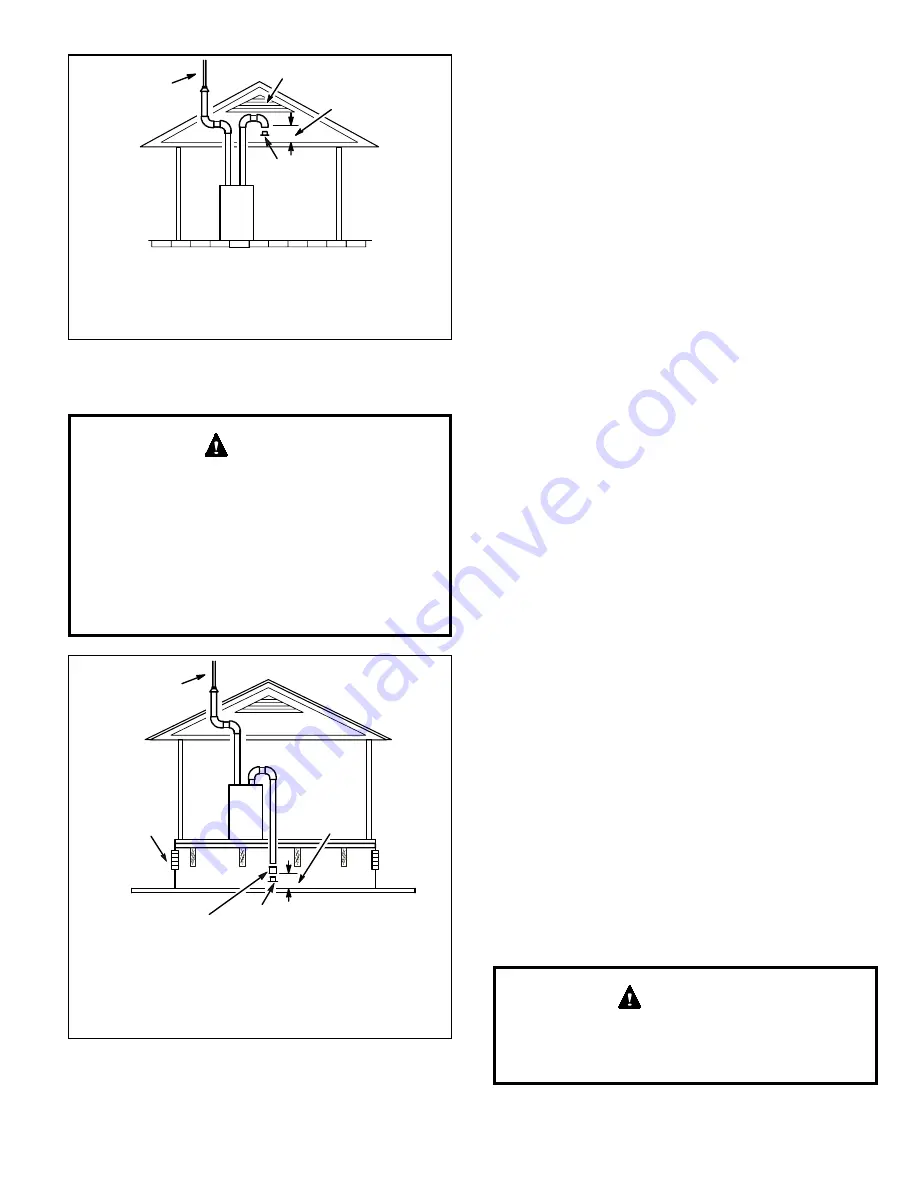
507735-03
Page 19 of 53
Issue 1933
Figure 25.
Equipment in Confined Space
(Inlet Air from Ventilated Attic and Outlet Air to
Outside)
Ventilation Louvers
Inlet Air
(Minimum 12 in.
(305mm) above
Attic Floor)
Roof Terminated
Exhaust Pipe
Furnace
*Intake Debris
Screen
(Provided)
* See Maximum Vent Lengths table
NOTE-The inlet and outlet air openings shall each have a
free area of at least one square inch per 4,000 Btu (645mm
2
per 1.17kW) per hour of the total input rating of all equipment
in the enclosure.
