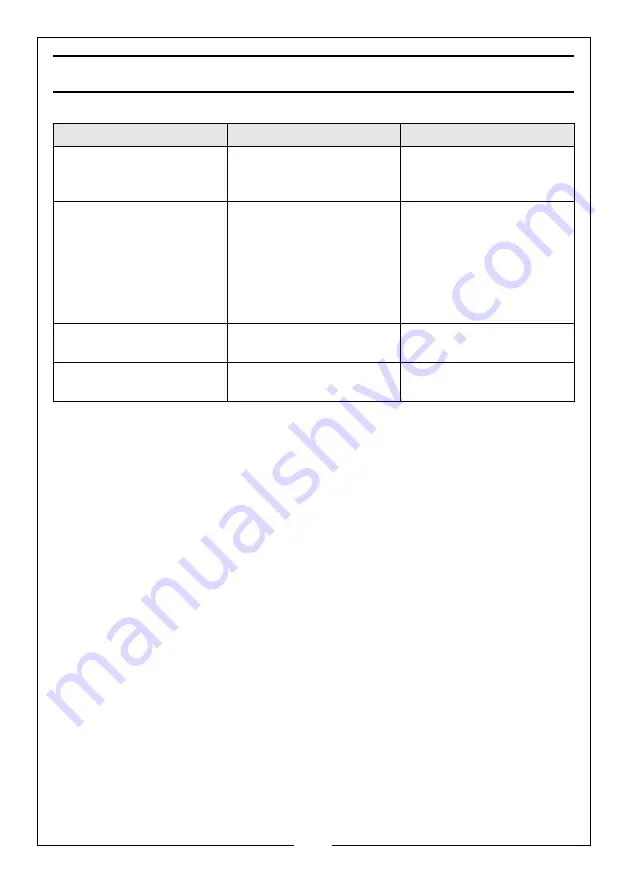
12
Parts & Service: 020 8988 7400 / E-mail: [email protected] or [email protected]
TROUBLESHOOTING
If this does not solve the problem, contact the CLARKE Sevice department on
020 8988 7400.
Problem
Probable Cause
Remedy
Pump will not work.
Dirt on valve seat/worn
seals.
Bleed pump unit or have
unit overhauled with new
seals by your dealer.
Pump will not produce
pressure.
Pump feels hesitant
under load.
Air-lock.
See “Purging the
Hydraulic System” on
page 7. Open the
release valve and pump
the handle a couple of
full strokes. Close the
release valve.
Pump feels hesitant
under load.
Pump cup seal could be
worn out.
Have the cup seal
replaced by your dealer.
Piston will not retract
completely.
Air-lock.
Release air by removing
the filler plug.
Summary of Contents for 7615203
Page 20: ......