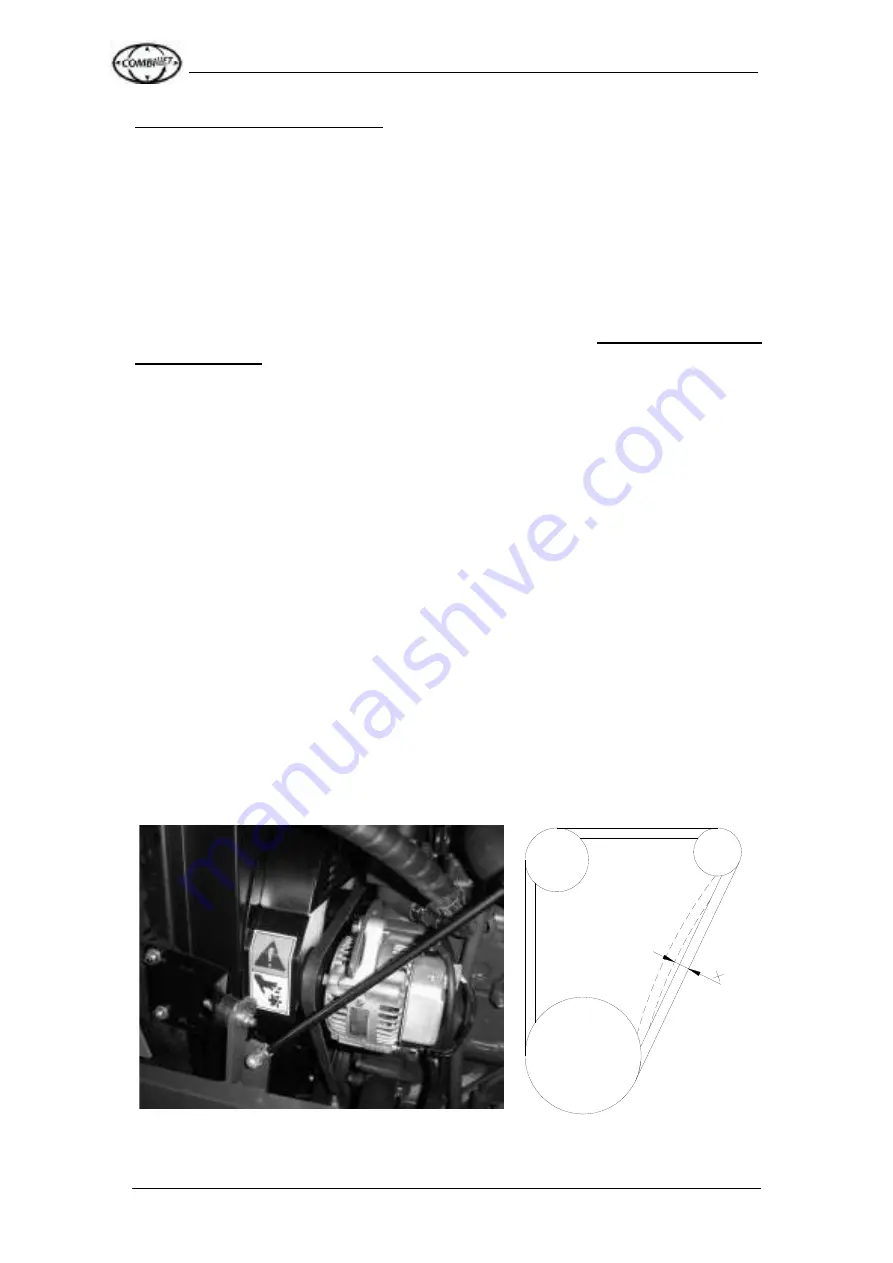
Combilift Ltd.
C4000-C5000XL O&S Manual
4-13
C4000-OM-EN-08
Additional Mast Maintenance (Contact Combilift for further information)
Replacement of hydraulic cylinder seals.
Replacement of chains.
Replacement of bearings.
4.7: Greasing Mast Carriage Channels
The mast carriage channels must be greased periodically only on the vertical
(side) surfaces where the wear pads run. The frequency of this operation is at
the discretion of the user and essentially depends upon the working conditions
and the workplace. A lubrication interval of about 250 hours can be taken as a
typical value, under normal working conditions. For this purpose use EP2
grease.
4.8: Water Pump V- Belt
The engine is kept cool via the coolant that is pumped round the cooling
system. The water pump is powered by the Water pump V-belt. This is located
on the engine as shown and checked as follows:
Check the belt tension. Perform this when the engine IS NOT running. Press
on the belt with a stick or rod. Ensure that the deflection is no more that 10mm
to 12mm. If it is adjust the belt via the pulley adjusting bolts
Check the belt condition: Inspect the condition of the belt. Be on the look out
for signs of damage and wear. If the belt is damaged replace it immediately.
Also check if the belt has sunk deeply into the pulley as this indicates
excessive wear. Again replace the belt immediately if this is the case.
https://www.forkliftpdfmanuals.com/