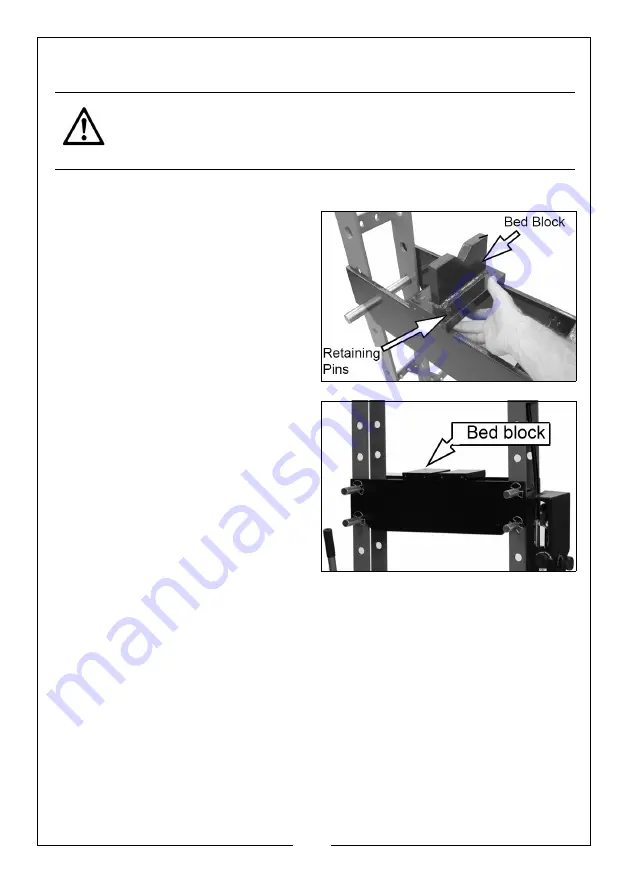
9
Parts & Service: 020 8988 7400 / E-mail: [email protected] or [email protected]
4. Repeat until the bed is at the required height, with the bed supporting pins
are secured using the spring butterfly clips.
POSITIONING THE PRESSING BLOCKS
The bed blocks can be placed on
the bed with either the flat face or
the V-supports facing upwards.
They are prevented from slipping out
of position by the retaining pins which
drop down within the confines of the
bed side members.
Check all parts are secure and
correctly aligned before using the
press.
CAUTION: THE BED HEIGHT SHOULD ONLY BE RAISED OR LOWERED ONE
HOLE AT A TIME, WORKING ALTERNATELY FROM ONE SIDE AND THEN THE
OTHER, FAILURE TO WORK IN THIS WAY MAY CAUSE THE BED TO FALL
AND CAUSE INJURY TO THE OPERATOR.
Summary of Contents for 7615201
Page 20: ......