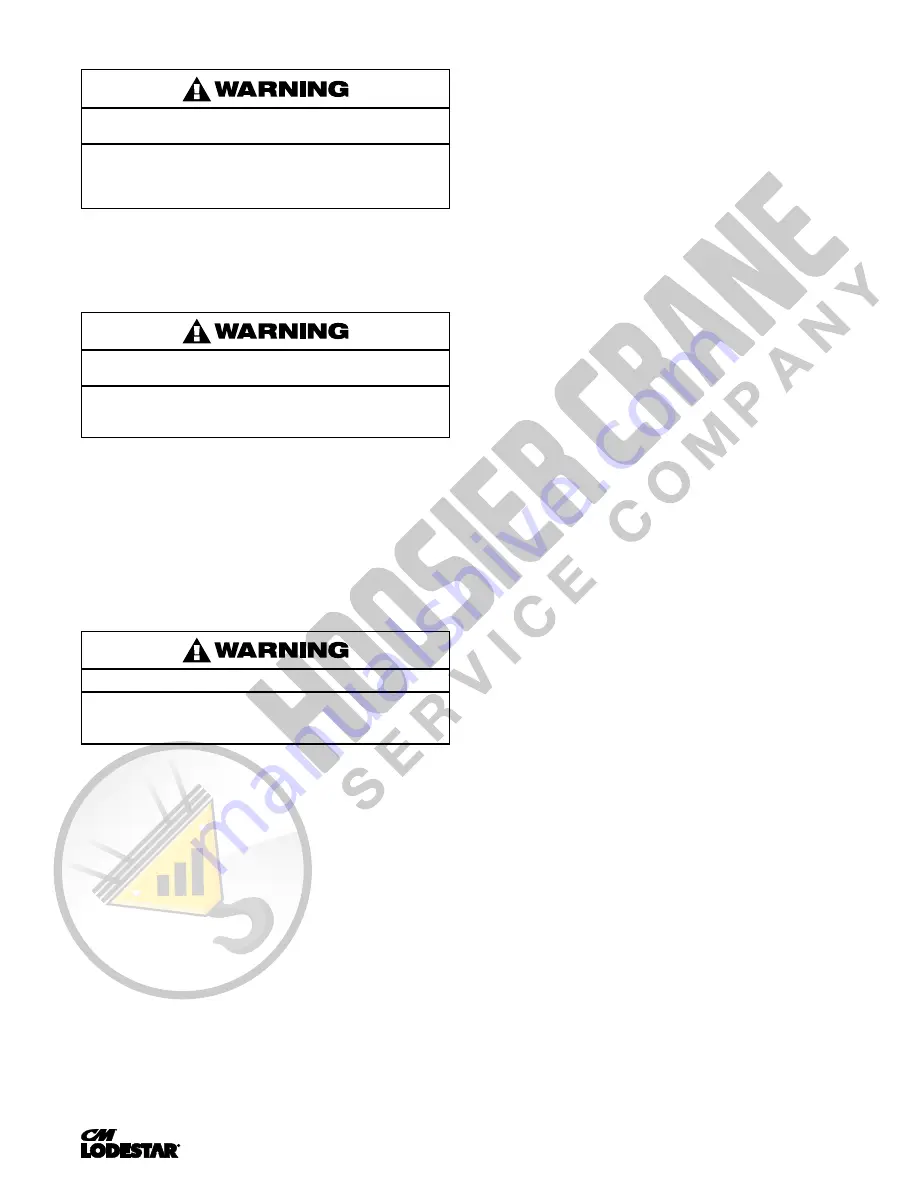
4
P/N: 10001609 (REV AB) 627NH
December 2014
Failure to provide a proper power supply system for the hoist may
cause damage and offers the potential for a fire.
tO aVOiD inJURY:
Provide the hoist with a overcurrent protected power supply
system per the National Electrical Code and applicable local
codes as instructed in this manual.
Remember, operation with low voltage can void the CM repair/
replacement policy. When in doubt about any of the electrical
requirements, consult a qualified electrician.
Always disconnect the power from the power supply system and
lockout/tagout disconnecting means before servicing the hoist.
Working in or near exposed energized electrical equipment
presents the danger of electric shock.
tO aVOiD inJURY:
Disconnect power and lockout/tagout disconnecting means
before removing cover or servicing this equipment.
nOtE: the brake coil voltage must be the same as the hoist
line voltage. this must be a consideration when ordering
a repair brake coil.
OPERATING INSTRUCTIONS
Follow the operating instructions in the hoist manual and use
the following:
The hoist is supplied with dynamic braking resistors. During
normal hoist operation these resistors get very hot (300ºF or
more). These resistors must never be touched while the hoist is
in operation. They should be allowed to cool to room temperature
before inspection or servicing the hoist.
Dynamic braking resistors get very hot during normal hoist operation.
tO aVOiD inJURY:
Never touch the dynamic braking resistors while the hoist is in
operation. Allow resistors to cool before servicing.
1. The adjustable frequency drives are programmed on a per order
basis (see Speed Control Methods on page 23) to provide:
a. 1 step control. In this method, the hoist can be operated as
a normal single speed hoist. Depress the up or down push
button and the hoist speed will gradually increase to the
rated speed of the hoist.
b. 2 step control. In this method, the hoist can be operated as
a normal two speed hoist. Partially depress the up or down
push button for slow speed operation and fully depress the
button for fast speed operation.
c. 3 step control. In this method, the hoist can be operated
as a normal three speed operation. Partially depress the
up or down push button for slow speed operation. Depress
the button to the intermediate position for second speed
operation and fully depress the button for fast speed
operation. The hoist speed gradually increases to the
next speed point.
d. 2 step infinitely variable control. Partially depress the up or
down push button and the speed of the hoist will gradually
increase to the slow speed point. Fully depress the button
and the speed of the hoist will gradually increase to fast
speed operation. Slowly release or depress the up or down
push button and the hoist will operate at a speed between
the preset speed points.
e. 3 step infinitely variable control. Partially depress the up or
down push button and the speed of the hoist will gradually
increase to the slow speed point. Depress the button to
the intermediate position and the speed of the hoist will
gradually increase to the second speed. Fully depressing
the button will cause the hoist to gradually increase to fast
speed. Slowly release or depress the up or down push
button and the hoist will operate at a speed between the
preset speed points.
SAFETY PROCEDURES
Refer to the hoist manual and:
1. When preparing to lift a load, be sure that the attachments
to the hook are firmly seated in hook saddle. Avoid off center
loading of any kind, especially loading on the point of hook.
2. When lifting, raise the load only enough to clear the floor or
support and check to be sure that the attachments to the
hook and load are firmly seated. Continue lift only after you
are assured the load is free of all obstructions.
3. Do not load hoist beyond the rated capacity shown on hoist
identification plate. Overload can cause immediate failure of
some load-carrying part or create a defect causing subsequent
failure at less than rated capacity. When in doubt, use the next
larger capacity hoist.
4. Do not use this or any other overhead materials handling
equipment for lifting persons.
5. Stand clear of all loads and avoid moving a load over the heads
of other personnel. Warn personnel of your intention to move a
load in their area.
6. Do not leave the load suspended in the air unattended.
7. Permit only qualified personnel to operate unit.
8. Do not wrap the load chain around the load and hook onto itself
as a choker chain. Doing this will result in:
a. The loss of the swivel effect of the hook which
could mean twisted chain and a jammed liftwheel.
b. The upper limit switch, on certain hoists, is
by-passed and the load could hit the hoist.
c. The chain could be damaged at the hook.