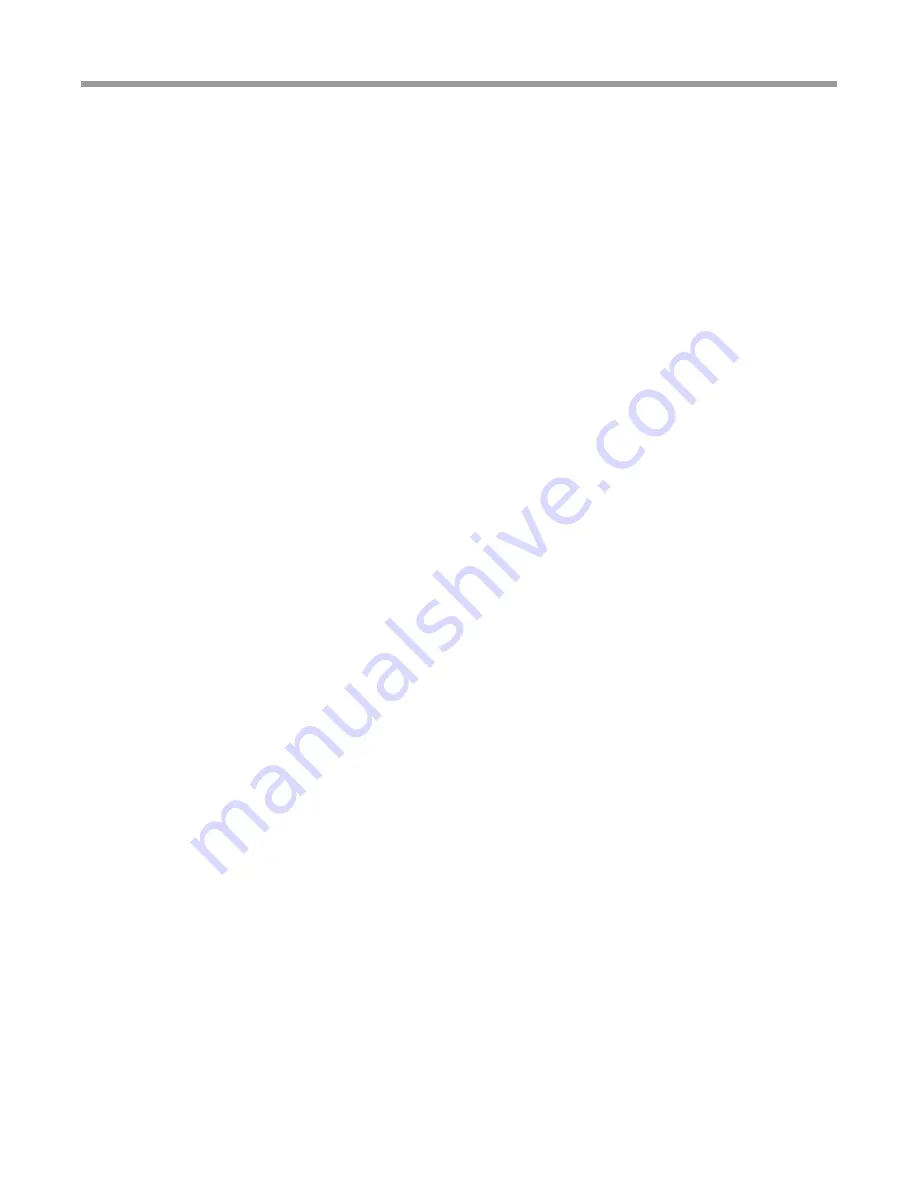
Refrigeration Installation
FP2 Sensor Installation
An FP2 sensor with violet wiring is shipped loose with the
compressor section. This is the air coil low temperature
protection sensor. Install this sensor on the refrigerant line
between the indoor expansion valve and the air coil using
thermal compound and the supplied mounting clips. Ensure
that the sensor makes good thermal contact with the refrigerant
line and insulate the sensor.
Air coil low temperature protection will not be active if this
sensor is installed incorrectly or is not installed.
Add-On Heat Pump Applications
The indoor coil should be located in the supply side of
the furnace to avoid condensation damage to the furnace
heat exchanger for add-on heat pump applications. A high
temperature limit switch should be installed as shown in
Figure 11b just upstream of the coil to de-energize the
compressor any time the furnace is energized to avoid
blowing hot air directly into the coil, elevating refrigerant
pressures during operation. The heat pump will trip out on
high pressure lockout without some method of disengaging
the compressor during furnace operation. Alternatively, some
thermostats with “dual fuel” mode will automatically de-
energize the compressor when second stage (backup) heat
is required.
