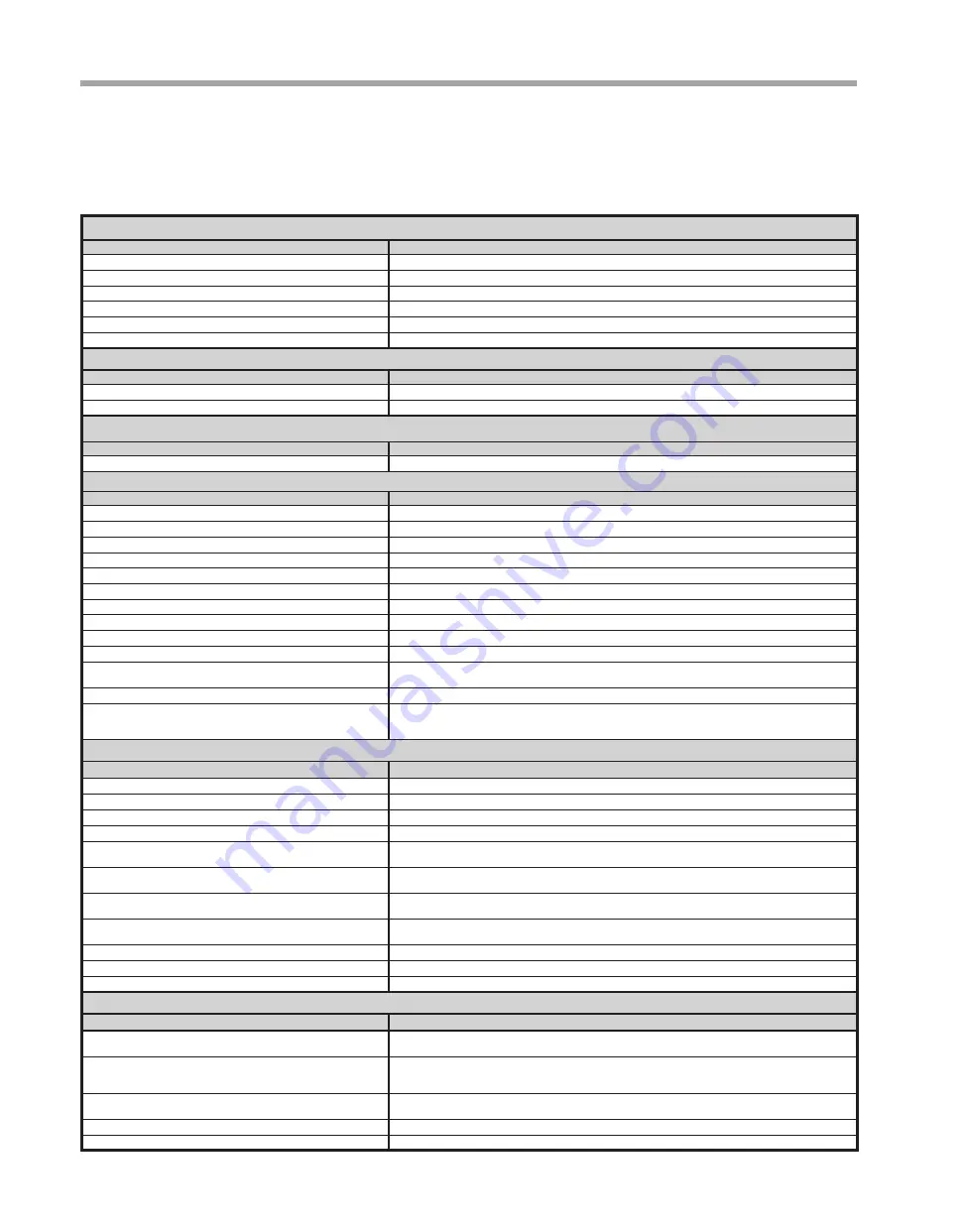
C L I M AT E M A S T E R WAT E R - S O U R C E H E AT P U M P S
Tranquility
®
Large Water-to-Water (TMW) Series
R e v. : O c t o b e r 5 , 2 0 2 1
C l i m a t e M a s t e r Wa t e r-S o u rc e H e a t P u m p s
58
Troubleshooting Guide
Unit Will Not Start
Possible Cause
Remedy
Power off
Check main disconnect switch
Main Line open
Check main fuses
Incorrect wiring
Check the wiring diagram
Loose terminals/connections
Tighten the terminal connections
Control Circuit open
Check interlocks with auxiliary
Improper phasing of main power
Change any two of three phases of main power
Compressor Hums but Does Not Start
Possible Cause
Remedy
Low voltage
Check at main power entry and power entry at unit (consult power company if low)
Phase Loss
Check power wiring and fuses
Compressor Runs but Does Not Cool or Heat
Possible Cause
Remedy
Improper phasing of main power
Switch any two of three phases of main power
Compressor Cuts Out on Low Pressure Safety Control
Possible Cause
Remedy
Main water valve closed or restricted
Open valve to full open position
Water isolation valves, if provided, closed or restricted
Open valves to full open position
Low water flow
Check water pump operation
Low water flow
Check water flow through the unit
Refrigerant shortage
Check for leaks - add refrigerant
Fouled Load brazed plate heat exchanger
Clean-in-place heat exchanger. See section on heat exchangers.
Restriction in liquid line
Plugged liquid line drier - replace liquid line drier
Expansion valve clogged or inoperative
Repair/Replace the expansion valve
Low discharge pressure
Raise and control discharge pressure within design limits
Load water temperature too cold or hot
Check water temperature setpoint
Improper Load water circulation
Use an ample sized cleanable strainer in the water circuit; make certain the strainer is clean to ensure full
flow of water (strainer screen must be 60 mesh minimum)
Faulty suction pressure transducer
Verify transducer calibration using a calibrated manifold gauge and replace if defective.
Wrong suction pressure cutout setpoint
Verify suction pressure cutout setpoint to be set equal to the corresponding leaving chilled solution freeze
temperature equivalent pressure on a PT chart. (i.e. if the solution freeze point is 32°F the equivalent
pressure setpoint will be 101 PSIG)
