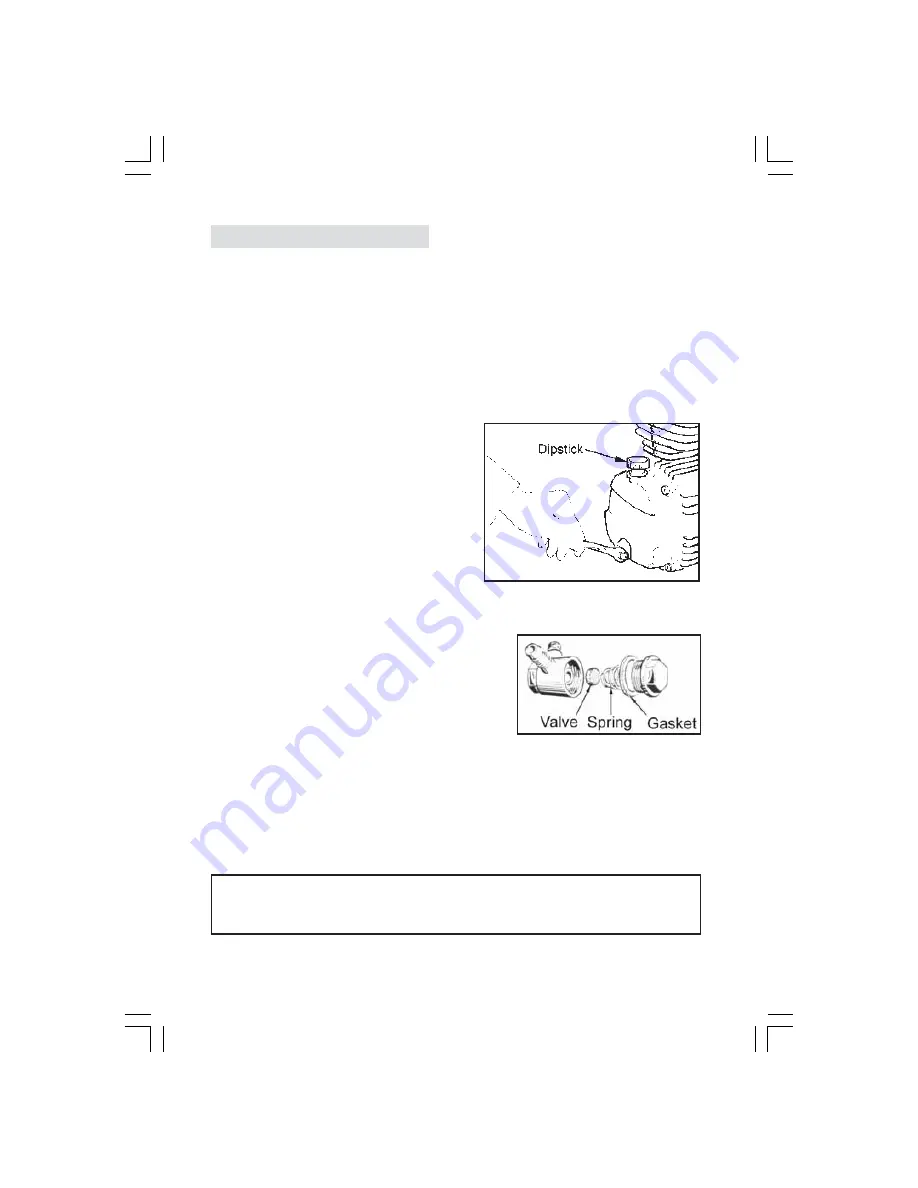
Fig. 6
9
B.
PERIODICALLY
1. After the first 5 hours of running the compressor, check the cylinder head
bolts and motor housing screws and re-tighten if any have worked loose.
2. Every 50 hours (more frequently if used in a dusty environment), clean the air
intake filter, by carefully removing the single screw securing the plastic cover
and withdrawing the sponge element from inside.
Clean the sponge and the inner housing. If necessary, the sponge filter may
be gently washed in warm soapy water, rinsed and allowed to dry thoroughly
before refitting. Ensure that the outer filter cover is then screwed back into its
original position.
If any part of the filter is damaged then you should obtain a replacement.
3. After the first 100 hours use, replace the
oil completely using Clarke SAE 40
compressor oil. Thereafter, replace the
oil completely after every 500 hours
of operation or every 6 months.
To empty the oil from the machine,
remove the drain plug from the
crankcase cover (see fig. 6).
4. Every 500 hours of operation or every
6 months
•
clean all the external parts of the
compressor.
(This cleaning makes the cooling
process more efficient and prolongs
the life of the machine).
•
Check and clean the inlet and outlet
valves
•
Examine the non-return valve and
replace the gasket if necessary (fig.7)
5. In the event of an air leak follow the procedure below:
•
Load compressor to maximum pressure
•
Unplug the compressor
•
With a brush and soapy water wet all ‘screwed’ air connections
•
Any leaks will show through the formation of air bubbles.
WARNING
NEVER UNSCREW A CONNECTION WHILST THE AIR RECEIVER IS UNDER PRESSURE.
ALWAYS MAKE CERTAIN THAT THE TANK HAS FIRST BEEN EMPTIED.
Fig. 7
Parts List item No. 59