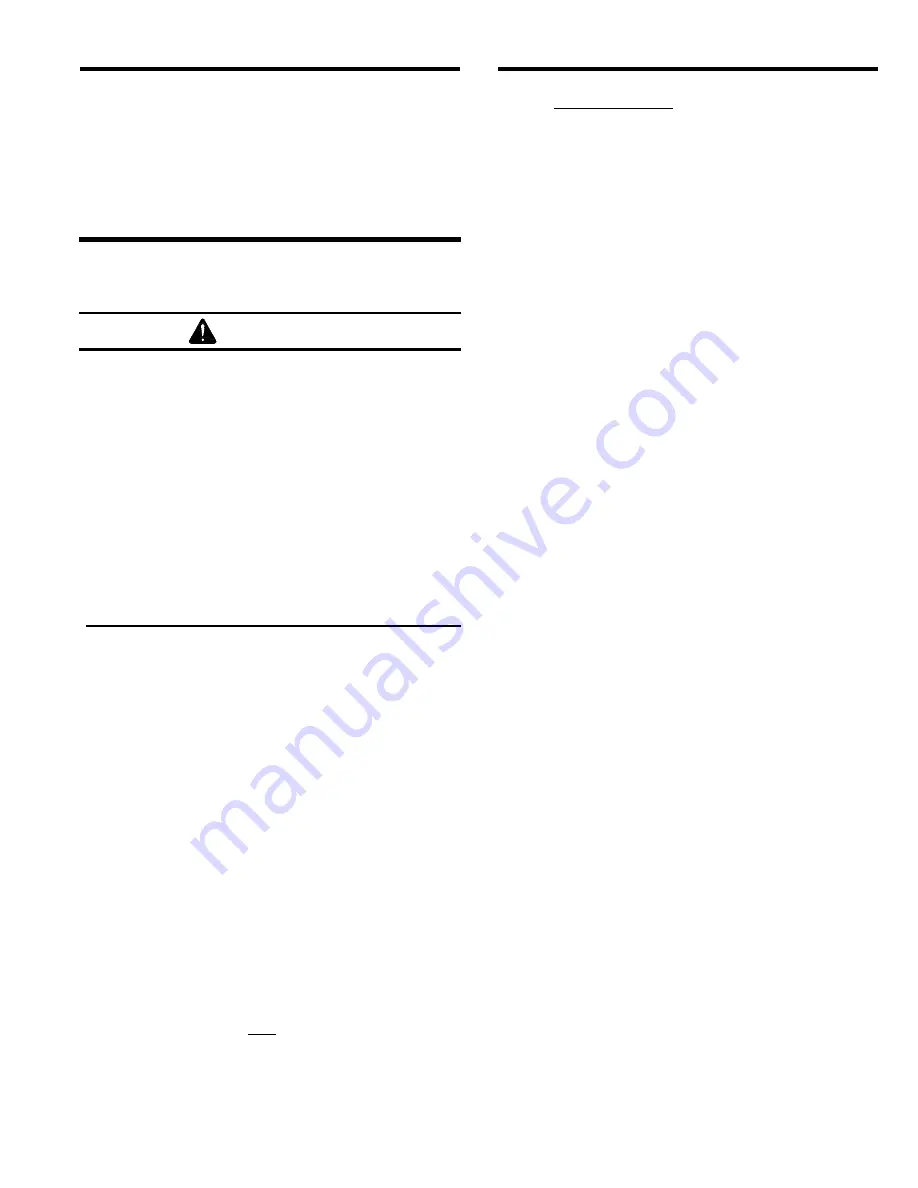
PULSAR
®
IX SUCTION BLAST CABINET
Page 29
© 2019 CLEMCO INDUSTRIES CORP.
www.clemcoindustries.com
Manual No. 23425, Rev. C, 07/19
damaged, clean old gasket material from the flange and
install new 2" strip gasket.
7.12.9
Reattach the reclaimer to the cone and stand.
7.12.10
If the baffle was replaced, allow the caulking to
cure before putting the reclaimer into service.
8.0
TROUBLESHOOTING
WARNING
To avoid serious injury, observe the following
when troubleshooting.
Turn OFF the compressed-air supply, bleed
the supply line, and lockout and tagout the
air supply.
If checking the controls requires air, always
enlist the aid of another person to:
Hold the nozzle holder securely.
Operate the foot pedal.
Never bypass the foot pedal or wedge it in
the operating position.
Never bypass the door interlock system.
Follow all OSHA regulations, including
lockout and tagout procedures
.
8.1
Poor visibility
8.1.1
Dirty filter cartridges. Empty the dust containers.
Run the exhauster and pulse cycle for several minutes.
Adjust pulse pressure and/or pulse sequence, per
Sections 5.7 and 5.8. When pulse pressure and pulse
duration are at maximum, replace cartridges.
8.1.2
Exhauster motor not operating. Check voltage to
motor and motor wiring.
8.1.3
Check rotation of exhauster motor; the motor
should rotate as indicated by the arrow on the housing. If
it does not rotate in the proper direction,
lockout and
tagout electrical power
and switch motor leads, as
shown on the motor plate. See Section 2.5.
8.1.4
Using friable media that rapidly breaks down, or
using media that is too fine or worn out can cause poor
visibility.
8.1.5
Dust-collector outlet damper closed too far
restricting air movement through the cabinet. Adjust
static pressure, per Section 5.4.
8.1.6
Cabinet air-inlet damper closed too far
restricting air movement into the cabinet. Adjust damper,
per Sections 2.9 and 5.9.
8.1.7
Reclaimer door open.
8.1.8
Hole worn in flex hose between cabinet hopper
and reclaimer inlet, or reclaimer outlet and dust-collector
inlet. Replace hose and route it with as few bends as
possible to prevent wear.
8.1.9
Obstruction in flex hose between the cabinet
hopper and reclaimer inlet. Inspect hoses for wear.
8.1.10
Paddle wheel worn. Check exhauster’s wheel
for wear.
8.2
Abnormally high media consumption
8.2.1
Door on reclaimer is open or door gasket is
worn. Air entering the reclaimer around the door will
cause media carry over to the dust collector. Inspect
door gasket. DO NOT operate unless all doors are
closed.
8.2.2
Dust-collector outlet damper open too far. Adjust
static pressure, per Section 5.4.
8.2.3
Media may be too fine or worn-out. Check
condition of media.
8.2.4
Using friable media that rapidly breaks down.
Check condition of media.
8.2.5
Blast pressure too high for the media, causing
media to rapidly break down. Check blast pressure and
adjust as needed or change media.
8.2.6
Hole worn in reclaimer or leak in reclaimer
seams. Check entire reclaimer for negative-pressure
leaks.
8.2.7
Externally adjustable vortex needs adjustment,
refer to Section 5.5.
8.2.8
When using media finer than 180-mesh, the inlet
baffle of the reclaimer (600 and 900 cfm only) may need
to be removed. Refer to Section 7.12.
8.3
Reduction in blast cleaning rate
8.3.1
Low media level reducing media flow. Check
media level in reclaimer; add media or replace media as
needed, per Section 4.2.