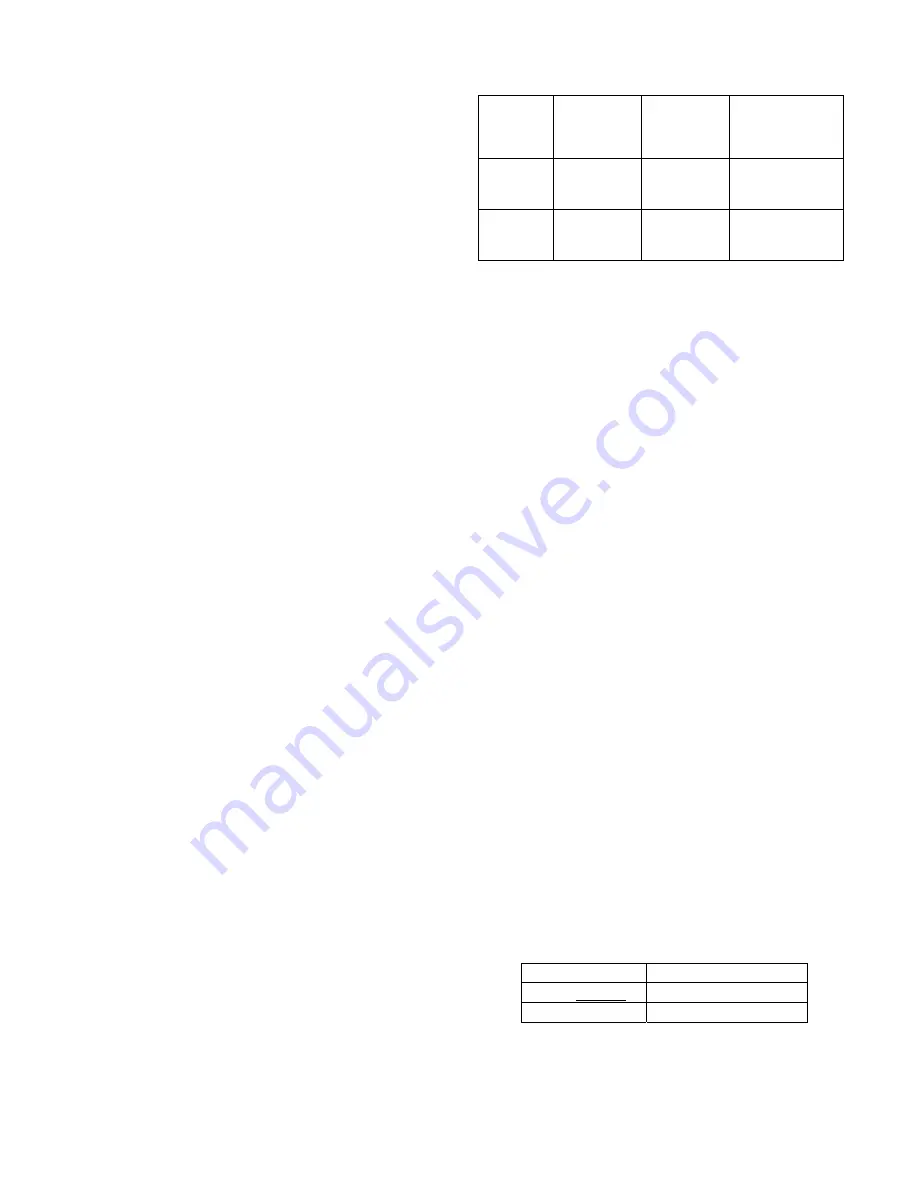
Page 13 of 41
wiring diagram sticker located on the inside
door of the engine gauge panel for proper
connection of the water solenoid.
11)
Fill batteries with electrolyte per battery
manufacturer’s instructions. Connect cables
between engine and batteries only after
electrolyte is installed. Refer to the wiring
diagram inside the engine gauge panel door
(if supplied), or appropriate wiring diagram
(see Page 5), for correct positive and
negative connections.
12)
Connect negative cables directly to the
ground stud. Connect each positive cable to
the large outer post of the manual starting
contactors.
13)
Note: Clarke Operation and Maintenance
Instructions Manual and Clarke parts
illustration pages are located inside the
engine gauge panel.
14)
IMPORTANT! In order to obtain prompt
Warranty Service and to comply with
Emissions regulations, this engine
must
be
registered to the final installation name and
address. To register this engine, go to
www.clarkefire.com
and select Warranty
Registration.
2.4
SPECIFIC FLYWHEEL COUPLING
ALIGNMENT INSTRUCTIONS
2.4.1
Listed Driveshafts
Refer to Listed Driveshaft Installation, Operation and
Maintenance Manual C132355
2.4.2
Driveshaft
To check the alignment of the pump shaft and engine
crankshaft centerlines for proper Parallel Offset and
Angular tolerance, the driveshaft must be installed
between the flywheel drive disc and the flanged hub
on the pump shaft.
Before removing the driveshaft guard, disconnect the
negative battery cable from both batteries.
Before beginning the alignment checks and making
any necessary corrections, install the driveshaft and
re-torque all driveshaft connection bolts to the values
given in the following table:
MODELS
DRIVE
SHAFT
BOLT
SIZE
/MATERIA
L GRADE
TIGHTENING
TORQUE
ft-lbs
(N-m)
ZE4H
CDS20-S1
1/2-20
Grade 8 (Hi-
Tensile)
75-82
(102-112)
ZF6H
SC81A
or
CDS50-SC
7/16-20
,
Grade 8 (Hi-
Tensile)
50-55
(68-75)
(See Note #2)
Note 1 – It is recommended that a medium strength
threadlocker (Loctite 243–blue) be used in the
assembly and torquing of all hardware. This may be
purchased as part number C126758, 50ml bottle.
Note 2 – 4 of the hi-tensile bolts and/or nuts, that are
used to connect the driveshaft to the drive disc and
that connect the driveshaft to the pump companion
flange, will require a “crow’s foot” wrench attached
to a standard torque wrench in order to apply the
required tightening torque. A standard socket will
not work due to close proximity of the bolts and/or
nuts with the driveshaft yoke. The tightening torque
values listed for these bolts and/or nuts have been
corrected for using a “crow’s foot” adapter which
extends the standard torque wrench’s length.
Note 3 – For the high torque required for these nuts it
is recommended that a boxed end crows foot be used.
The following steps describe the proper way to check
alignment. A small pocket scale or ruler with
millimeter markings is recommended to make all
measurements.
A)
To check the Horizontal Parallel Offset, the
driveshaft must be in the proper orientation.
1.
Rotate the shaft so the reference “AB” on the
flywheel adapter disc or the circumference of
the drive shaft flange (against the flywheel
adapter disc) is in the 12 o’clock position
shown on
figure #7a
.
2.
Measure from the face of the flywheel
adapter disc to point E. (Point E is on the
bearing bore as shown in
Figure #7a
). This
measurement must be:
Measurement
Driveshaft
68 ± 1.5 mm
CDS20-S1
109 ± 2 mm
SC81A / CDS50-SC