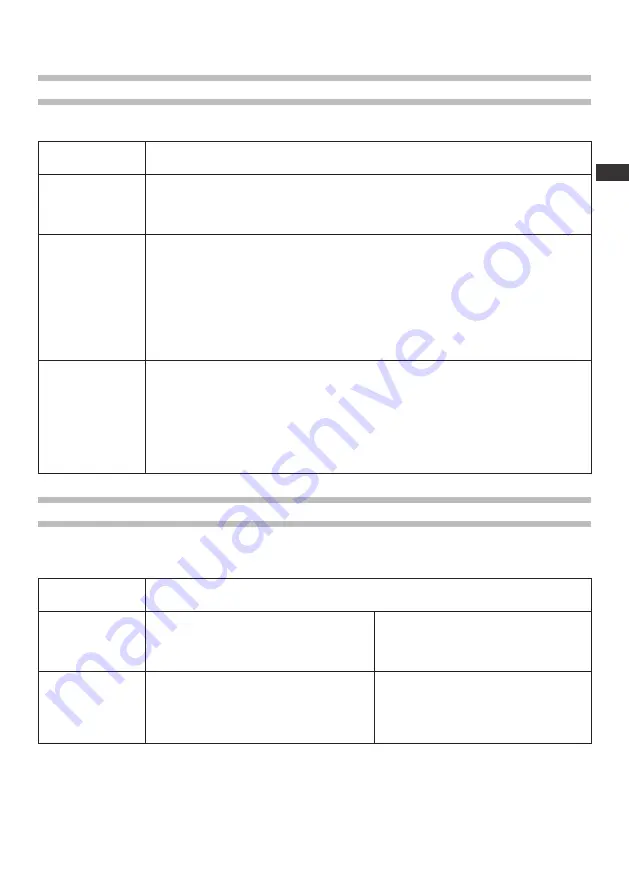
29
• Store the high pressure cleaner in a clean, dry place. Make sure the power cord and the high pressure
hose are not damaged.
ROUTINE MAINTENANCE
Follow the instructions for
“STOPPING WORK”
and those provided in the table below.
MAINTENANCE
SCHEDULE
ACTION
Every time the
cleaner is used
• Check the power cord, the high pressure hose, the connectors, the cleaner gun and
the lance pipe.
Should any of these look damaged, do not use the cleaner for any reason and
contact a
QUALIFIED TECHNICIAN
.
Once a Week
• Check the water inlet filter (18) and clean it if necessary.
Use a coin
(Fig. 6)
to turn the screw anticlockwise (37) and remove it; press the
lever (38) downwards and remove the cover (33) Unscrew the whole filter and
remove the filter cartridge.
Running water or compressed air is generally all that is needed to clean the filter
cartridge. In difficult cases, use a lime scale remover or replace the filter cartridge.
For tough cases, use a lime scale remover or replace it by contacting a
QUALIFIED
TECHNICIAN
to buy the spare part.
Replace the filter and put the cover back, following the above steps in reverse order.
Once a Month
• Clean the nozzle.
To clean the nozzle, it is generally sufficient to insert the pin (31) supplied into the
nozzle’s hole. If no appreciable results are obtained, contact a
QUALIFIED TECHNICIAN
to buy the spare part . The nozzle can be replaced using a 14 mm/0.55” spanner
(not supplied).
• Check the pump oil level.
Use the dipstick (51)
(Fig. 6)
. If you need to top up the oil, contact a
QUALIFIED
TECHNICIAN.
SUPPLEMENTARY MAINTENANCE
Supplementary maintenance should only be carried out by a
QUALIFIED TECHNICIAN
, following the
table below (guideline only).
MAINTENANCE
SCHEDULE
ACTION
Every 200 hours
• Check the pump’s hydraulic circuit
(water).
• Check the pump is firmly secured
• Adjust the electrodes
• Clean the fuel nozzle.
• Check/replace the fuel filter.
• Check/replace the water filter
Every 500 hours
• Change the pump oil
• Replace the electrodes
• Replace the fuel nozzle.
• Check the pump delivery/suction valves.
• Check the tightness of pump screws.
• Check the pump’s adjustment valve
• Clean the boiler.
• Remove any lime scale on the heating
element
(“CLASSIC” version only)
.
• Check the safety devices
EN
Summary of Contents for KF classic
Page 2: ......
Page 4: ...1 2 11 9 7 20 28 8 33 34 4 13 3 17 6 16 5 39 10 4 ...
Page 5: ...2 10 4 4 1 41 42 44 CLASSIC 4 1 41 48 44 49 42 45 46 47 EXTRA ...
Page 6: ...5 4 3 24 21 30 31 36 35 43 24 S 22 23 a b 30 40 39 M 29 27 25 26 50 17 ...
Page 7: ...6 51 28 28 32 18 37 33 38 19 ...
Page 8: ...8 35 12 43 15 14 36 1 2 A C E D B 2 1 7 ...
Page 9: ......
Page 220: ...NOTE ...
Page 221: ...NOTE ...
Page 222: ...NOTE ...
Page 223: ......