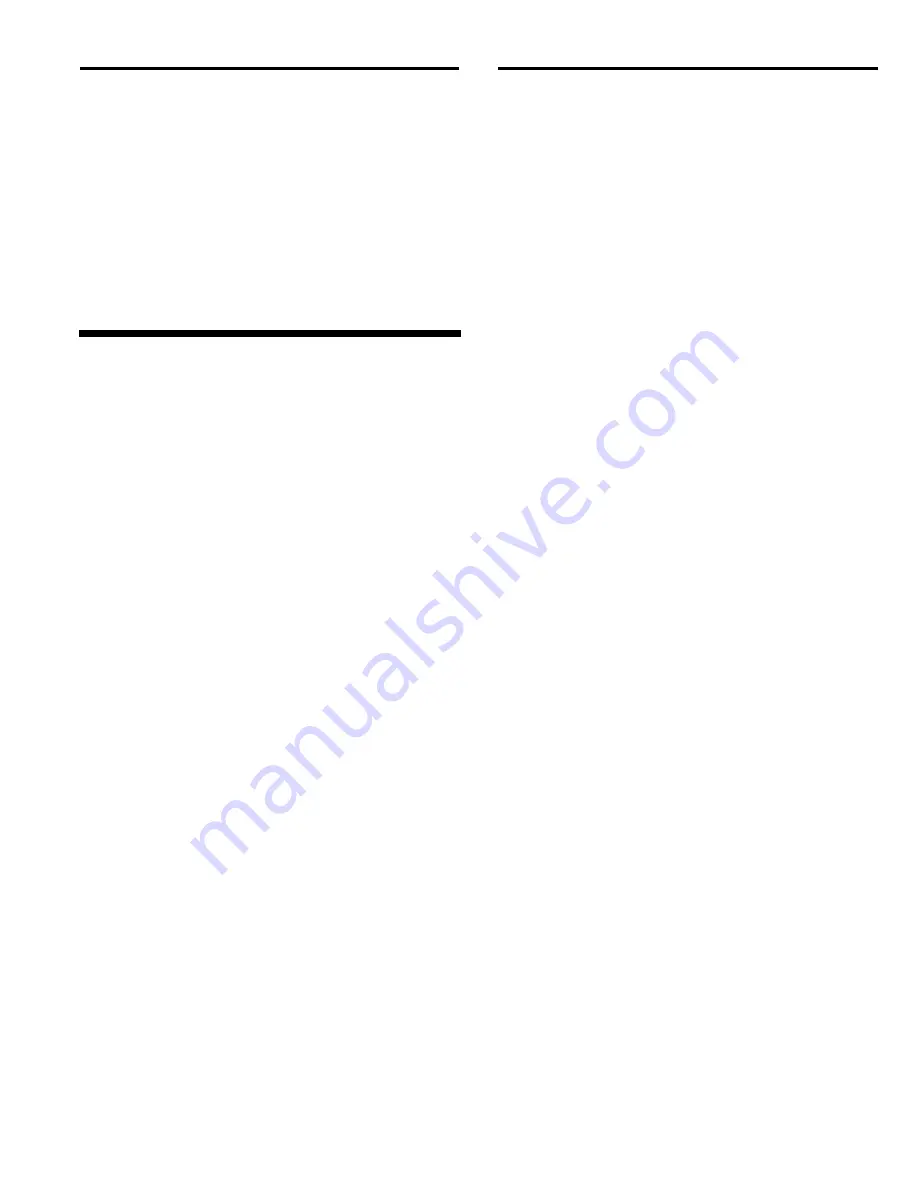
FLAT-TRAK
®
RECOVERY FLOOR
Page 3
© 2017 CLEMCO INDUSTRIES CORP.
www.clemcoindustries.com
Manual No. 07763, Rev M
1.4 Tools
Requirement
Open/box end wrenches, 7/16" - 3/4"
Socket wrench w/ 7/16" - 3/4" sockets
Screw
drivers
Hex
keys
Hand drill with bit assortment
Hammer
Drift
pin
Welder
Measuring tape, long enough to measure the
floor area diagonally
Chalk
line
2.0 INSTALLATION
2.1 Installation
Notes
2.1.1
These instructions are general guidelines for all
sizes of Flat-Trak
®
floors. The assembly illustrations shown
throughout the manual are for a typical arrangement.