Compressor Cycles on High Pressure Control
Possible Cause
Remedy
Main Source water valve closed or restricted
Open valve to full open position
Source water isolation valves, if provided, closed or restricted
Open valves to full open position
Water regulating valve incorrectly set or defective
Reset or replace
Compressor discharge valve partially closed
Open valve to full open position
Non-condensable gases in hydronic system
Purge non-condensable gases from bleed valve on condenser or at bleed valve of the building condenser
water system
Overcharge of refrigerant
Purge refrigerant from system while in operation until the first sign of bubbles are shown in the sight glass.
Add back refrigerant just until bubbles clear.
Source water temperature high
Check water supply temperature against requirements; if cooling tower is used check spray nozzles on
cooling tower
Improper condenser water circulation
Use an ample sized cleanable strainer in the condenser water circuit; make certain the strainer is clean to
ensure full flow of condenser water (strainer screen must be 60 mesh minimum)
Insufficient water flow through the Source
Check water flow through condenser against design requirements
Fouled Source brazed plate heat exchanger
Clean-in-place heat exchanger as described on page 32
Defective high pressure switch
Replace high pressure switch
Causes and Prevention of Freeze-Up
Possible Cause
Prevention
Improper charging
Charge per data plate information, located on the unit, following the Superheat and Subcooling procedure
described on page 27.
Improper Load water circulation
Use an ample sized cleanable strainer in the chilled water circuit; make certain the strainer is clean to ensure
full flow and velocity of chilled water (strainer screen must be 60 mesh minimum). It may sometimes be
necessary to treat the water to prevent formation of deposits.
Not draining for winter shutdown
When the system is shut down for the winter, remove the drain plugs, and drain the cooler. Blow out
remaining water with air.
Faulty leaving Load water solution temperature sensor
Verify sensor calibration using a calibrated thermometer and replace if defective.
Wrong freeze-up protection temperature setpoint
Verify leaving chilled solution freeze protection temperature setpoint to be set at 8°F above solution freeze point.