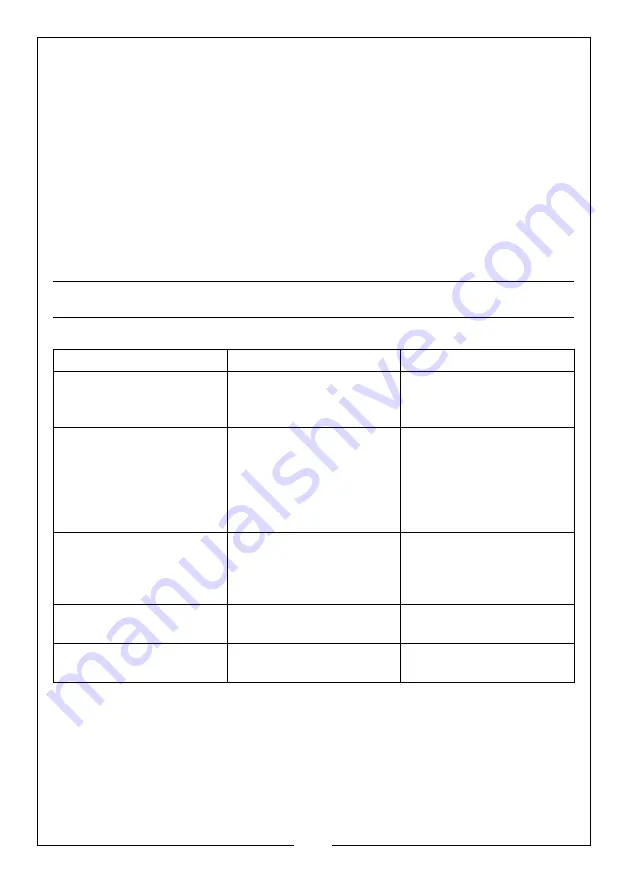
10
Parts & Service: 020 8988 7400 / E-mail: [email protected] or [email protected]
• Check the hydraulic connections for leaks. Replace or properly repair any
damaged or leaking hydraulic components before using. In the event of
leaking seals, oil can be topped up via the plug on the end of the pump. Oil
should be level with the bottom of the hole. If necessary top up with CLARKE
hydraulic oil, Part No. 3050830.
This task is carried out with the ram fully
retracted.
• If any rust is apparent it must be removed completely and the paint restored.
DE-COMMISSIONING PRODUCT
Should the product become completely unserviceable and require disposal,
draw off the oil into an approved container and dispose of the product and
the oil according to local regulations.
TROUBLESHOOTING
Problem
Probable Cause
Remedy
Pump unit will not work
Dirt on valve seat/warn
seals
Bleed pump unit or have
unit overhauled with new
seals
Pump will not produce
pressure
Pump feels hesitant
under load
Pump will not lower com-
pletely
Air-lock
Open the release valve
and remove the oil filler
plug. Pump the handle a
couple of full strokes and
close the release valve.
Replace the filler plug.
Pump will not deliver
pressure
Reservoir could be over-
filled or have low oil level.
Check oil level by
removing the filler plug
and topping up to the
correct level.
Pump feels hesitant
under load
Pump cup seal could be
worn out.
Have the cup seal
replaced.
Pump will not lower
completely
Air-lock
Release air by removing
the filler plug
Summary of Contents for STRONG-ARM CSA12F
Page 16: ......