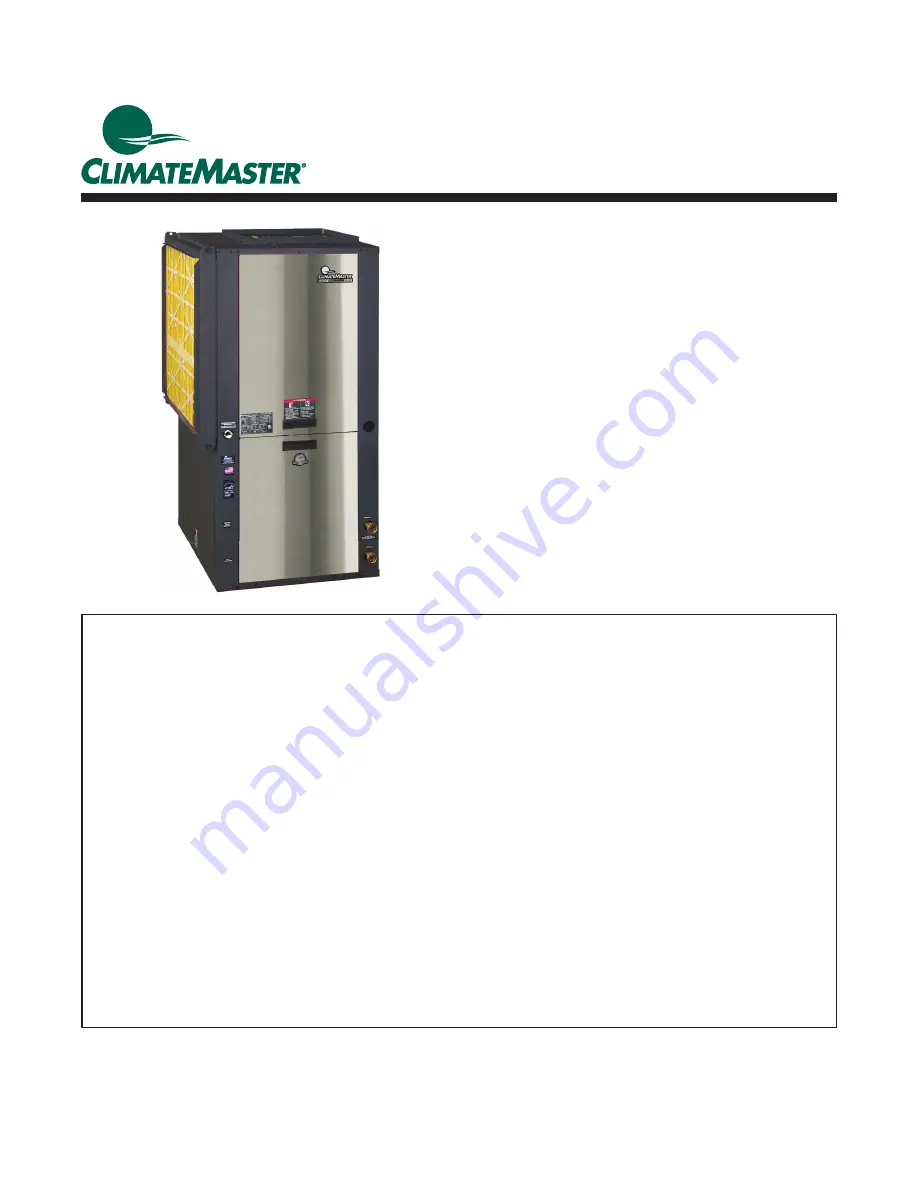
97B0119N01
Residential Horizontal, Vertical & Downfl ow
Packaged Geothermal Heat Pumps
Installation, Operation &
Maintenance Instructions
Created: 4 October, 2019
Trilogy
®
Variable
(VE) Series IOM
Table of Contents
Model Nomenclature
3
General Information
4
Vertical Installation
5-6
Horizontal Installation
7-10
Condensate and Water Connection
11
vFlow
™
Heat Pump Applications Overview
12
Closed Loop Heat Pump Applications
with Internal Flow Controller
13-14
Flushing the Earth Loop
15-17
Multiple Unit Piping and Flushing
18-20
Ground Loop Heat Pump Applications
21-22
Electrical - Line Voltage
23
Electrical - Low Voltage Wiring
24
Electrical - Thermostat Wiring
25
EXM Wiring Diagram
26-27
ECM Blower Control
28
ECM Blower Performance Data
29
System Confi guration
30-34
Unit Commissioning and Operating Conditions
35
Unit Start-Up and Operating Conditions
36
Unit Start-Up Procedure
37
Unit Operating Conditions
38-39
Performance Data - 0930 - Heating
40-41
Performance Data - 0930 - Cooling
42-43
Performance Data - 1860 - Heating
44-45
Performance Data - 1860 - Cooling
46-47
Performance Tables Legend
48
Preventive Maintenance
49
Troubleshooting
50-59
Refrigeration Troubleshooting Form - Heating
60-61
Refrigeration Troubleshooting Form - Cooling
62-63
Warranty
64
Revision History
68