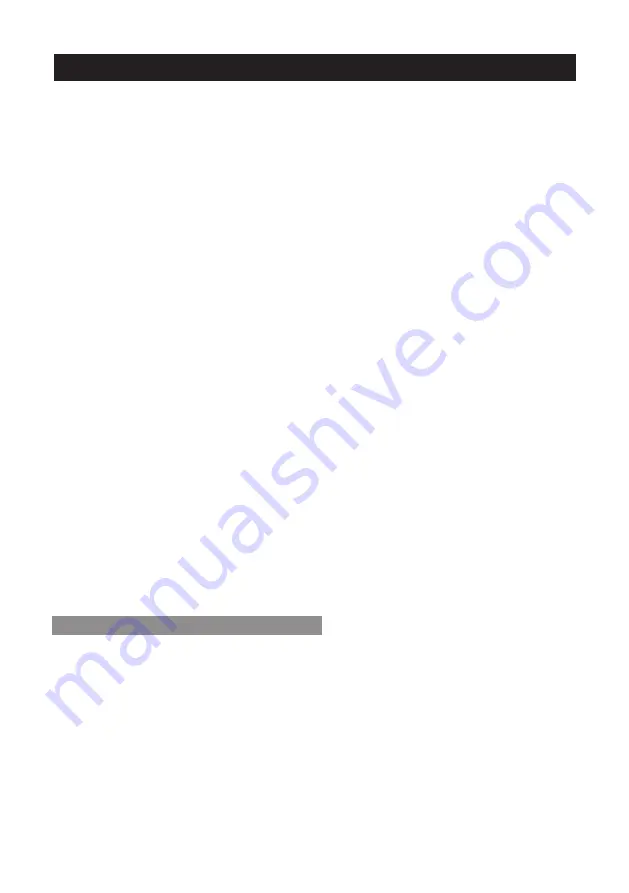
22
OPERATION
With the welding current set, and welding wire trimmed, set the wire feed control
to 6 , (8 for Aluminium). Plug the machine into the mains supply or switch on at the
isolator and ensuring all precautions have been taken and with the machine set
up correctly, lower the torch to the workpiece with one hand, whilst holding the
welding mask in the other.
Approach the work with the tip at an angle of approx. 45
O
and pull the torch
trigger fully. A welding current is now available at the tip.
As the electrode touches the workpiece, an arc will be struck......
BEFORE
it is struck,
cover the face with the face mask.
Maintain a gap of approx. 5 - 7mm from the workpiece to the tip, and feed the
wire into the molten pool at a steady rate, along the line of the proposed weld.
The speed of weld will depend upon the wire speed and welding current.
NOTES:
As MIG welding is an aquired skill, it is strongly advised that, if you are not fully
familiar with this type of welding, you practise on a piece of material with the
same characteristics as that of your workpiece until you are satisfied with the
result, and you have fine tuned your welder to produce a satisfactory weld.
One of the problems experienced with novice welders, is the welding wire sticking to the
contact tip. This is as a result of the wire feed speed being too slow. It is always better
therefore to start with too high a speed, and back off slightly, to avoid the possibility of the
wire welding itself to the tip. This is the reason position 6 is recommended for start up.
The Wire Feed control is for fine tuning the wire speed. The speed of wire delivery
will increase automatically as the current is increased from MIN to MAX, and vice
versa. Therefore, once the ideal speed is achieved, by fine tuning,it should not be
necessary to adjust this control when the welding current is changed.
Listen to the sound made. An irregular crackling sound denotes too high a wire
speed. Decrease the speed until a regular, strong buzzing sound is heard.
THERMAL OVERLOAD
Should the welder suddenly cut out during operation, it is possible that the thermal
overload has intervened.
The thermal overload is a safety device which shuts off the welder when the duty
cycle has been exceeded. This is to prevent damage to the machine caused by
overheating.
When this occurs, the ON/OFF switch will glow (amber). Allow the welder to cool,
until the amber light extinguishes before resuming.
For details of the duty cycle...i.e. the length of time the machine may be used
continuously, refer to the data and notes on page 29.
Summary of Contents for weld MIG 100EN
Page 29: ...WIRING DIAGRAMS MIG 90EN 29...
Page 30: ...WIRING DIAGRAMS MIG 100EN 105EN 30...
Page 31: ...WIRING DIAGRAMS MIG 151EN 31...
Page 32: ...PARTS DIAGRAM MIG 90EN 32...
Page 34: ...PARTS DIAGRAM MIG 100EN 105EN 34...
Page 36: ...PARTS DIAGRAM MIG 151TE 36...
Page 40: ......