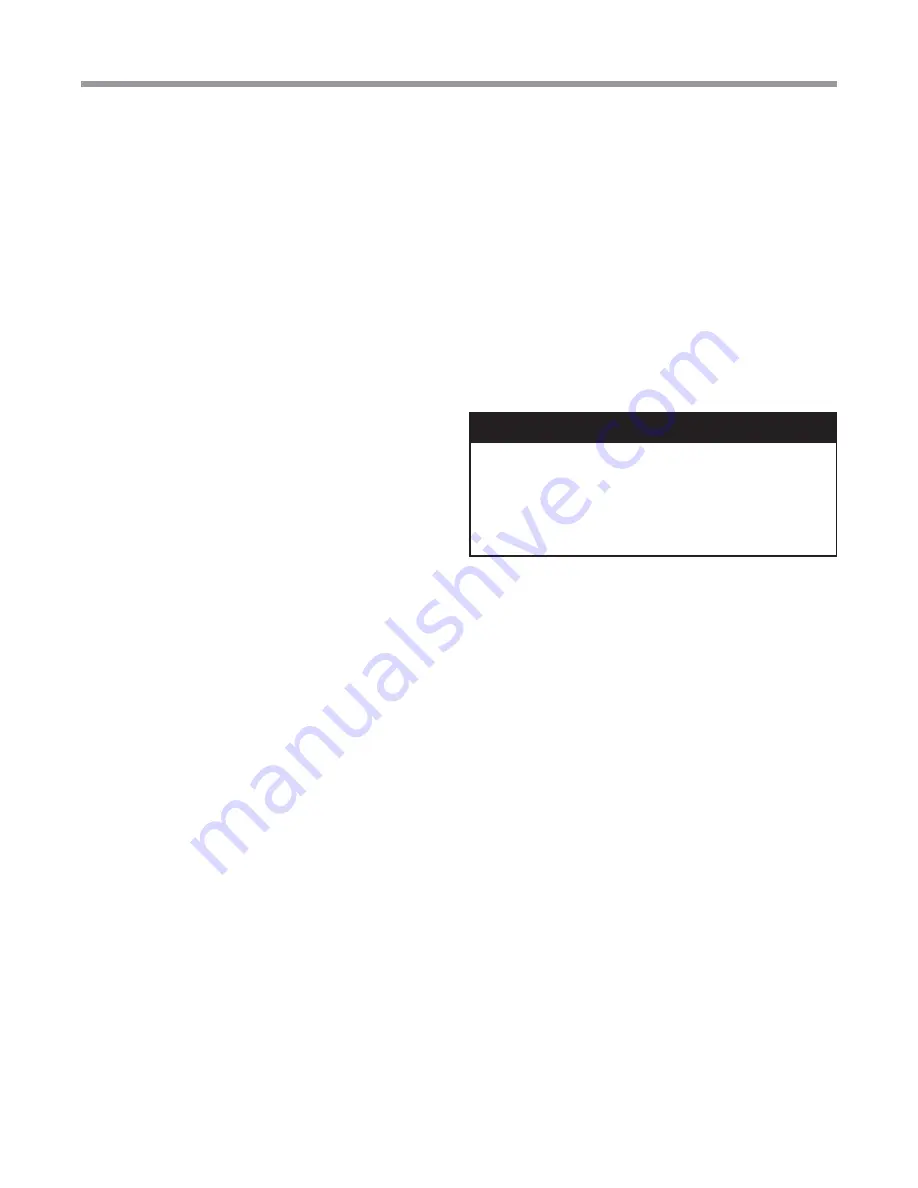
Earth loop temperatures can range between 25 and
110°F [-4 to 43°C]. Flow rates between 2.25 and 3 gpm
per ton [2.41 to 3.23 l/m per kW] of cooling capacity is
recommended in these applications.
Test individual horizontal loop circuits before back
Ä
lling.
Test vertical U-bends and pond loop assemblies prior to
installation. Pressures of at least 100 psi [689 kPa] should be
used when testing. Do not exceed the pipe pressure rating.
Test entire system when all loops are assembled.
Flushing the Earth Loop
Once piping is completed between the unit, Flow Controller
and the ground loop (Figure 7), the loop is ready for
Ä
nal
purging and charging. A
Å
ush cart with at least a 1.5 hp
[1.1 kW] pump is required to achieve enough
Å
uid velocity
in the loop piping system to purge air and dirt particles. An
antifreeze solution is used in most areas to prevent freezing.
