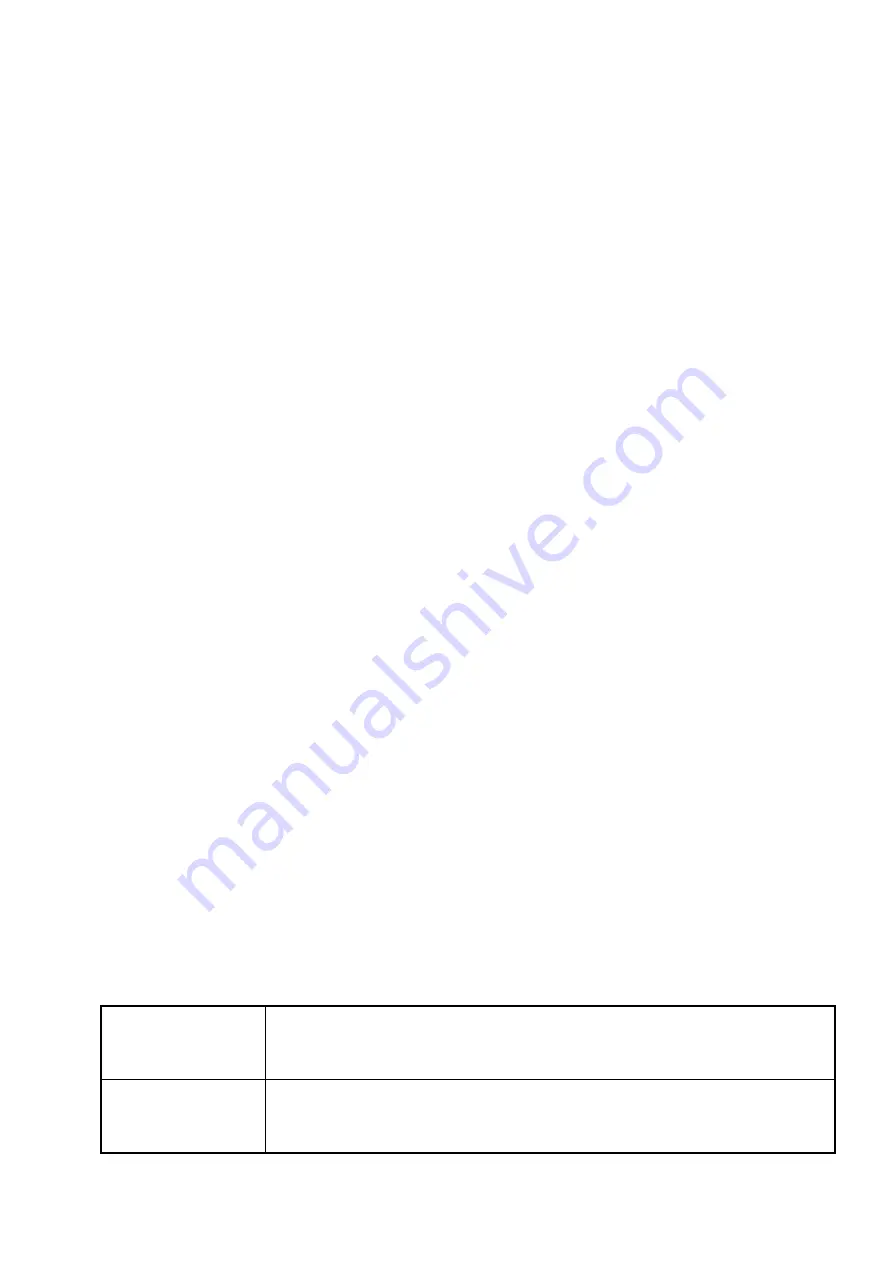
7
2.3 Toxic dust poisoning
The following applies for model 1 and model 2 protective clothing in accordance with DIN EN ISO
14877:2003 (D):
Research has identified the potential risks of lead poisoning to unprotected operators and other
personnel who may be exposed to lead-containing abrasive dust in the vicinity of abrasive blasting
operations. This dust is primarily the result of removing lead-containing paints. A risk to human life and
health may also result from paints containing heavy metals, asbestos or other toxic dust. Lead
poisoning may cause death. The maximum workplace concentration has been defined as 0.1 mg/m³ of
air (TRGS 900).
For this reason, the blasting contractor must always determine which type of paint is to be removed
and, if necessary, ensure that operators wear a blast hood or helmet that is approved for use with
these substances or an additional respirator.
In accordance with DGUV Regulation 112-190, Class 4B blast protection equipment can be used at up
to 500 times the threshold value.
2.4 Ear protectors
Ear protectors must be worn when using the blast helmet.
2.5 Expiry date of the PPE or certain of its components
The equipment must be properly serviced, maintained and stored. All rubber components must be
replaced at the latest 5 years after the date of manufacture. It is recommended that the blast helmet is
replaced after a maximum of 10 years.
3 Description of the equipment
The minimal version of the blast helmet consists of the following components:
Helmet with chin strap, suspension and cape
Breathing air line (length approx. 700 mm)
Air supply line (length 10 m) with quick coupling (female)
Air control valve
4 Preparation
Check and/or prepare the following components:
(1) Adjust the helmet
suspension.
Remove the cape (see 8.4).
Detach and adjust the helmet suspension (see 7.2).
(2) Check that the lens
system is in place.
Inner lens (replacement, see 8.1)
Outer lens (replacement, see 8.2)