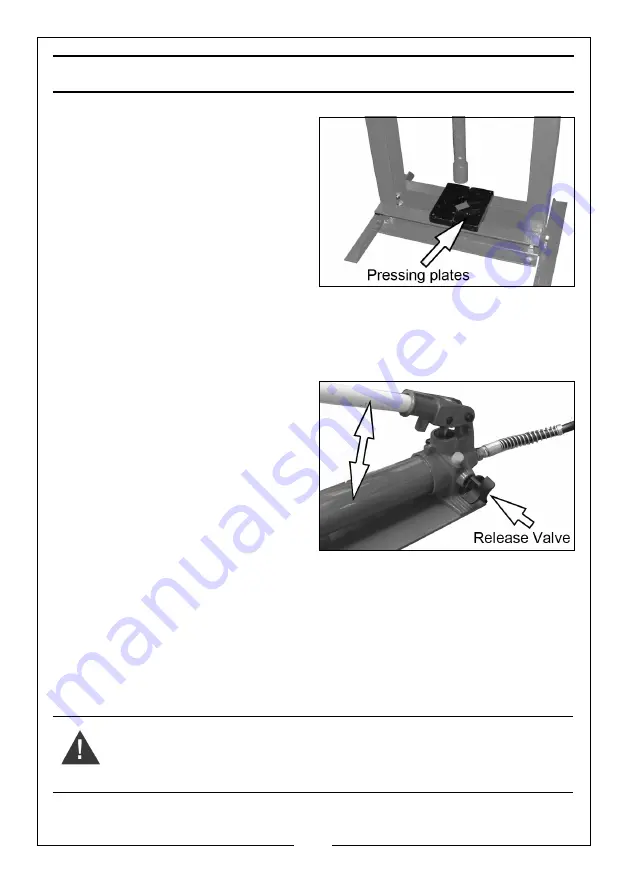
6
Parts & Service: 020 8988 7400 / E-mail: [email protected] or [email protected]
OPERATION
1. Place the workpiece on the
pressing plates supplied. It must
be completely stable and
supported by packing or shims
where required. Place the
workpiece on a combination of
these to give it stability.
NOTE:
Any packing pieces or shims
used MUST be capable of
withstanding the pressure
that will be brought to bear,
and MUST be of sufficient size with sufficient surface area, so as to
avoid the possibility of slipping or springing out. Mating surfaces
MUST be horizontal so that the force being exerted will NOT be at
an angle.
2. Close the release valve by turning
it clockwise until tightly closed.
3. Pump the handle to bring the ram
very lightly into contact with the
workpiece.
4. Position the workpiece so that the
desired point of contact is directly
beneath the centre of the ram.
5. When satisfied that the workpiece
is correctly aligned and is
completely stable in that position, slowly pump the handle so that the ram
begins to exert pressure on the workpiece. Continue to pump the handle
whilst standing to the side. Do NOT stand directly in front of the work, and
constantly monitor the process, ensuring the ram and work remain
completely in line and there is no risk of slipping.
6. When the process is complete, turn the release valve anti-clockwise in
small increments to release ram pressure and allow removal of the
workpiece.
WARNING: NEVER USE EXTENSIONS TO THE RAM PUMPING HANDLE
Summary of Contents for STRONG-ARM 7613025
Page 12: ......