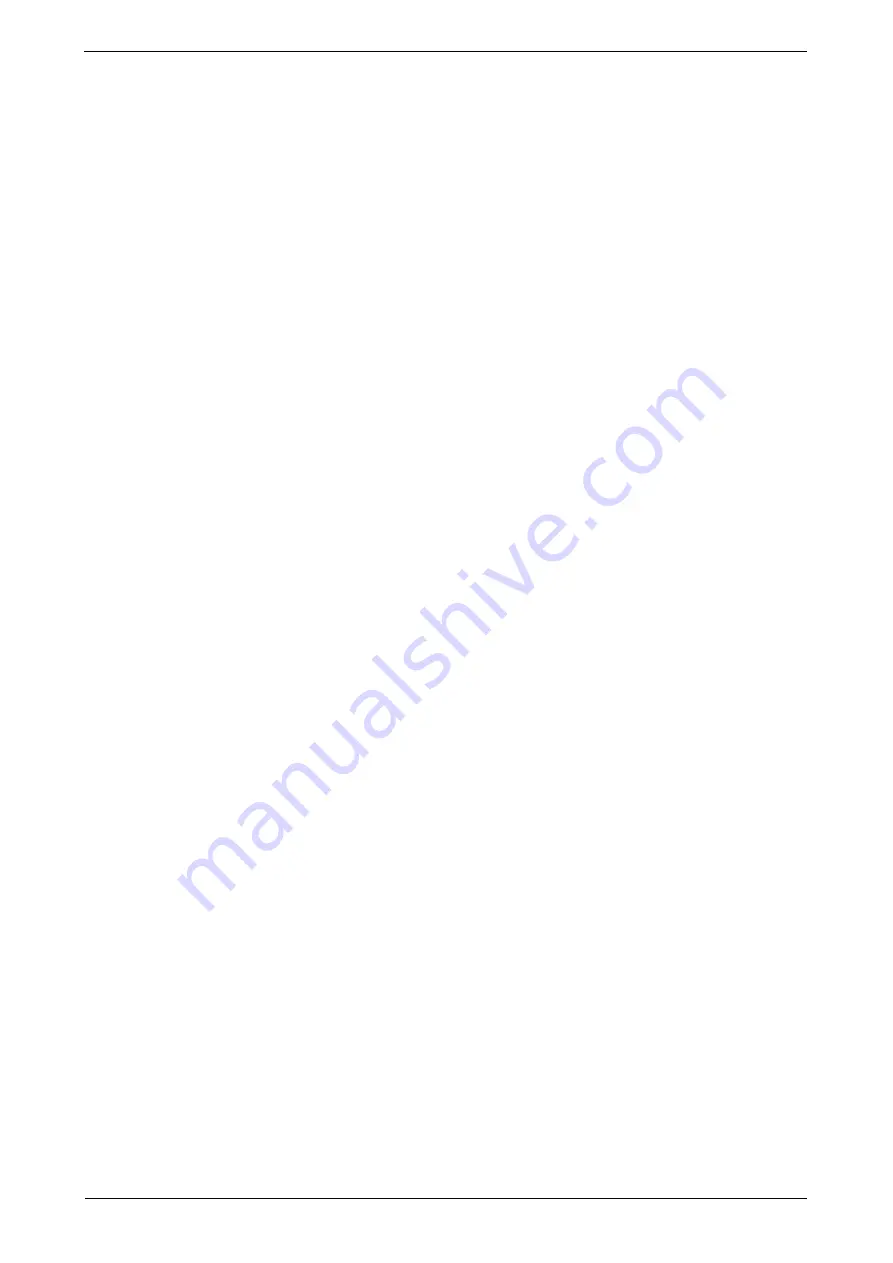
COFFE
tek
LTD
NEVA 4
Issue 1
22/02/08
14
Section 2
Programming
INTRODUCTION
1.
The Neva 4 Beverage Machine provides two discrete user programs: The Operator’s
Program and the Engineer’s Program. The Operator’s Program is available to both the
Operator and the Service Engineer, but the Engineer’s Program is only available to the
Service Engineer.
2.
Both the programs are stored in programmable read only memory on the Controller
Board. The values and settings (Variables) which the program allows the programmer to
alter are stored in NVRAM (non-volatile random access memory).
3.
Settings are maintained, without the need for back-up battery, when the power supply is
removed.
Summary of Contents for NEVA 4
Page 1: ...NEVA 4 BEVERAGE MACHINE TECHNICAL MANUAL ...
Page 3: ...COFFEtek LTD 3 22 02 08 Issue 1 NEVA 4 This page is intentionally blank ...
Page 5: ...COFFEtek LTD 5 22 02 08 Issue 1 NEVA 4 This page is intentionally blank ...
Page 12: ...COFFEtek LTD NEVA 4 Issue 1 22 02 08 12 ...
Page 13: ......
Page 25: ...COFFEtek LTD 25 22 02 08 Issue 1 NEVA 4 This page is intentionally blank ...
Page 36: ...COFFEtek LTD NEVA 4 Issue 1 22 02 08 36 Section 4 Exploded Parts Diagram ...
Page 37: ...COFFEtek LTD NEVA 4 Issue 1 22 02 08 38 ...
Page 38: ...COFFEtek LTD 39 22 02 08 Issue 1 NEVA 4 ...