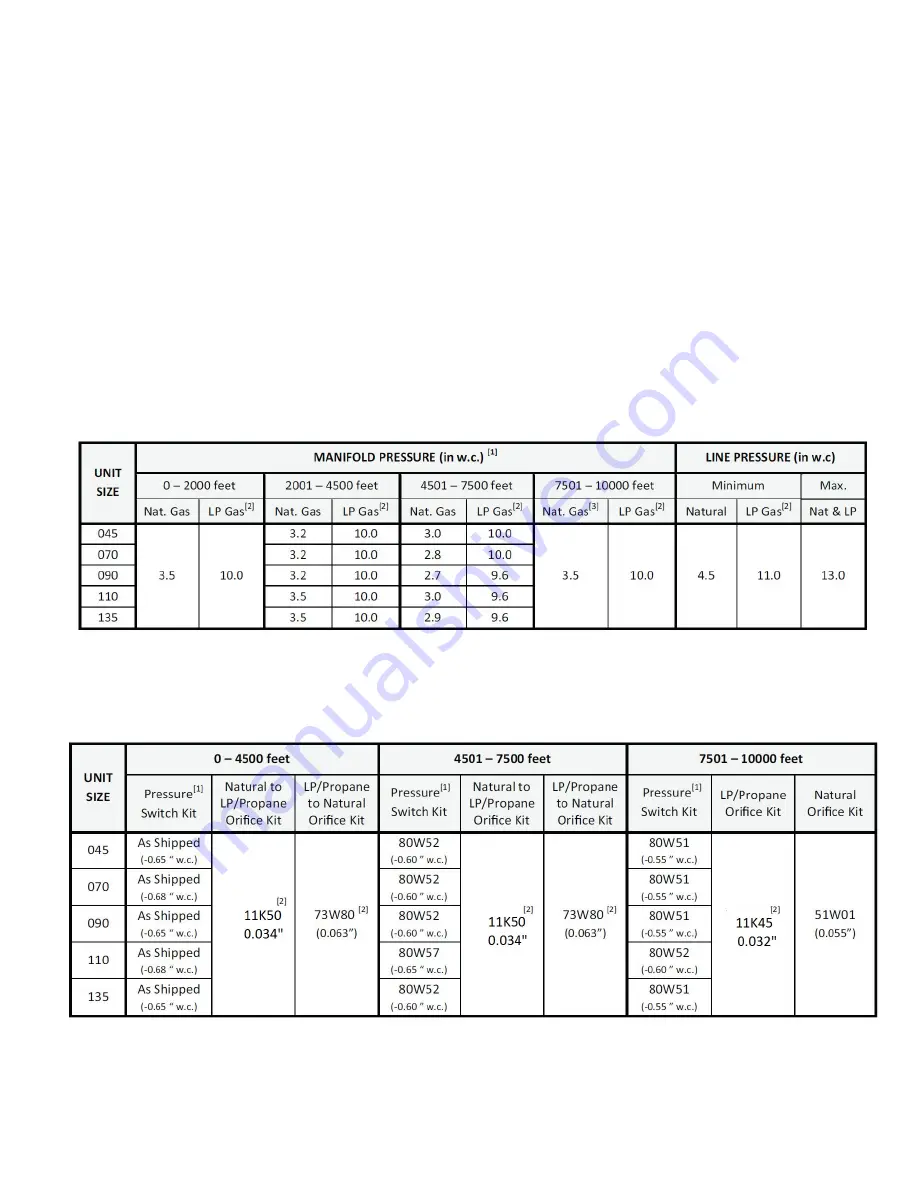
507713-01
Page 27 of 32
Issue 1623
High Altitude
This furnace is carefully designed for optimal performance under a wide range of operating conditions. To ensure proper operation at
higher altitudes, certain adjustments and/or kits may be required.
Manifold Pressure –
Between 2000 and 7500 ft, certain units require manifold pressure adjustments specified in Table 9. Manifold pressure should be
measured, and adjusted as required during unit start up. Note: LP/Propane installations require a gas conversion Orifice Kit as specified
in Table 10.
Pressure Switch –
Between 4501 and 7500 ft, some units may require a pressure switch change. Table 10 lists the available Pressure Switch Kits
providing the minimum allowable pressure switch set points, in this altitude range, for each unit. The need for a Pressure Switch Kit
may be evaluated by comparing the pressure measured at the pressure switch under steady state conditions (after 15 minutes of run
time) against the as shipped switch set point. Insufficient negative pressure may lead to nuisance pressure switch trips and possible
unit lock outs.
Above 7500 feet, all units require both a burner orifice change and a pressure switch change per Table 10
1. Manifold pressure adjustments based on 1020 Btu/ft
3
gas for natural and 2500 Btu/ft
3
gas for LP (corrected to standard conditions). Consult local utility
for actual local heating value.
2. A natural to LP/Propane gas conversion Orifice Kit is required to convert this unit. Refer to kit instructions for conversion procedure.
3. A high altitude natural Orifice Kit is required.
1. Minimum allowable set points for this altitude range. Application of a Pressure Switch with lower set point (less negative / closer to zero) is not
permitted.
2. Kit contains burner orifices and gas valve regulator spring(s).
Table 9 - Manifold Pressure and Line Pressure at Various Altitudes
Table 10 - Orifice Kits and Pressure switch kits at various Altitudes