All air and debris must be removed from the earth loop
piping before operation. Flush the loop with a high volume
of water at a minimum velocity of 2 fps (0.6 m/s) in all piping.
The steps below must be followed for proper
Å
ushing.
1. Fill loop with water from a garden hose through the
Å
ush
cart before using the
Å
ush cart pump to insure an even
Ä
ll.
2. Once full, the
Å
ushing process can begin. Do not allow
the water level in the
Å
ush cart tank to drop below the
pump inlet line to avoid air being pumped back out to
the earth loop.
3. Try to maintain a
Å
uid level in the tank above the return
tee so that air cannot be continuously mixed back into
the
Å
uid. Surges of 50 psi (345 kPa) can be used to help
purge air pockets by simply shutting off the return valve
going into the
Å
ush cart reservoir. This “dead heads”
the pump to 50 psi (345 kPa). To purge, dead head the
pump until maximum pumping pressure is reached.
Open the return valve and a pressure surge will be sent
through the loop to help purge air pockets from the
piping system.
4. Notice the drop in
Å
uid level in the
Å
ush cart tank when
the return valve is shut off. If air is adequately purged
from the system, the level will drop only 1-2 inches (2.5
- 5 cm) in a 10” (25 cm) diameter PVC
Å
ush tank (about a
half gallon [2.3 liters]), since liquids are incompressible. If
the level drops more than this,
Å
ushing should continue
since air is still being compressed in the loop
Å
uid.
Perform the “dead head” procedure a number of times.
Note: This
Å
uid level drop is your only indication of air in
the loop.
Antifreeze may be added before, during or after the
Å
ushing
procedure. However, depending upon which time is chosen,
antifreeze could be wasted when emptying the
Å
ush cart
tank. See antifreeze section for more details.
Loop static pressure will
Å
uctuate with the seasons.
Pressures will be higher in the winter months than during
the cooling season. This
Å
uctuation is normal and should
be considered when charging the system initially. Run the
unit in either heating or cooling for a number of minutes to
condition the loop to a homogenous temperature. This is
a good time for tool cleanup, piping insulation, etc. Then,
perform
Ä
nal
Å
ush and pressurize the loop to a static
pressure of 50-75 psi [345-517 kPa] (winter) or 35-40 psi
[241-276 kPa] (summer). After pressurization, be sure to
loosen the plug at the end of the Grundfos loop pump
motor(s) to allow trapped air to be discharged and to insure
the motor housing has been
Å
ooded. This is not required
for Taco circulators. Insure that the Flow Controller provides
adequate
Å
ow through the unit by checking pressure drop
across the heat exchanger and compare to the pressure
drop tables at the back of the manual.
Ground-Loop Heat Pump Applications
ѥ
CAUTION!
ѥ
Antifreeze
In areas where minimum entering loop temperatures drop
below 40°F [5°C] or where piping will be routed through
areas subject to freezing, antifreeze is required. Alcohols
and glycols are commonly used as antifreeze; however your
local sales manager should be consulted for the antifreeze
best suited to your area. Low temperature protection
should be maintained to 15°F [9°C] below the lowest
expected entering loop temperature. For example, if 30°F
[-1°C] is the minimum expected entering loop temperature,
the leaving loop temperature would be 25 to 22°F [-4 to
-6°C] and low temperature protection should be at 15°F
[-10°C]. Calculation is as follows:
30°F - 15°F = 15°F [-1°C - 9°C = -10°C].
All alcohols should be premixed and pumped from a
reservoir outside of the building when possible or introduced
under the water level to prevent fumes. Calculate the
total volume of
Å
uid in the piping system. Then use the
percentage by volume shown in Table 3 for the amount
of antifreeze needed. Antifreeze concentration should be
checked from a well mixed sample using a hydrometer to
measure speci
Ä
c gravity.
Low Water Temperature Cutout Setting
- CXM Control
When antifreeze is selected, the FP1 jumper (JW3) should
be clipped to select the low temperature (antifreeze 10°F
[-12.2°C]) set point and avoid nuisance faults (see “Low
Water Temperature Cutout Selection” in this manual). Note:
Low water temperature operation requires extended range
equipment.
13
R e s i d e n t i a l S p l i t U n i t s - 6 0 H z P u r o n
®
R e v. : 6 D e c . , 2 0 1 1
CAUTION!
To avoid equipment damage, DO NOT allow
system water pressure to exceed 100 psi when using
the GT-PE Outdoor Compressor Section. The expansion
tank in the GT-PE has a maximum working water
pressure of 100 psi. Any pressure in excess of 100 psi
may damage the expansion tank.