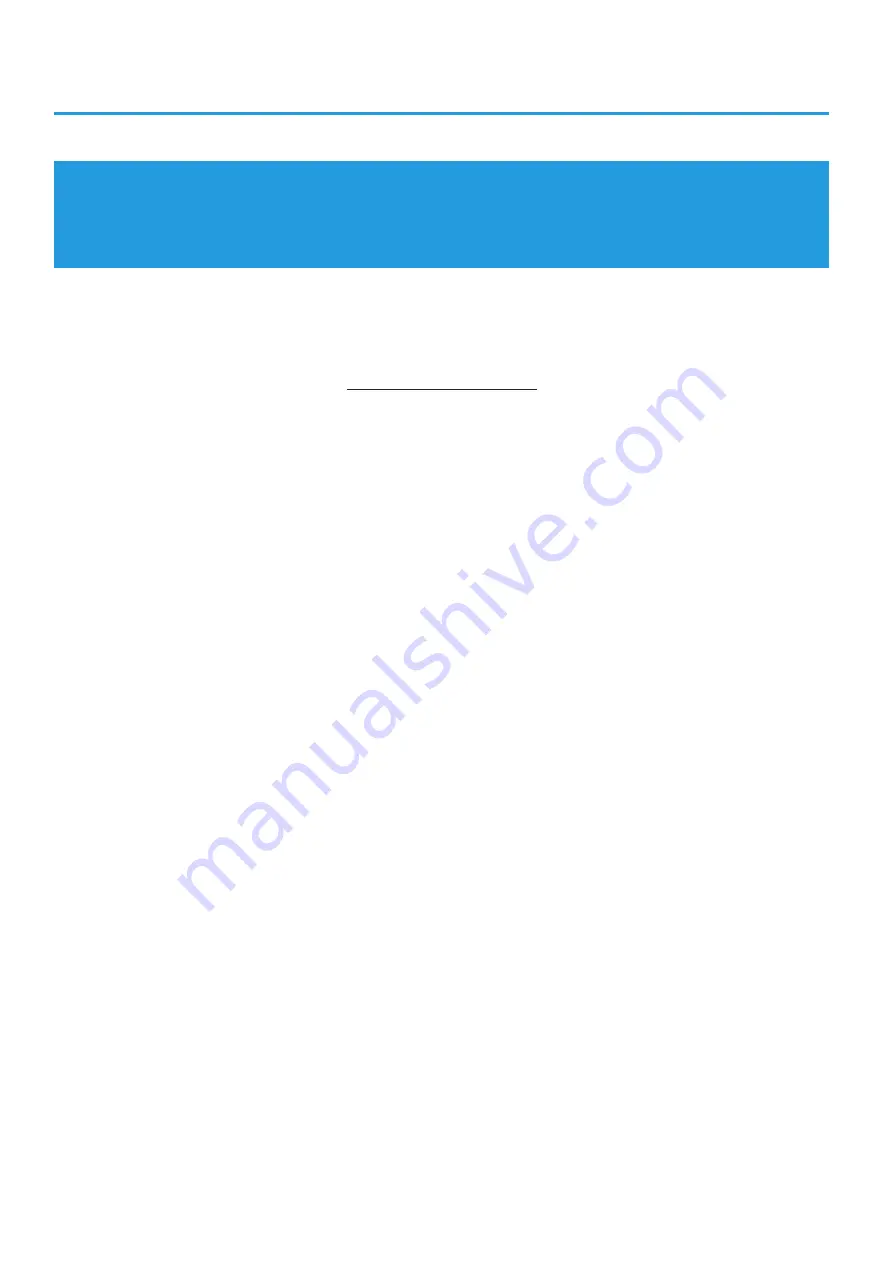
Contents
Accessories .....................................................................................................................
4
0
1.
Installation Overview ..........................................................................................
4
1
2.
Location Selection ...............................................................................................
4
2
3.
Indoor Unit Installation .......................................................................................
4
3
4.
Outdoor Unit Installation ....................................................................................
4
4
5.
Drainage Pipe Installation ...................................................................................
4
5
6.
Refrigerant Pipe Installation ...............................................................................
4
7
7.
Vacuum Drying and Leakage Checking ..............................................................
4
9
8.
Additional Refrigerant Charge ...........................................................................
5
0
9.
Engineering of Insulation ...................................................................................
5
0
10.
Engineering of Electrical Wiring ........................................................................
5
1
11
Panel Installation
............................................................................................
5
2
12
Test Operation
.................................................................................................
5
3
Installation