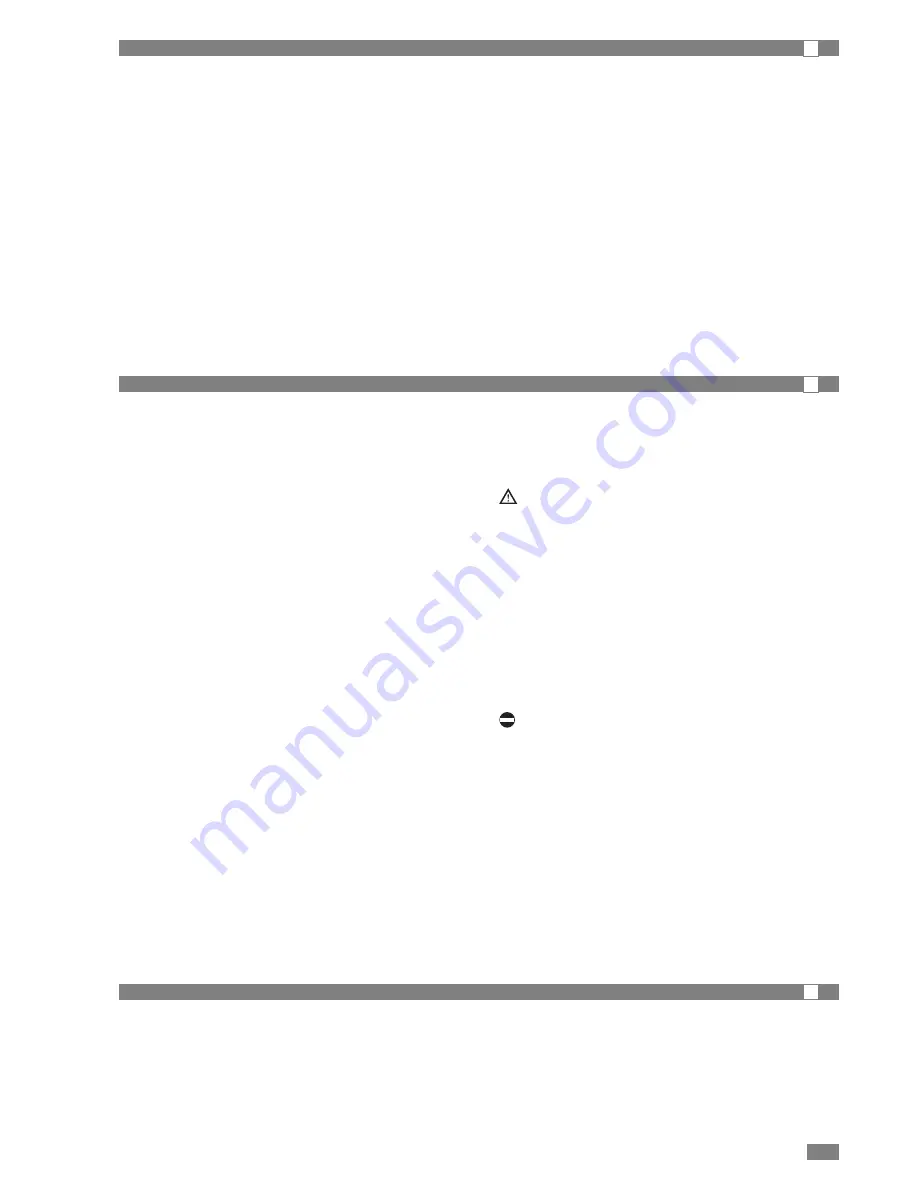
49
GB 01/2009
AWR MTD - AWR MTD/B
ROUTINE MAINTENANCE
A
SPECIAL MAINTENANCE
A
Never perform any cleaning operations
before having
disconnected the unit from the mains power supply.
Terminals 6, 7, 8 and 9 may be live even when the unit has
been disconnected..
Check for voltage before proceeding.
CHEMICAL WASHING
It is recommended to chemically flush the plate heat
exchanger after every 3 years of operation.
For instructions on how to carry out this operation, call the
toll free number.
REFRIGERANT GAS CONTENT
The chillers are charged with R410A refrigerant gas and
tested in the factory.
In normal conditions, there should be no need for the Tech-
nical Service to intervene to check the refrigerant gas.
However, over time, small leaks may develop at the joints
leading to loss of refrigerant and draining of the circuit,
causing the unit to function poorly.
In this case, the leaks of refrigerant must be identified and
repaired and the refrigerant circuit recharged.
Proceed as follows:
- Empty and dry the entire refrigerant circuit using a vacuum
pump connected to the low and high pressure tap until the
vacuometer reads about 10 Pa.
Wait a couple of minutes and check that this value does
not rise to more than 50 Pa.
- Connect the refrigerant gas cylinder or a filling cylinder to
the low pressure line pressure gauge connection
- Charge the quantity of refrigerant indicated on the unit’s
rating plate.
- Always check the superheat and subcooling values, which
should be between 5 and 10 °C and 4 and 8 °C.
- After a couple of hours operation, check that the liquid
indicator indicates a dry circuit (dry-green).
In the event of partial leaks
, the circuit must be com-
pletely emptied before being recharged.
The R410A refrigerant
must only be charged in the liq-
uid state.
Operating conditions
other than rated conditions may
produce considerably different values.
Tightness testing
or identification of leaks must only be
carried out using R410A refrigerant gas, checking with a
suitable leak detector.
The refrigerant circuit
must not be charged
with a
refrigerant other than that indicated on page 16.
The use of a different refrigerant may cause serious
damage to the compressor.
Oxygen, acetylene or other flammable or poisonous gas-
es
must never be used
in the refrigerant circuit as they
may cause explosion or poisoning.
Oils other than those indicated on page 16
must not be
used
.
The use of a different oil may cause serious damage to
the compressor.
Never perform any cleaning operations
before having
disconnected the unit from the mains power supply.
Terminals 6, 7, 8 and 9
may be live even when the unit has
been disconnected.
Check for voltage before proceeding.
Regular maintenance is fundamental to maintain the effi-
ciency of the unit both in terms of operation and energy con-
sumption.
The Technical Service maintenance plan must be observed,
with an annual service which includes the following opera-
tions and checks:
- Filling of the water circuit;
- Presence of air bubbles in the water circuit;
- Efficiency of safety devices;
- Power supply voltage;
- Power input;
- Tightness of electrical and water connections;
- Condition of the compressor contactor;
- Efficiency of the plate heat exchanger heater;
- Verification of operating pressure, superheat and subcool-
ing
- Efficiency of the compressor heater
- Cleaning of the finned coil every three months
- Cleaning of the fan grills
- Cleaning of condensate drain pan (if installed);
For units installed near the sea, the intervals between main-
tenance should be halved.
DISPOSAL
A
The unit must be disposed of
according to the legislation
in force in the country concerned