Layout drawings for specific jobs are provided with the job
manual. All floor drive sections are 98-1/2-inches long. If
floor extensions are used, they will be 30-inches, 60-
inches, or 120-inches long. All cross conveyor base
segments are 9-feet long, with a 40-13/16-inch long drive
section. If cross conveyor extensions are used, they will be
24-inches, 36-inches, and/or 72-inches long.
2.1.2
When both short and long conveyor extensions
are used, the shorter extensions should be located
between two longer extensions. See the example shown in
Figure 1. The 30-inch and 60-inch extensions are placed
between the longer drive section and 120-inch extension.
2.1.3
Extensions can be placed in any order; however,
the same sequence must be used on all floor sections.
See Note 1 in Figure 1.
2.1.4
Conveyor section widths are measured from
center to center. Since the beams are 3-inches wide, an
additional 1-1/2 inches is needed on each side of the floor
layout. For example: If a floor is four sections wide, the
total outside dimension of the floor width will be 147 inches
(four 36-inch sections plus 3 inches [1-1/2 inches on each
side]). Be sure to allow for the extra 1-1/2 Inches when
laying out the floor perimeter.
2.1.5
If
the
Flat-Trak
®
Floor is recessed in a pit or in an
existing room, it is necessary to have 3 inches between
the outside perimeters of the floor and pit or room wall.
The 3-inch space is needed to replace rollers.
2.1.6
Track beams are labeled "This side up" and "This
end toward drive cylinder". When laying out the tracks,
make sure the side labeled "up" is facing up, and the end
marked toward drive cylinder, is facing the drive cylinder.
Splice holes in the beams are positioned so they are on
the lower side when the tracks are right side up. If the
splice holes of two adjoining tracks do not lineup one of
the tracks may be upside down.
2.1.7
The
Flat-Trak
®
floor is installed on a single level. If
the Flat-Trak
®
replaces an existing multi-level floor, a
single level floor capable of sustaining the gross weight of
the recovery floor, abrasive, grate, parts to be blasted, and
operator, will have to be constructed.
2.1.8
The electro/pneumatic cylinder control panel(s)
must be accessible to an air supply line and electrical
source, and located to enable installation of poly tubing air
lines to run from the panel to each air cylinder. One
cylinder is used on each floor conveyor section, and cross
conveyor section. The panel must be located within a
distance to require no more than 15 feet of tubing to the
cross conveyor cylinder. See note # 2 and the typical
arrangement in Figure 1.
2.1.9
Cylinder timing control panels come with four, five,
or six stations. One station operates one conveyor section
(one cylinder for each section). If the system has more
than six conveyor sections, more than one panel is
required. For example, if the floor has nine conveyor
sections, a four-station and five-station panel is used. If the
floor has seven-sections, two four-station panels are used.
The unused station(s) must be looped with a short piece of
5/16 inch poly tubing, and the flow control valve (used to
time the cylinder cycles) must be closed.
2.1.10
Control panels do not need to be mounted
together. It is best to separate the panels on large
systems, and mount each one as close as possible to the
cylinders they control. See Paragraph 2.1.8.
2.1.11
The
Flat-Trak
®
is designed to connect to a Clemco
elevator, and recovery components. If other brand
recovery components are used, transitions must be made
to adapt to them.
2.2 Uncrating
2.2.1
Uncrate and identify all parts. Use the checklist
shipped with the equipment, and the illustrations in Figures
2, 3, 4, and 5 to identify the parts. To help keep the
assembly area organized, and to avoid loss, leave small
parts in marked boxes until they are required.
2.2.2
Sort all parts into groups. The first parts to be
used will be the track beams. Identify and sort them as
shown in Figure 2.
2.2.3
Identify and sort hardware shown in Figure 3,
carriages shown in Figure 4, and cylinder equipment
shown in Figure 5. Make sure the carriages are flat.
Straighten any that may have bent during shipment. It is
important that the carriage frames lay flat on the floor.