The TXV should be brazed into place as shown in Figure 10,
keeping the “IN” side toward the compressor section. The
TXV has an internal check valve and must be installed in the
proper direction for operation. Always keep the valve body
cool with a brazing shield and wet rags to prevent damage
to the TXV. Attach the bulb to the suction line using the
supplied hose clamp. Be careful not to overtighten the clamp
and deform the bulb.
NOTICE! The air coil should be thoroughly washed with a
Ä
lming agent, (dishwasher detergent like Cascade) to help
condensate drainage. Apply a 20 to 1 solution of detergent
and water. Spray both sides of coil, repeat and rinse
thoroughly with water.
Evacuation and Charging the Unit
LEAK TESTING - The refrigeration line set must be pressurized
and checked for leaks before evacuating and charging the unit.
To pressurize the line set, attach refrigerant gauges to the service
ports and add an inert gas (nitrogen or dry carbon dioxide) until
pressure reaches 60-90 psig [413-620 kPa]. Never use oxygen or
acetylene to pressure test. Use a halogen leak tester or a good
quality bubble solution to detect leaks on all connections made
in the
Ä
eld. Check the service valve ports and stem for leaks. If
a leak is found, repair it and repeat the above steps. For safety
reasons do not pressurize system above 150 psig [1034 kPa].
System is now ready for evacuation and charging.
Turn service valves full out CCW (see Table 6) and then turn
back in one-half turn to open service ports. Add the required
refrigerant so that the total charge calculated for the unit
and line set is now in the system. Open the service valve
fully counter clockwise so that the stem will backseat and
prevent leakage through the schrader port while it is not in
use. Start unit in the heating mode and measure superheat
and subcooling values after 5 minutes of run time. See
tables 14d for superheat and sub-cooling values. Superheat
is measured using suction temperature and pressure at the
compressor suction line. Subcooling should be measured
using the liquid line temperature immediately outside the
compressor section cabinet and either the liquid line service
valve pressure or the compressor discharge pressure. Note
that different values from tables 14d will be obtained due to
the pressure losses through the condenser heat exchanger.
Adding refrigerant will increase sub-cooling while superheat
should remain fairly constant allowing for a slight amount
of hunting in TXV systems. This increase in subcooling will
require 5 minutes or so of operation before it should be
measured. After values are measured, compare to the chart
and go to “FINAL EVALUATION.”
PARTIAL CHARGE METHOD - Open service valve fully
counterclockwise and then turn back in one-half turn to
open service port. Add vaporized (Gas) into the suction side
of the compressor until the pressure in the system reaches
approximately 100-120 psig. Never add liquid refrigerant into
the suction side of a compressor. Start the unit in heating
and add gas to the suction port at a rate not to exceed
Ä
ve pounds [2.27 kg] per minute. Keep adding refrigerant
until the complete charge has been entered. Superheat is
measured using suction temperature and pressure at the
compressor suction line. Subcooling should be measured
using the liquid line temperature immediately outside the
compressor section cabinet and either the liquid line service
valve pressure or the compressor discharge pressure. Note
that different values from tables 14d will be obtained due to
the pressure losses through the condenser heat exchanger.
Adding refrigerant will increase sub-cooling while superheat
should remain fairly constant allowing for a slight amount
of hunting in TXV systems. This increase in subcooling will
require 5 minutes or so of operation before it should be
measured. After values are measured, compare to the chart
and go to “FINAL EVALUATION.”
FINAL EVALUATION -In a split system, cooling subcooling
values can be misleading depending on the location of the
measurement. Therefore, it is recommended that charging
be monitored in the heating mode. Charge should be
evaluated by monitoring the subcooling in the heating mode.
After initial check of heating sub-cooling, shut off unit and
allow to sit 3-5 minutes until pressures equalize. Restart unit
in the cooling mode and check the cooling superheat against
Tables 14d. If unit runs satisfactorily, charging is complete. If
unit does not perform to speci
Ä
cations the cooling TXV (air
coil side) may need to be readjusted (if possible) until the
cooling superheat values are met.
Checking Superheat and Subcooling
R e s i d e n t i a l S p l i t U n i t s - 6 0 H z P u r o n
®
R e v. : 6 D e c . , 2 0 1 1
22