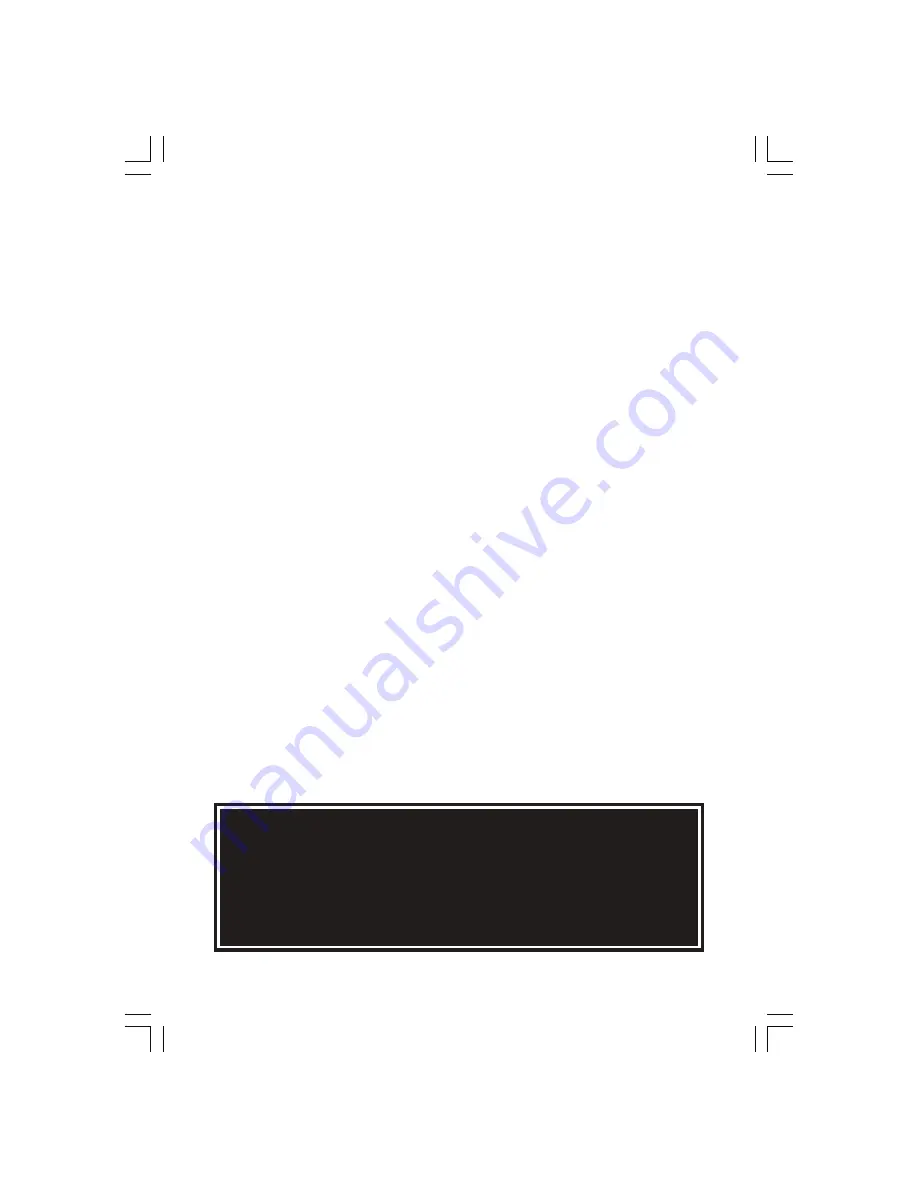
✗
NEVER
use or store in a wet/damp environment. DO NOT EXPOSE TO RAIN.
✗
NEVER
continue to weld, if,
at any time
, you feel even the smallest electric shock.
Stop welding IMMEDIATELY, and DO NOT attempt to use the machine until the fault
is diagnosed and corrected.
✗
NEVER
point the MIG torch at any person or animal.
✗
NEVER
touch the MIG torch nozzle until the welder is switched OFF
and the nozzle has been allowed to cool off.
✗
NEVER
connect, disconnect, or attempt to service the MIG torch,
until the machine is switched OFF and disconnected from the mains
supply.
✗
NEVER
allow the cables to become wrapped around the operator or
any person in the vicinity.
12
DANGER - ELECTRIC SHOCK CAN BE FATAL.
A person qualified in first aid should always be present in the working area.
If person is unconscious and electric shock is suspected, do not touch the person if
he or she is in contact with the welder or cables. Disconnect the welder from the
power source and then use First Aid. Dry wood, or other insulating material can be
used to move cables, if necessary, away from the person.
Summary of Contents for MIG85ENB
Page 24: ...PARTS DIAGRAM 24...