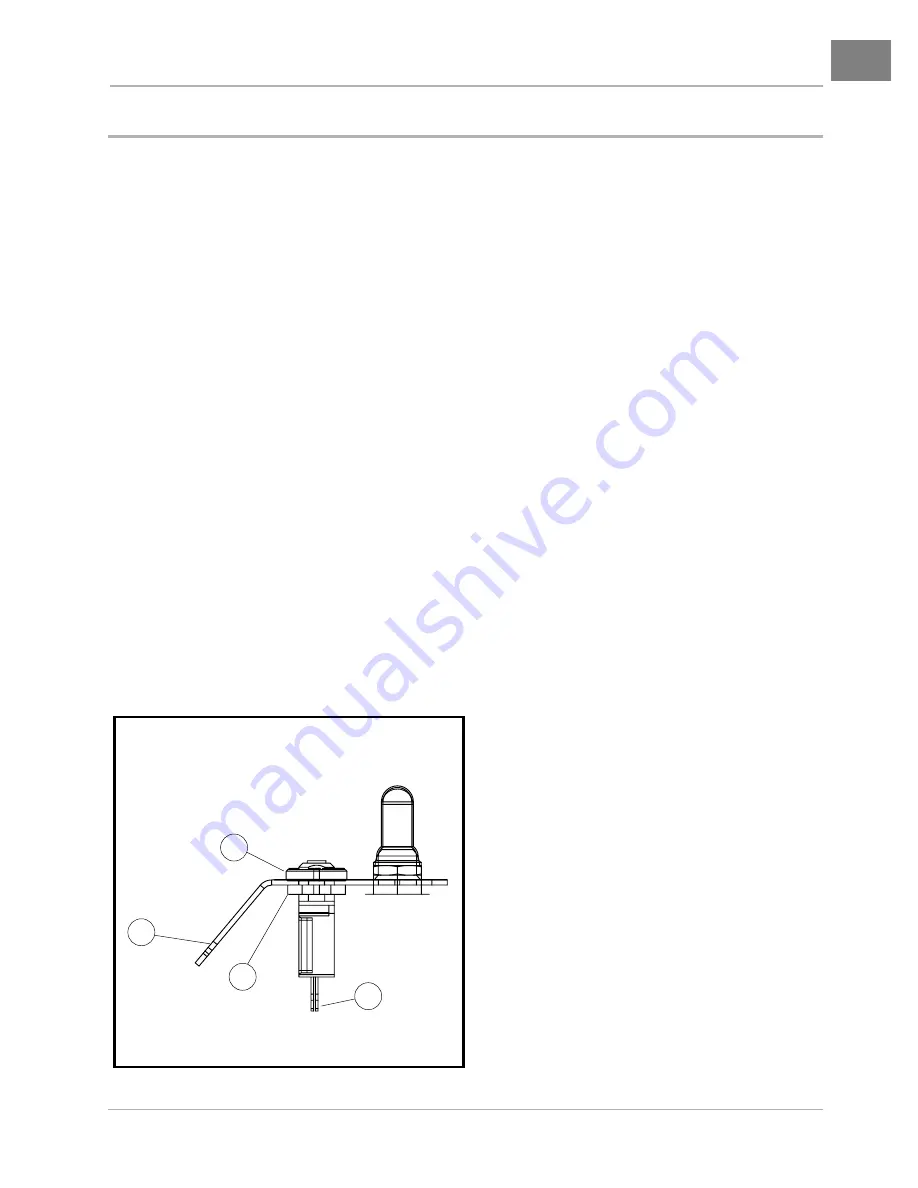
ELECTRICAL COMPONENTS
Circuit Breaker
2006 IQ Plus System Electric Vehicle Maintenance and Service Supplement
Page 13-5
13
CIRCUIT BREAKER
See General Warning, Section 10, Page 10-1.
Testing the Circuit Breaker
See Test Procedure 7, Section 11, Page 11-23.
Circuit Breaker Removal
1. Disconnect the battery cables as instructed.
See WARNING “To avoid unintentionally starting...” in
General Warning, Section 10, Page 10-1.
2. Remove the plastic nut (1) from the circuit breaker
.
3. Remove circuit breaker and metal nut (2) from bracket (3).
4. Disconnect tan and green wires from the spade connectors (4) on the back of the circuit breaker.
Circuit Breaker Installation
1. Installation is reverse of removal. Connect tan and green wires to the spade connectors (4) on the back
of the circuit breaker.
See following NOTE.
NOTE: The spade connectors are not polarity-sensitive. It does not matter what color wire goes to either
of the spade connectors.
2. Insert the circuit breaker and metal nut (2) into the bracket (3).
3. Replace the plactic nut (1) on the circuit breaker.
4. Place the Tow/Run switch in the TOW position and connect the battery cables, positive (+) cable first.
Tighten battery terminals to 110 in-lb (12.4 N·m) and coat terminals with Battery Terminal Protector Spray
(CCI P/N 1014305) to minimize corrosion.
Figure 13-4 Circuit Breaker
3
1
2
4