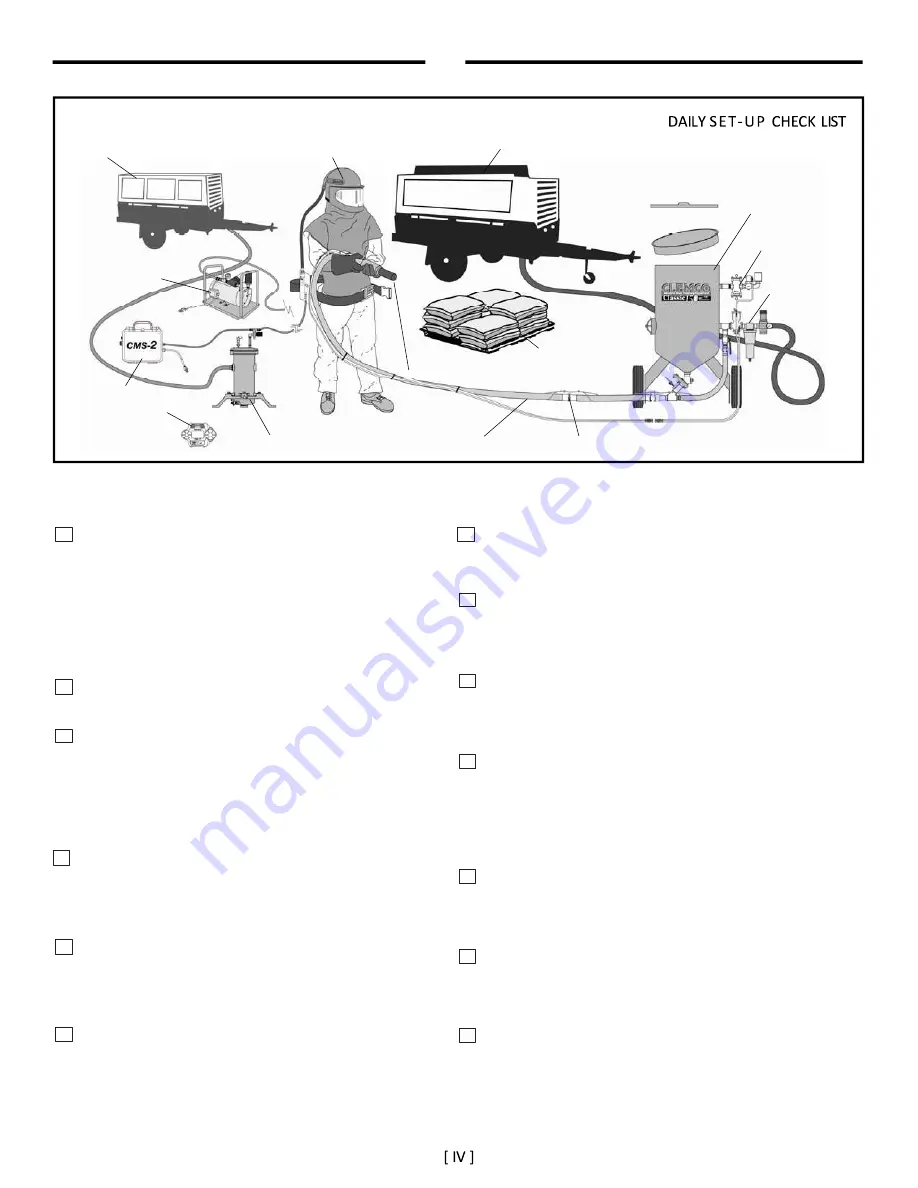
PREFACE
Make sure all blast operators are properly trained and suitably attired with a blast suit, safety boots, leather gloves, respiratory and hearing protection. Every day before start up,
check all equipment components, including piping, fittings, and hoses, and valves, for leaks, tightness, and wear. Repair or replace as needed. Use the following checklist.
1. PROPERLY-MAINTAINED AIR COMPRESSOR
sized to provide
sufficient volume (cfm) at given pressure for nozzle and other tools. ADD 50%
volume (cfm) reserve to allow for nozzle wear. Use large compressor outlet and
air hose (at least 4 times the nozzle orifice diameter). For oil-lubricated
compressors, the employer shall use a high- temperature or carbon monoxide
alarm, or both, to monitor carbon monoxide levels. If only high-temperature
alarms are used, the air supply shall be monitored at intervals sufficient to
prevent carbon monoxide in the breathing air from exceeding 10 ppm. Follow
the manufacturer’s checklist and maintenance instructions.