If this unit is being installed in an application with
combustion air coming in from a space serviced by an
exhaust fan, power exhaust fan, or other device which
may create a negative pressure in the space, take care
when sizing the inlet air opening. The inlet air opening
must be sized to accommodate the maximum volume
of exhaust air as well as the maximum volume of
combustion air required for all gas appliances serviced
by this space.
CAUTION
Figure 26.
Equipment in Confined Space
(Inlet Air from Ventilated Crawl Space and Outlet Air
to Outside)
Roof Terminated
Exhaust Pipe
Furnace
Ventilation
Louvers
(Crawl Space)
*Intake Debris Screen Provided
Inlet Air
Minimum
12 in. (305mm)
above Crawl
Space Floor
Coupling or
3 in. to 2 in.
Transition
(Field Provided)
* See Maximum Vent Lengths table
NOTE-The inlet and outlet air openings shall each have a
free area of at least one square inch per 4,000 Btu (645mm
2
per 1.17kW) per hour of the total input rating of all equipment
in the enclosure.
General Guidelines for Vent Terminations
In Non-Direct Vent applications, combustion air is taken
from indoors and the flue gases are discharged to the
outdoors. This unit is then classified as a non-direct vent,
Category IV gas furnace.
In Direct Vent applications, combustion air is taken from
outdoors and the flue gases are discharged to the outdoors.
This unit is then classified as a direct vent, Category IV gas
furnace.
In both Non-Direct Vent and Direct Vent applications, the
vent termination is limited by local building codes. In the
absence of local codes, refer to the current National Fuel
Gas Code ANSI Z223-1/NFPA 54 in U.S.A., and current
CSA-B149 Natural Gas and Propane Installation Codes in
Canada for details.
Position termination according to location given in Figure
27 or Figure 28. In addition, position termination so it is
free from any obstructions and 12” above the average
snow accumulation.
At vent termination, care must be taken to maintain
protective coatings over building materials (prolonged
exposure to exhaust condensate can destroy protective
coatings). It is recommended that the exhaust outlet not be
located within 6 feet (1.8 m) of a condensing unit because
the condensate can damage the painted coating.
NOTE:
If winter design temperature is below 32° F (0° C), it
is recommended that the exhaust piping be insulated with
1/2” (13 mm), Armaflex or equivalent when run through an
unconditioned area. In extremely cold climate areas with
temperature below 20° F (6.7° C) it is recommended that
3/4” (19 mm) Armaflex or equivalent be used. Insulation on
outside runs of exhaust pipe may be painted or wrapped
to protect insulation from deterioration in accordance with
the insulation manufacturers recommendation. Exhaust
pipe insulation may not be necessary in some specific
applications.
NOTE:
During extremely cold temperatures, below
approximately 20° F (6° C), units with long runs of vent
pipe through unconditioned space, even when insulated,
may form ice in the exhaust termination that prevents the
unit from operating properly. Longer run times of at least 5
minutes will alleviate most icing problems. Also, a heating
cable may be installed on exhaust piping and termination
to prevent freeze-ups. Heating cable installation kits are
available, see unit specification sheets for part numbers.
Do not use screens or perforated metal in exhaust
terminations. Doing so will cause freeze-ups and may
block the terminations.
IMPORTANT
Summary of Contents for Century GDD95C Series
Page 30: ...507735 03 Page 30 of 53 Issue 1933 Figure 50 Trap Drain Assembly Using 1 2 PVC or 3 4 PVC ...
Page 36: ...507735 03 Page 36 of 53 Issue 1933 045B3 070B4 090C4 110C5 Figure 57 Typical Wiring Diagram ...
Page 48: ...507735 03 Page 48 of 53 Issue 1933 Troubleshooting Heating Sequence of Operation ...
Page 49: ...507735 03 Page 49 of 53 Issue 1933 Troubleshooting Heating Sequence of Operation continued ...
Page 50: ...507735 03 Page 50 of 53 Issue 1933 Troubleshooting Cooling Sequence of Operation ...
Page 51: ...507735 03 Page 51 of 53 Issue 1933 Troubleshooting Continuous Fan Sequence of Operation ...