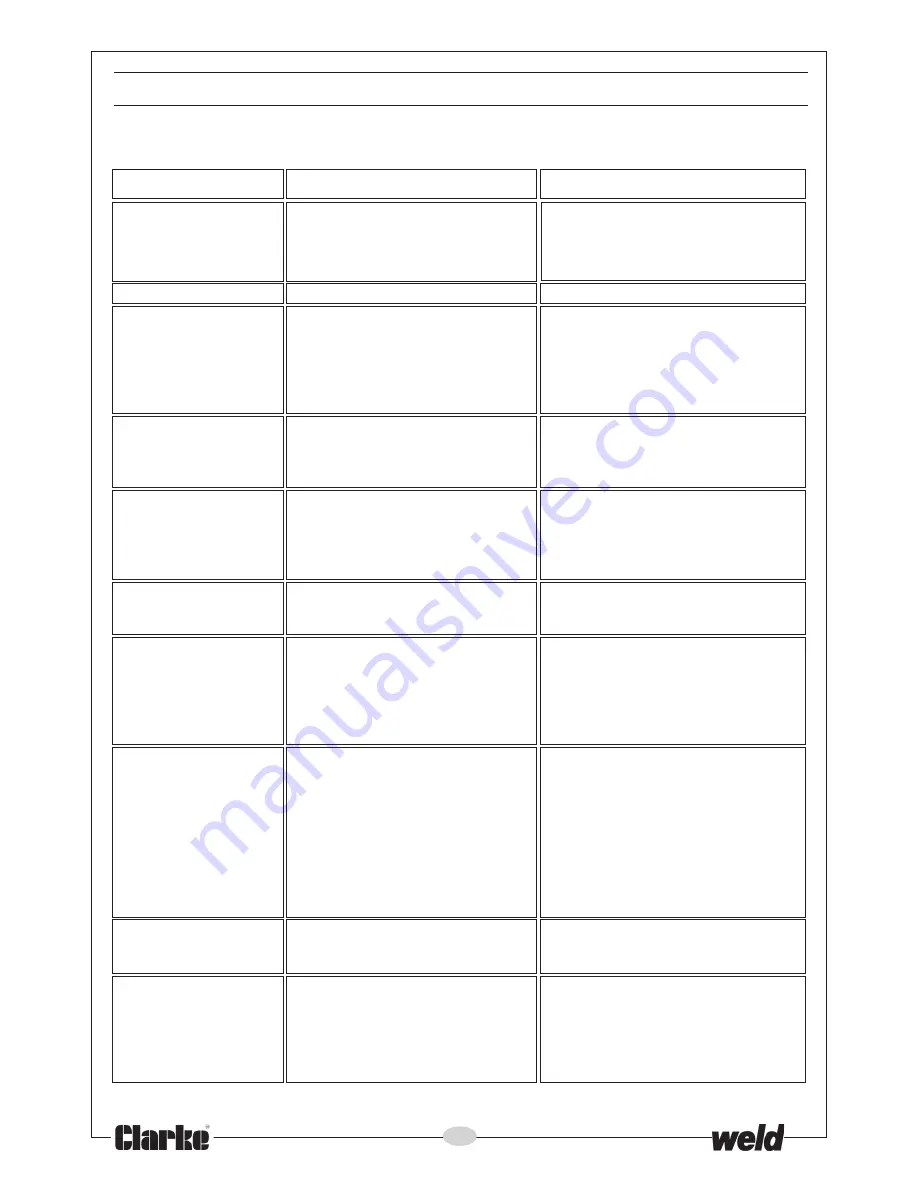
26
Your
Clarke
Mig Welder has been designed to give long and trouble free service. If, however,
having followed the instructions in this booklet carefully, you still encounter problems, the
following points should help identify and resolve them.
PROBLEM
CAUSE
REMEDY
1. No “life” from welder
a) Check fuses and mains lead
a) Replace fuses as necessary If
problem persists return welder to
your local dealer
b) Check fuse size
2. No wire feed
Motor malfunction
Return welder to your local dealer
3. Feed motor operates
a) Insufficient Feed Roller Pressure
a) Increase roller pressure
but wire will not feed
b) Burr on end of wire
b) Re-cut wire square with no burr
c) Liner blocked or damaged
c) Clean with compressed air or
replace liner.
d) Inferior wire
d) Use only good “clean” wire
e) Roller worn out
e) Replace roller
4. Wire welds itself to tip
a) Wire feed speed too low
a) Unscrew tip, cut wire and fit new tip
Increase wire speed before
operating again
b) Wrong size tip
b) Fit correct size tip
5. Wire feeds into ‘birds
a) Wire welded to tip
a) As above plus reduce feed roller
nest’ tangle
pressure so that if blockage occurs
wire slips on roller i.e. no feed
b) Wire liner damaged preventing
b) Renew wire liner
smooth operation
6. Loose coils of wire
Drum brake too slack
Tighten drum brake
tangle around wire
Caution: Do not over-tighten
drum inside machine
7. Erratic wire feed
a) Drum brake too tight
a) Loosen drum brake slightly
b) Feed roller worn
b) Check and replace if necessary
c) Insufficient pressure on feed roller
c) Increase pressure on feed roller
Caution: Do not over-tighten
d) Wire dirty, rusty, damp or bent
d) Re-cut wire and ensure it is clean
e) Liner partially blocked
e) Clean with compressed air
8. Poor quality welds
a) Insufficient gas at weld area
a) Check that gas is not being blown
away by draughts and if so move
to more sheltered weld area. If not
increase gas supply
b) Incorrect gas/wire combination
b) Consult your MIG welding manual
for correct set-up
c) Rusty, painted, damp, oil or
c) Ensure workpiece is clean and dry
greasy workpiece
d) Rusty/dirty wire
d) Ensure wire is clean and dry
e) Poor earth contact
e) Check earth clamp/work onnection.
9. Wire jams in tip when
a) Tip too small
a) Use slightly oversize tip ie., for 0.8mm
welding aluminium
wire use 1mm tip. (Note: Applies to
aluminium only)
10. Welder cuts out
a) Duty cycle exceeded
a) Allow welder to cool 15-30 mins
whilst in use
(auto cut-out operates)
before continuing
Note: If duty cycle is continually
exceeded, damage to the welder
may result, and welder output is
probably too small for application.
If you have any problems which cannot be resolved by reference to the above, or if you
TROUBLESHOOTING
Summary of Contents for MIG220TE
Page 1: ...OPERATING MAINTENANCE INSTRUCTIONS 11 16 MIG220TE MIG255TEC MIG270TE WELDERS...
Page 14: ...14 GENERAL LAYOUT Fig 2...
Page 27: ...27 WIRING DIAGRAM MIG220TE...
Page 28: ...28 WIRING DIAGRAM MIG255TEC...
Page 29: ...29 WIRING DIAGRAM MIG270TE...
Page 30: ...30 PARTS DIAGRAM MIG220TE...
Page 32: ...32 PARTS DIAGRAM MIG255TEC...
Page 34: ...34 PARTS DIAGRAM MIG270TE...
Page 36: ......