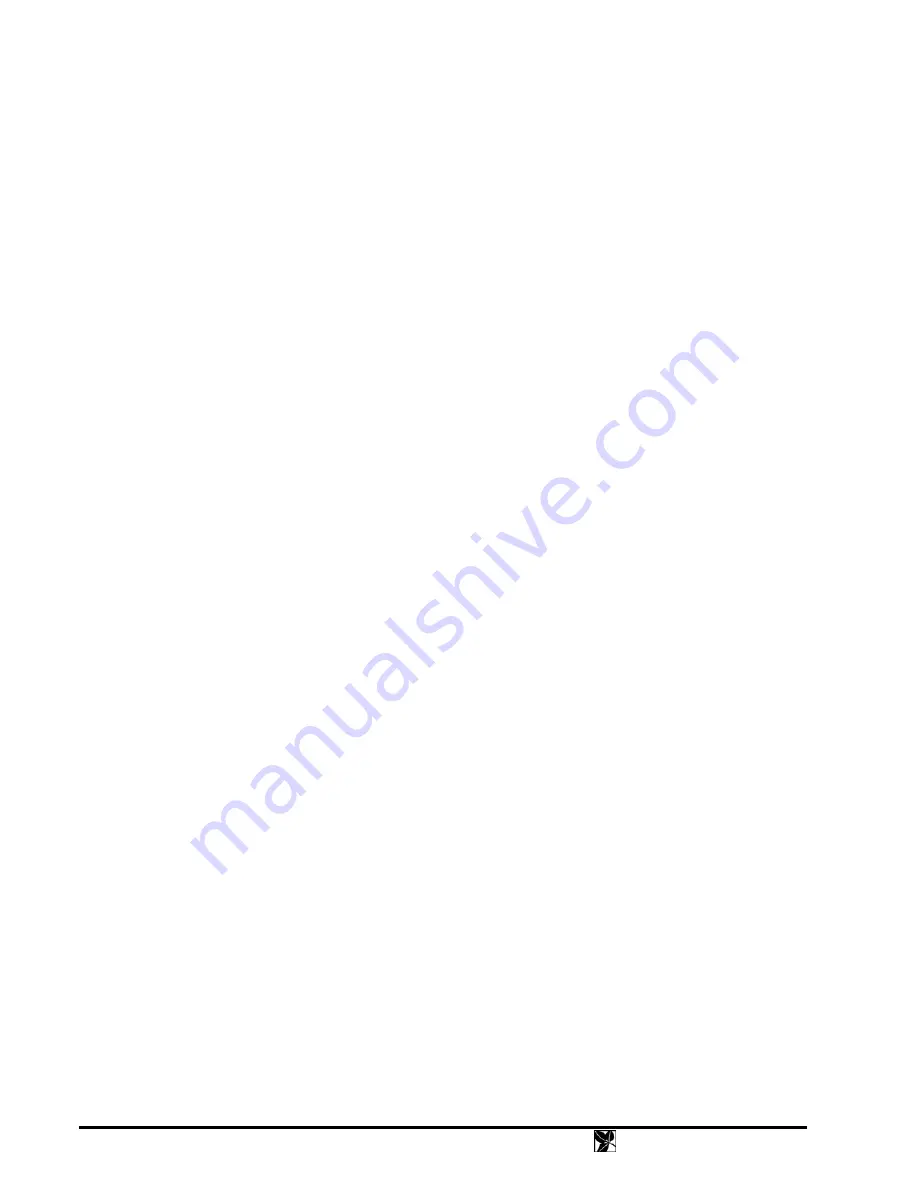
46
DVX
Instruction
Manual
MAJOR CAUSES OF DISC FAILURE
The most common cause of disc failure is
scratches and dirt
due to handling.
With molded discs that have not been handled, the most common cause of defects is a
defective master or stamper
.
This is true because any defect on the stamper will be faithfully reproduced on every disc.
With DVD/CD-Recordables, the most common problem
is incompatibility between the writer and the media
. Often
the case is that the recording speed is too high for the type of media being used. Generally, higher recording speeds
produce poorer results. This problem usually manifests itself as high error rates across the whole disc. Another
common cause of problems is a speck of dust or dirt on the disc (readout) surface when recording. This blocks the
recording beam, producing a void, where there are no “pits”. Likewise, bubbles or black spots in the disc substrate can
cause the same problem. These type of errors show up as local defects, for example like in fig. 9 on page 22.
Quality Clues
Most problems are traceable to the disc. Often people will encounter a situation where a disc works in one drive, but
not another. The tendency is to blame the drive, concluding that “the disc must be good because it plays in this other
drive”. However, almost certainly it is the disc that is at fault. Since there are no standards for players (other than that
they must play a disc that meets the standards), a disc that is outside the Red Book or DVD specs may play on some
drives, but not others.
The solution is that all discs must conform to the standards. Discs that are made well within Red Book or DVD
standards should play on any player.
A disc that behaves erratically is invariably bad. A disc that is outside the specs (or marginal) will behave in a way that
is not predictable. If a discs produces different results each time you test it, that tells you that the disc does not meet
Red Book (or DVD) specs.
DISC DUPLICATION TIPS
How to Test Blank Media
DVX will measure Focus Error and Tracking Error on a blank disc (CD or DVD). To do this, load the disc, and wait
for it to initialize. Then select the "Blank Test" checkbox in the main screen, then press "Start".
Although some things can be measured on a blank disc, none of these things will predict how the disc will work. The
recording action is in the dye layer, and the only way to test the dye is to record on it.
We recommend that you record the full disc (74 or 80 minutes) at the speed you wish to use in production. This is
important because defects are more common at the outside of the disc. Then do the Error Test to measure the results.
Analog pit geometry measurements are especially useful for qualifying new media.
Since the media is generally quite consistent within a batch, it is only necessary to test one or two samples from each
batch of new media.
You will also find that the results vary according to the recording speed. Generally, results are worse at the highest
speeds. Ideally, you should make full test recordings at several different speeds to discover what is the highest speed
that will give satisfactory results.
Hints for Producing Good Discs
•
The number one issue is compatibility between the writer and the media. There isn't necessarily a "best" writer
or "best" media; some combinations work better than others. The writer’s laser power and write strategy must
match the type of media used. Both media and writers have evolved over the years, so there are many
opportunities for mis-match.
•
Use DVX to determine the best type of media for your application. Most major brands will produce good
results with modern writers. But anybody can make a bad batch. The media is pretty consistent within a
batch, so if there is a manufacturing defect, every disc will be bad. We have gotten bad batches from most
major manufacturers. Defects range from stamper defects to bubbles in the plastic, to dirty discs and dye layer
coating problems. We have had to change brands several times over the years when a particular brand’s