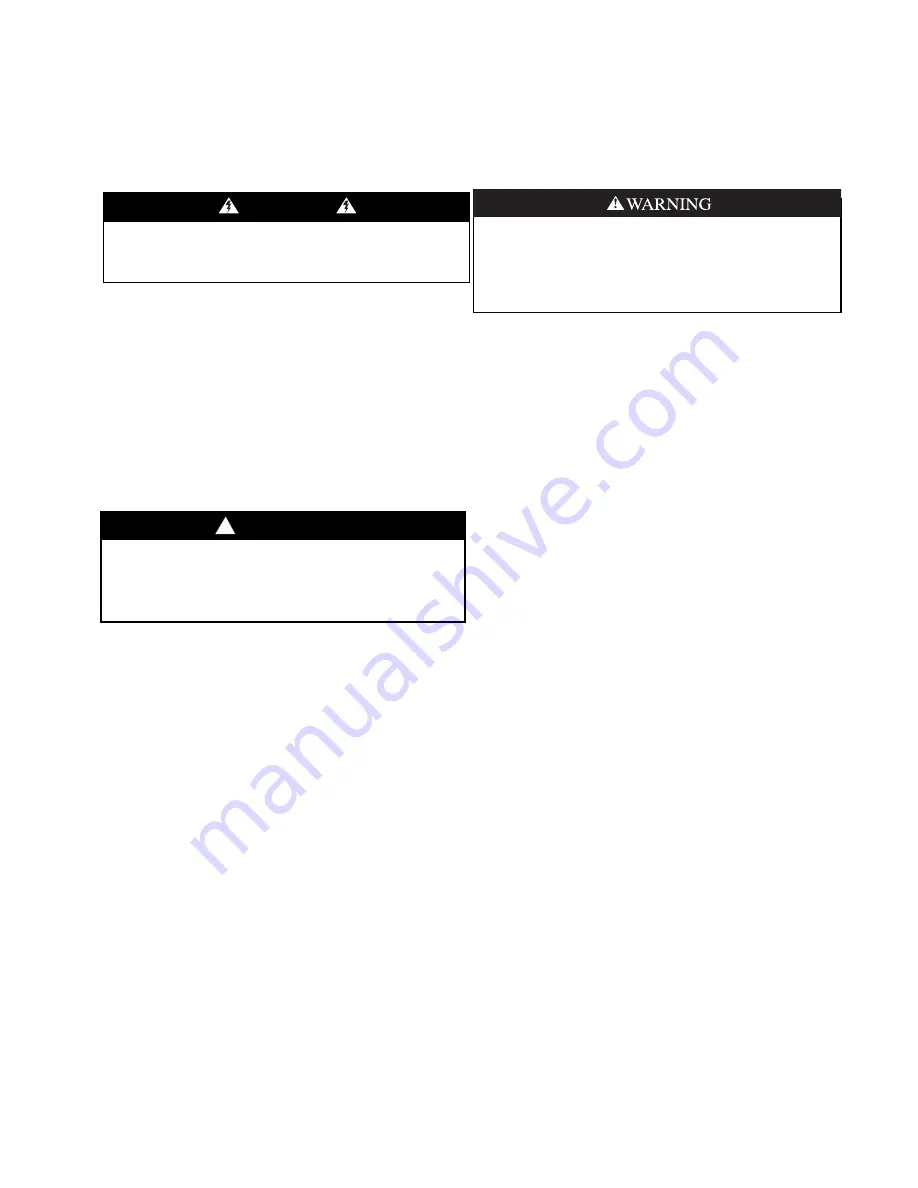
Page 11
MAINTENANCE
Maintenance Procedures
Perform the maintenance procedures outlined below
periodically as indicated:
To prevent injury or death due to electrical shock or
contact with moving parts, open unit disconnect
switch before servicing unit.
FILTERS: Inspect filters. Establish a regular mainte-
nance schedule. Replace/clean filter frequently depend-
ing upon need.
To remove the filter from a Large Commercial Unit, slide
the filter out of its frame located in the return air open-
ing. When re-installing the filter, use the slide-in rails of
the filter frame to guide the filter into the proper position.
Verify that the airflow arrow found on the top of each
filter points toward the unit. Always replace filters with
the same size and quantity of filters as removed from the
unit.
To avoid fouled machinery and extensive unit clean-
up, DO NOT operate units without filters in place.
DO NOT use equipment as a temporary heating or
cooling source during construction.
CONDENSATE PANS: Check condensate drain pans
for algae growth every three (3) months. If algae growth
is apparent, consult a water treatment specialist for
proper chemical treatment. The application of an algae-
cide every three (3) months will typically eliminate algae
problems in most locations.
FAN MOTORS: Lubricate fan motors annually. All
ClimateMaster Large Commercial Units are fully
lubricated at the factory. DO NOT lubricate during
installation. Check all belts and sheaves for wear. Adjust
and replace as needed.
Conduct amperage checks annually. Amperage draw
should not exceed normal full load or rated load amps by
more than 10% of the values noted on the unit nameplate.
Maintain a log of amperage values to detect deterioration
prior to component failure.
UNIT INSPECTION: Visually inspect the unit annu-
ally. Pay special attention to hose assemblies. Repair any
leaks and replace deteriorated hoses immediately.
COMPRESSOR: Conduct amperage checks on the
compressor annually. Amperage draw should not exceed
normal full load or rated load amps by more than 10% of
the values noted on the unit nameplate. Maintain a log of
amperage values to detect deterioration prior to compo-
nent failure.
When replacing the compressor contactor or lockout
relay in a unit with electromechanical controls, use
only ClimateMaster replacement parts. Substitution
of other components may result in an inoperative
safety circuit and may cause a hazardous condition.
HEAT EXCHANGERS: Clean heat exchangers
annually. Inspect heat exchangers regularly and clean
more frequently if the unit is located in a “dirty” environ-
ment.
NOTE: If the unit must be reset more than twice,
check the unit for a dirty filter, abnormal entering
water temperature, inadequate or excessive water
flow and internal malfunction. If the unit continues to
cutout, contact a trained service technician.
Controller and Safety Protection
The microprocessor-based controller monitors and
controls unit operation. The controller provides
compressor sequencing, high and low pressure
monitoring, field selectable water and air coil freeze
protection sensing, condensate overflow sensing, over/
under voltage monitoring, and unit performance sentinel.
The control provides a test mode, short cycle protection,
random start-up, a fault LED, fault memory, and
intelligent fault retry. Note the controls operation below
and refer to the controller AOM provided with each unit
for specific controller features, specifications and
operations.
Interstage Time Delay On two compressor units, a time
delay between stage I and stage 2 can be set with a dip
switch on compressor 2 controller.
Pressure Switches Pressure switches are normally
c
losed during normal operating conditions, and open
upon fault. The high pressure switch opens at 375 PSIG
and automatically closes at 3 00 PSIG. The low pressure
s
witch opens at 10 PSIG and automatically closes at 33
PSIG. The low pressure switch must be open for 30
continuous seconds to cause a fault.
Freeze Protection Thermistors used for freeze
protection, is a NTC (negative temperature coefficient)
type. Freeze protection is set at 30 degrees Fahrenheit for
water systems. If antifreeze is used, the freeze protection
can be set at 10 degrees Fahrenheit by cutting a jumper
on the controller.
WARNING
!
CAUTION