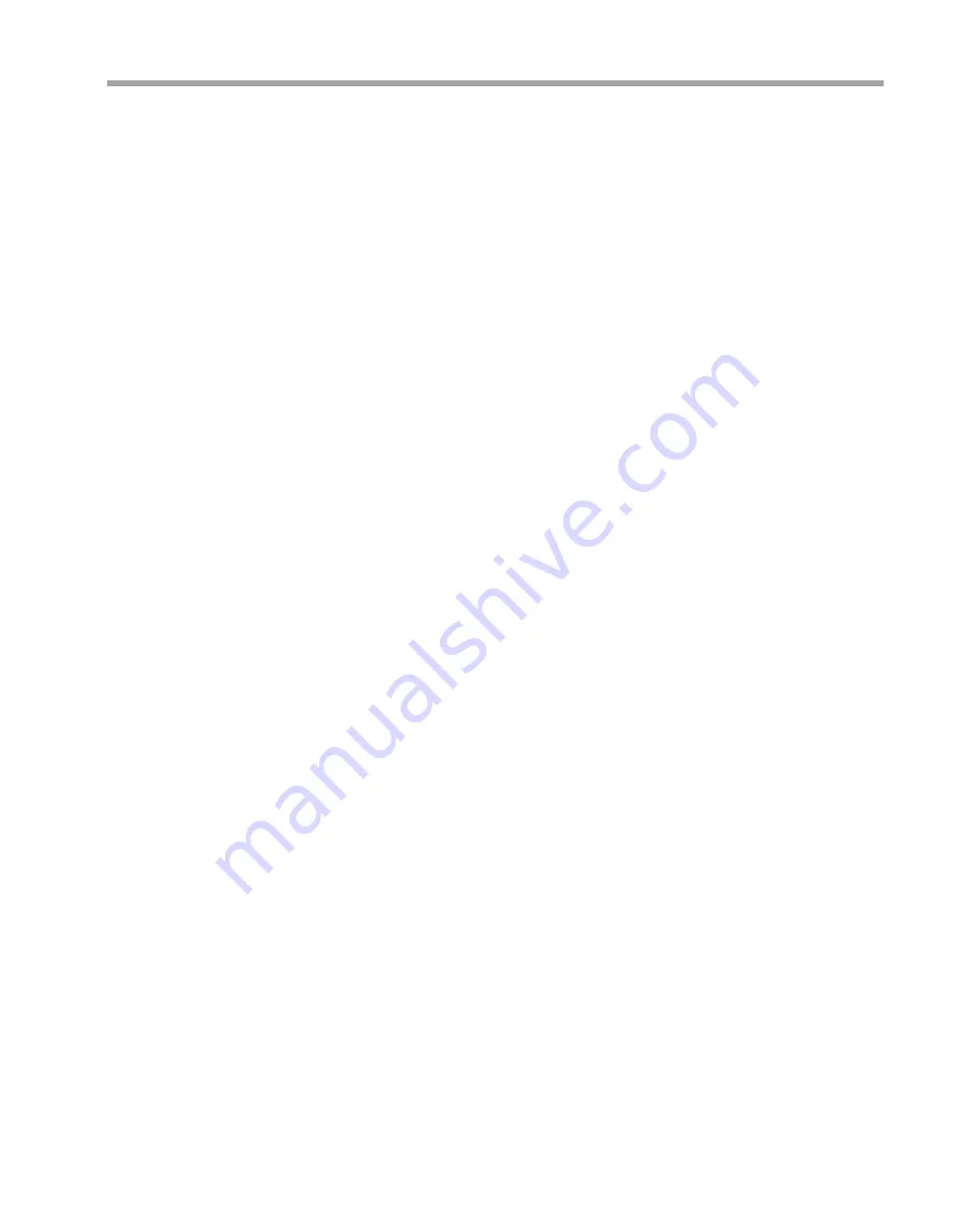
c l i m a t e m a s t e r.c o m
27
Tranquility
®
Large Water-to-Water (TMW) Series
R e v. : O c t o b e r 5 , 2 0 2 1
T H E S M A R T S O L U T I O N F O R E N E R G Y E F F I C I E N C Y
Control System
The Control System provides leaving chilled and hot
water liquid temperature control algorithms which
maintain precise temperature control for heating and
cooling applications. A compressor run time equalization
sequence is given to ensure even distribution of
compressor run time. Unit power consumption is
minimized by indexing the most efficient stages of
cooling, optimizing heat transfer surface.
The controls are two separate boards; the IO FLEX6126
and EX8160 expander board. The controls govern all
significant events, timing, Load and Source water flows
and compressor staging, providing operator interface for
all levels of setting and retrieving data.
The controller directly senses the control parameters
that govern the unit operation, such as Load and Source
entering and leaving temperatures, Load and Source
water flows, both compressors’ winding temperatures,
suction and discharge temperatures and pressures.
Controller Connections and Settings -
Before wiring to,
setting or changing the hardware address, make sure
the controller power is off. The controller only reads the
address when the unit is turned on.
The controller has two rotary switches for assigning the
module’s hardware address. One switch corresponds to
the “tens” digit and the second switch corresponds to
the “ones” digit, allowing for hardware-based addresses
of 02 to 99. For example, if the unit’s address is two, set
the tens switch to zero and the ones switch to two, as
shown in Figure 7. The station ID for each MS/TP node
must be unique on a MS/TP segment. The rotary address
switches are used to set this unique ID.
Set the communication BAUD rate with DIPS 1 and 2,
see figure 7. 9600, 19.2K, 38.4K, or 76.8K available.
Set the protocol with DIPS 5, 7, and 8, see figure 7.
MSTP, N2, and Modbus are available.
Field Component Connections to the Controller -
Field
integration is simplified by the use of the following
minimum input devices:
• A remote OFF, HEAT, COOL input for scheduling is
required for unit operation. (not required if BAS is used)
Connect 3 wires to 7, 9, 10 plus add jumper between
8 and 10.
• Voltage/phase monitor (phase loss/phase reversal,
brown-out/black-out device) is recommended for
unit operation. (If not used, add jumper wire, connect
between 1 and 2 at LVTB2, see wire diagram.)
• BAS or BacView6 (one per site).
• Optional fault reset switch can be connected between
11 and 12 at LVTB2, see wire diagram.