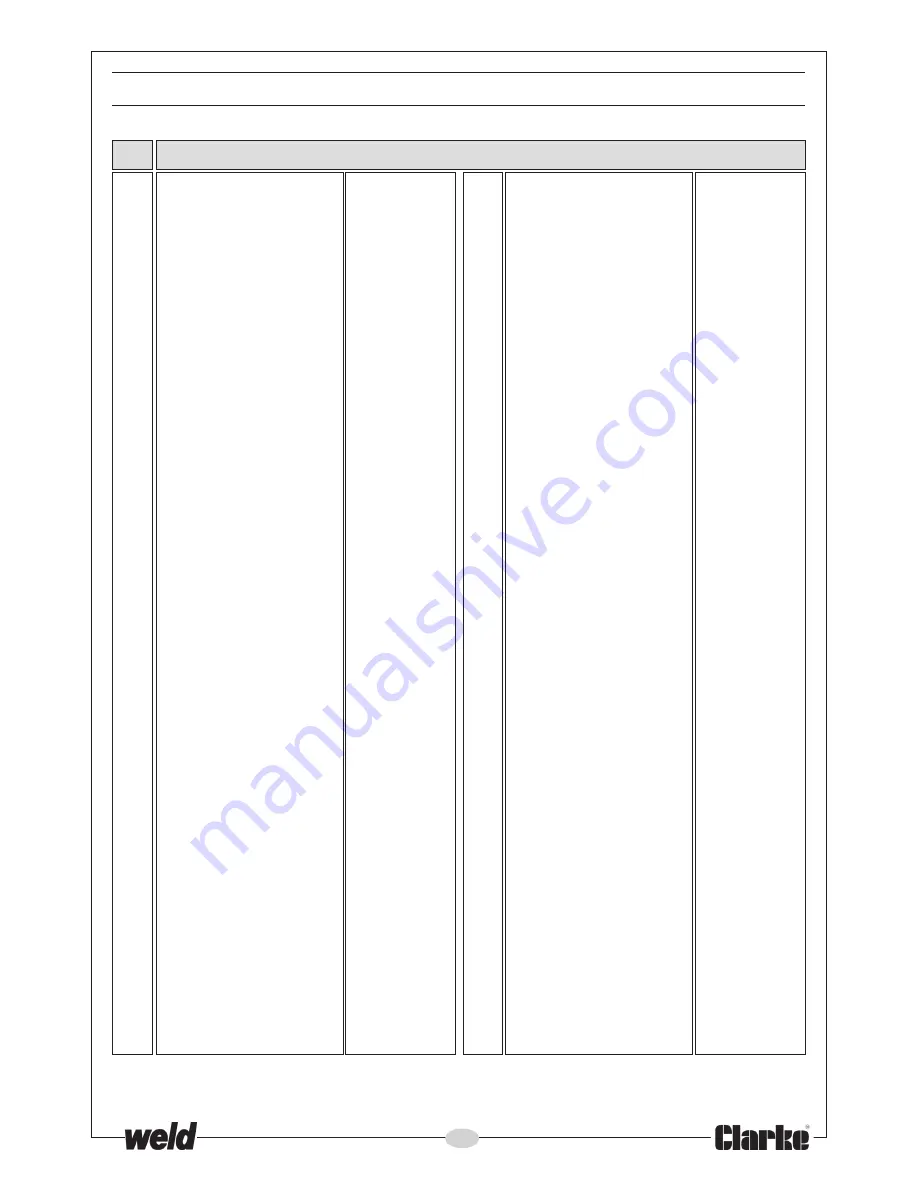
35
28
29
30
31
32
33
34
35
36
37
38
39
40
40
40
41
42
---
44
45
46
47
48
PARTS LIST - MIG270TE
No. Description
Part No.
No. Description
Part No.
01
02
03
04
05
06
07
08
09
10
11
12
13
14
15
16
17
18
19
20
21
22
23
24
25
26
27
Wire Feed Motor 42V
EM22810006
P.C. Board
EM22710051
Gas Solenoid Valve
EM22900035
Ther Support
EM04600113
Rectifier
EM22400029
Fan
EM22800005
Front Panel
EM33710295
Front Frame
EM21690285
Euro Torch Adaptor
EM23005048
Green Pilot-light Switch
EM22200005
Fuse 1A 250V
EM22220002
Fuse Holder 3A 250V
EM22220016
Potentiometer Knob
EM04600332
Right Side Panel
EM33705626
Zinc Chain 0,76 Mt
EM04600205
Rear Panel
EM33715096
Compl. Spool Holder
EM04600275
Mat For Tools
EM30905045
Upper Panel PVC
EM33705628
Dividing Panel PVC
EM33720211
Handle
EM21600042
Torch Connection Cover
EM21690267
Switch 16 A
EM22205030
Contactor
EM22225022
Auxiliary Transformer
EM44140036
Transformer 230/400V
EM44125038
Al Side Winding 230V
EM44025084
Input Cable
EM20220030
Black Hose
EM30900027
Rear Wheel
EM21625048
Castor
EM21625003
Switch Knob
EM04600268
Female Dinse Plug
EM22100002
Orange Pilot-lamp 24V
EM22610011
Wheels Axle
EM55200036
Cable Clamp
EM21605010
Lower Panel
EM33700317
Left Access Panel
EM33705627
Al.. Wire Gears
EM44410017
Wire Feed Roll 0,6-0,8mm
EM33805003
Wire Feed Roll 1,0-1,2mm
EM33805005
Wire Feed Roll 0,8-1mm Nylon EM33805104
Wire Block Roll
EM33805007
Slide Clip
EM21690226
- - - - - - - - - - - - - - -
- - - - - - - - -
Earth Clamp 300A
EM22110033
Earth Cable
EM43210167
Dinse Plug
EM22100001
Torch-bl/blk Handle
EM23000424
Reducer 2/Gauges
EM22905018
Face Mask
EM21905029
Transparent Glass
EM21905020
Dark Glass
EM21905024
- -
- -
- -
Summary of Contents for MIG220TE
Page 1: ...OPERATING MAINTENANCE INSTRUCTIONS 11 16 MIG220TE MIG255TEC MIG270TE WELDERS...
Page 14: ...14 GENERAL LAYOUT Fig 2...
Page 27: ...27 WIRING DIAGRAM MIG220TE...
Page 28: ...28 WIRING DIAGRAM MIG255TEC...
Page 29: ...29 WIRING DIAGRAM MIG270TE...
Page 30: ...30 PARTS DIAGRAM MIG220TE...
Page 32: ...32 PARTS DIAGRAM MIG255TEC...
Page 34: ...34 PARTS DIAGRAM MIG270TE...
Page 36: ......