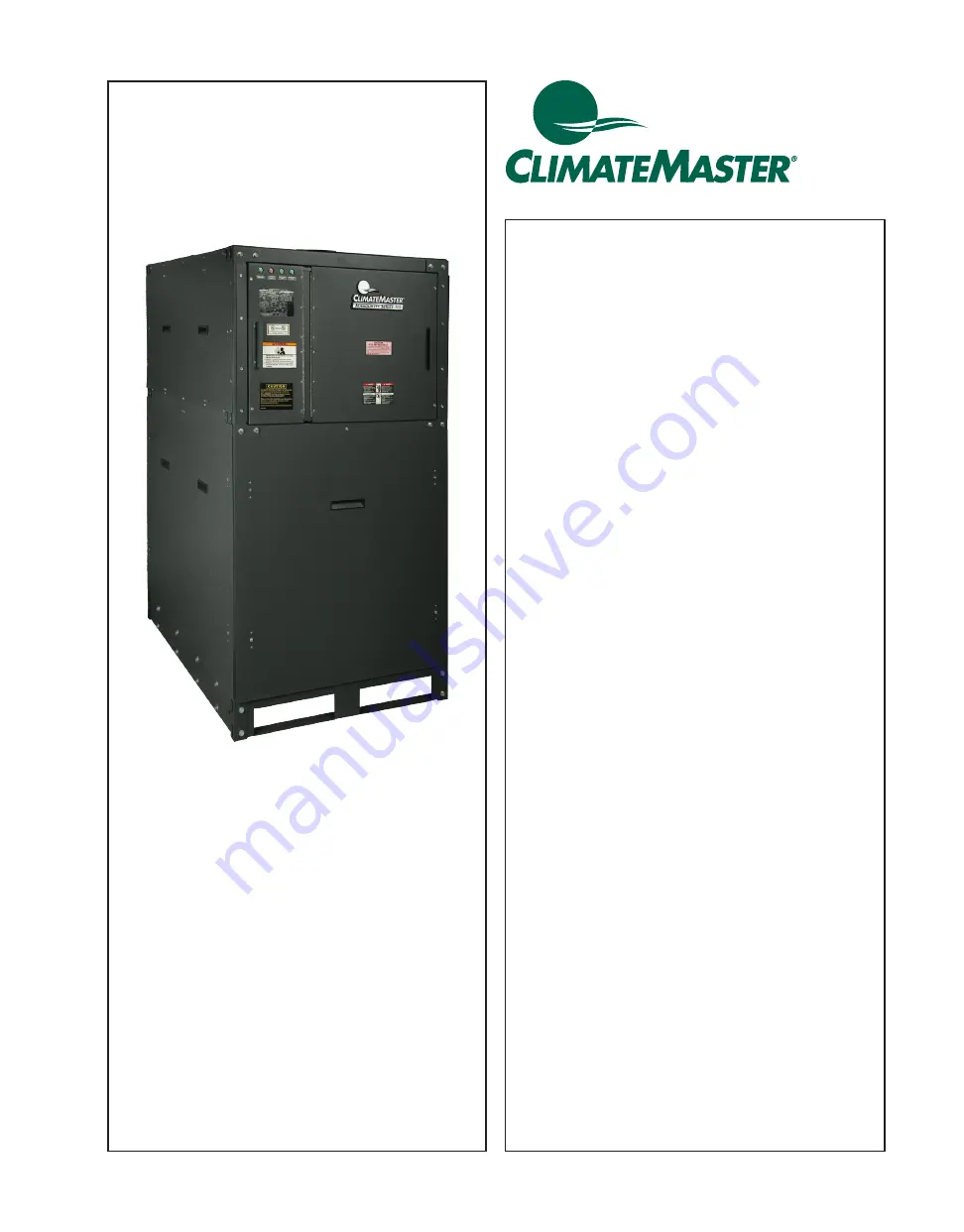
Tranquility
®
Large
Water-to-Water
(TMW) Series
Models 360 - 840
Commercial
EarthPure
®
Water-to-Water
Water-Source
Heat Pumps - 60Hz
Installation, Operation
& Maintenance
97B0090N01
Revised: October 5, 2021
Table of Contents
Model Nomenclature
3
General Information
4
Unit Physical Data
6
Unit Dimensional Data
7
Unit Installation
8
Piping Installation
9
Load Plumbing Installation
10
Water Temperature Requirements
10
Water-Loop Heat Pump Applications
11
Ground-Water Heat Pump Applications
12
Ground-Loop Heat Pump Applications
13
Water Quality Standards
14
Electrical - Line Voltage
18
Wiring Diagram Matrix
21
Typical Wiring Diagram
22
Refrigeration Circuit Diagram
25
Heat Exchangers
26
Control System
27
Control System Optional Features
35
Control Sequence of Operation from BAS
36
BACnet, Modbus, N2 Points List
37
Unit Commissioning & Operating Conditions
43
Piping System Cleaning & Flushing
44
Pre-Start Up Procedures
45
Pre Start-up Check List
47
Unit Start Up Procedures
48
Operation and Maintenance
51
Operational Limitations
53
Compressor Information
54
Refrigeration System Recharging
55
Sequence of Operation
56
Factory Installed Options
57
Field Installed Options
57
Troubleshooting Guide
58
Start Up Form
59
Refrigeration Troubleshooting Form
61
Warranty (US & Canada)
62
Revision History
64