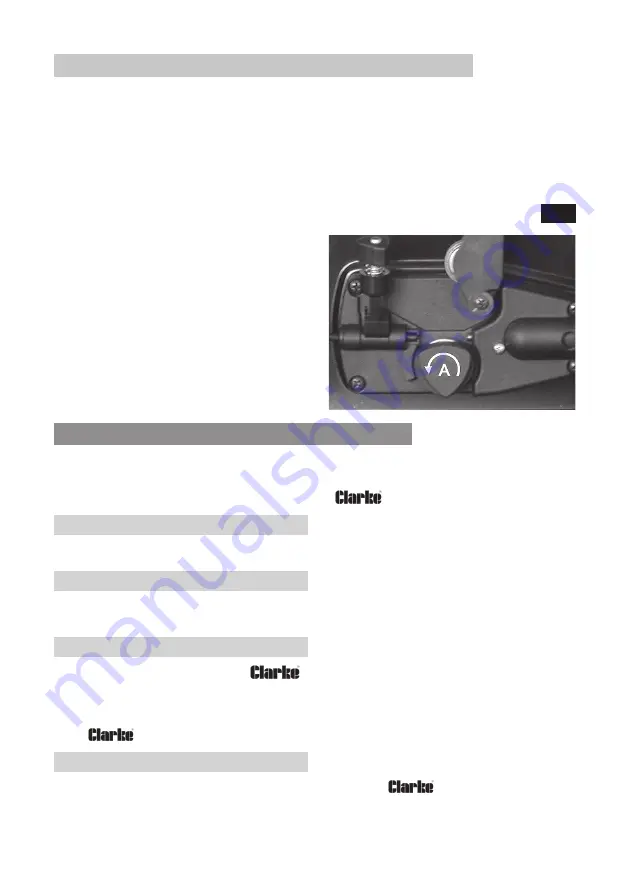
18
(3) Selecting the Correct Drive Roller Groove
As previously mentioned, it is important that the correct groove in the drive roller is
selected for the particular wire being used. Two grooves, 7mm and 9mm are
provided.
The 7mm groove should be used with 6mm dia. wire and the 9mm groove for all
8mm wire and 9mm flux cored wire. The welder s factory set with the 9mm groove
in position.
To change to the other groove, proceed as follows:
Fig.7
1.
With the pressure roller bracket
raised, and the old wire removed, as
shown, turn the roller securing knob
(A), fully anticlockwise, as indicated
in Fig.7, and pull it from the shaft,
followed by the roller.
Turn the roller through 180
O
, replace
it on the shaft, followed by the
securing knob, which should then
be turned fully clockwise to lock the
roller securely in place.
D. CONVERTING TO GAS WELDING
For welding stainless steel or aluminium, it is necessary to convert your NO-GAS
machine to GAS operation. This is a simple process once you have purchased the
following parts, readily available from your
dealer.
1. Welding Wire
Either Mini or 5kg wire spools, at 0.6mm or 0.8mm diameter. (See Accesssories)
2. Contact Tips
The appropriate tip must be used to suit the thickness of wire being used. i.e.,
8mm wire requires a 0.8mm tip and 0.9mm wire requires a 1.0mm tip.
3. Gas Regulator
This is available from your
dealer.
NOTE: Decide in advance whether you are going to use disposable or
rechargable gas bottles as this will effect the type of regulator purchased. Consult
your
dealer
4. Gas
Disposable gas bottles are available from your
dealer, or
rechargeable bottles from your welding supply shop.
SEE ALSO THE NOTES ON PAGE 21 - ATTACH THE EARTH LEAD
Summary of Contents for weld MIG 100EN
Page 29: ...WIRING DIAGRAMS MIG 90EN 29...
Page 30: ...WIRING DIAGRAMS MIG 100EN 105EN 30...
Page 31: ...WIRING DIAGRAMS MIG 151EN 31...
Page 32: ...PARTS DIAGRAM MIG 90EN 32...
Page 34: ...PARTS DIAGRAM MIG 100EN 105EN 34...
Page 36: ...PARTS DIAGRAM MIG 151TE 36...
Page 40: ......