2. BREATHING-AIR COMPRESSOR
(or oil-less ambient air pump)
capable of providing Grade D quality air, located in a dust free area. Read # 1
above.
3. CLEAN, PROPERLY-MAINTAINED NIOSH-APPROVED SUPPLIED-AIR
RESPIRATOR
worn by blast operators, and other workers exposed to blast dust.
Make sure all respirator components are in place — all lenses, inner collar, and
cape. Thoroughly inspect all components for wear. The NIOSH approval (approval
number is listed in the owner’s manual) is for a complete assembly from point of
attachment on the CPF (sorbent bed) filter to the complete respirator. Substitution of
any part voids the NIOSH approval.
4. CARBON MONOXIDE MONITOR/ALARM
installed at the CPF filter or
inside the supplied-air respirator for monitoring for the presence of deadly CO gas
and warning the operator(s) when the CO level reaches an unacceptable level.
When an ambient air pump is used for breathing air, a CO monitor provides a
measure of safety. Read # 1 above.
5. BREATHING-AIR FILTER (OSHA-REQUIRED
sorbent bed filter) for
removal of moisture and particulate matter in the compressed air breathing-air
supply. Monitor the condition of the cartridge and replace when odor is detected or
at 3 month intervals, whichever comes sooner. The breathing air filter does NOT
detect or remove carbon monoxide (CO). Always install a CO monitor/alarm.
6. BLAST MACHINE
(bearing U or UM stamp, National Board Number, and
Maximum Working Pressure) sized to hold a 30-minute abrasive supply. Examine
pop-up valve for alignment. Check piping, fittings, screens, valves for tightness,
leaks, and wear. Always ground the machine to eliminate hazard of static shock.
Install a blast machine screen to keep out foreign objects. Use a blast machine
cover if left outdoors overnight. Never exceed the maximum working pressure of the
vessel.
7. AIR LINE FILTER
(moisture separator) installed as close as possible to the
blast machine inlet and sized to match the size of the inlet piping or larger air supply
line. Clean filter and drain often. Damp abrasive causes operational problems.
8. REMOTE CONTROLS
are required by OSHA and must be in perfect
operating condition. Test and check all components to ensure all parts are present
and fully functional. Use genuine replacement parts. NEVER mix parts from different
manufacturers. Never use welding hose for remote control hose.
9. BLAST HOSE
should have an inside diameter sized to suit the blast nozzle.
The ID should be three to four times the size of the nozzle orifice diameter. Blast hose
should be arranged in as straight a line as possible from the blast machine to the
work area, avoiding sharp bends.
10. COUPLINGS AND NOZZLE HOLDERS
should fit snugly on the hose and
be installed with manufacturer recommended screws. Coupling lugs must snap firmly
into locking position. Gasket must always be used to form a positive seal, and cotter
pins must be installed. Replace gasket when wear, softness or distortion is detected.
Check nozzle holder for thread wear; replace at any sign of wear. Install safety cables
at all connections.
11. NOZZLE
orifice size should be checked and nozzle replaced when worn
1/16” from original size. (No. 5 nozzle has 5/16” orifice diameter; replace when it
measures 3/8”). Threads should be inspected daily for wear and nozzle should be
replaced when wear is detected. Always use a nozzle washer.
12. ABRASIVE
must be a material specifically manufactured for blasting. It
should be properly sized for the job. Check material safety data sheet for free-
silica, cyanide, arsenic, lead and other toxins and avoid use when these toxic,
harmful substances are present.
SURFACE TO BE BLASTED
should be examined for hazardous substances.
Take appropriate protective measures as required by OSHA to ensure the blast
operator, other workers in the vicinity, and any bystanders are properly protected.
©Clemco Industries Corp., Stock No. 20954P, 0692 Rev. F, 06/12
1. Air Compressor
7. Air Line
Moisture
Separator
5. CPF Air Filter
6. ASME Code
Blast Machine
8. Remote
Controls
9. Blast Hose
10. Hose Couplings and Safety Cables
11. Appropriately Sized Nozzle
12. Abrasive
4. External or
Helmet Mounted
Carbon Monoxide
Monitor /Alarm
2. Breathing Air Compressor for
High Pressure Respirators
3. NIOSH Approved
Supplied-Air Respirator
or Ambient Air Pump for
Low Pressure Respirators