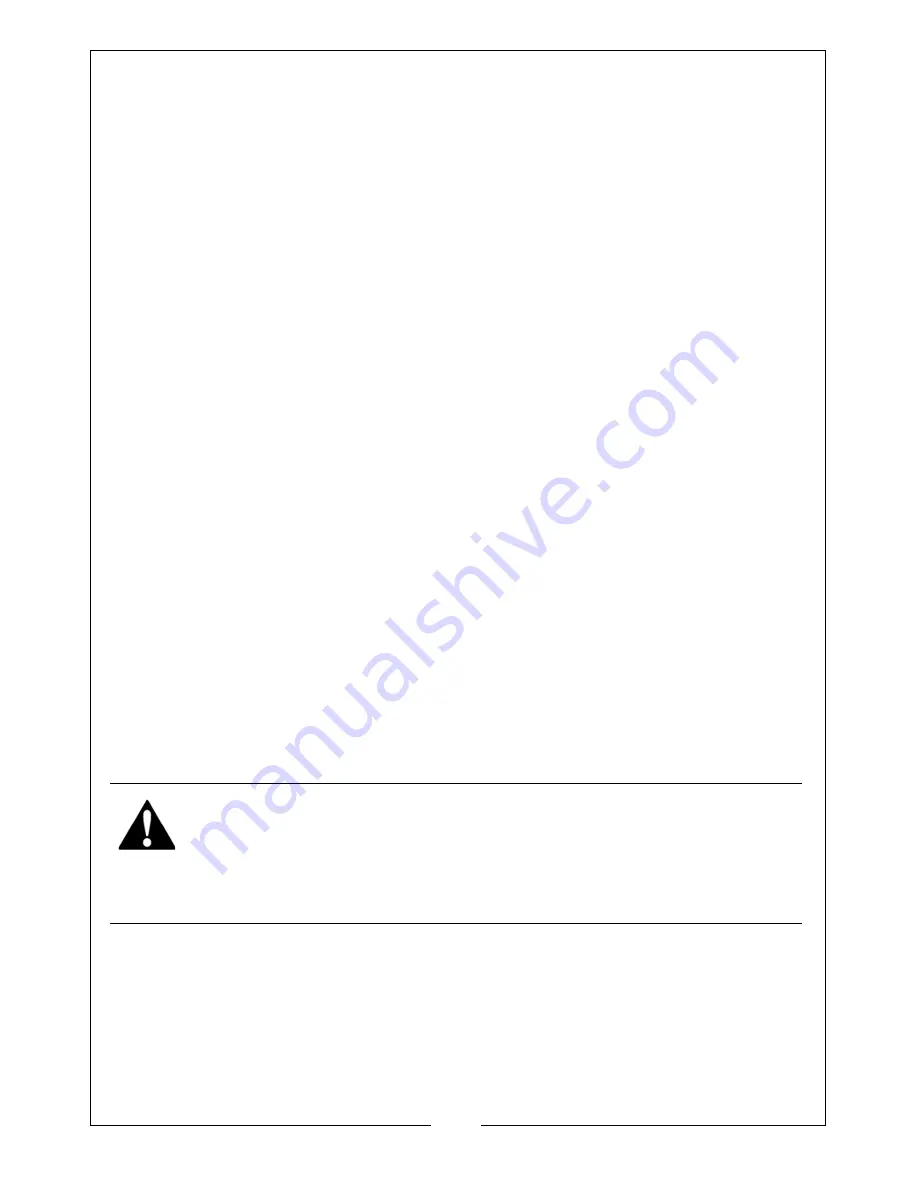
4
Parts & Service: 020 8988 7400 / E-mail: [email protected] or [email protected]
5. ALWAYS disconnect the machine from the power supply before carrying
out any servicing or changing of accessories.
6. Before further use of the tool, it should be carefully checked to determine
that it will operate properly and perform its intended function. Check for
alignment of moving parts, binding of moving parts, breakage of parts,
mounting or other condition that may affect its operation.
7. Have defective switches repaired by your Clarke Service Department. Do
not use a tool if the switch does not turn it on and off.
8. ALWAYS check for any damage or any condition that could affect the
operation of the machine. Damaged parts should be properly repaired.
9. NEVER
remove the cover panel unless the machine is disconnected from
the power supply, and never use the machine with cover panels removed.
10. Have your machine repaired by a qualified person. This machine complies
with the relevant safety rules. Repairs should only be carried out by
qualified persons using original spare parts, otherwise this may result in
considerable danger to the user.
11. NEVER use this product for any other purpose than that described in this
booklet.
12. NEVER abuse the power cable by yanking the cable to disconnect it from
the socket. Keep the cable away from heat, oil or sharp edges.
13. Guard against electric shock. Avoid body contact with earthed surfaces.
14. If the machine should be used outdoors, use only extension cables
intended for outdoor use and marked accordingly.
15. Avoid accidental starting by making sure the power switch is off before
plugging in the power cable.
ADDITIONAL SAFETY RULES FOR DRILL PRESSES
1. IMPORTANT: You should not operate this machine unless you are thoroughly
familiar with drilling machines and drilling techniques. If there is any doubt
whatsoever you should consult a qualified person.
2. NEVER operate the machine until it is completely assembled and you have
read and understood this entire manual.
CAUTION: AS WITH ALL MACHINERY, THERE ARE CERTAIN HAZARDS
INVOLVED WITH THEIR OPERATION AND USE. EXERCISING RESPECT AND
CAUTION WILL CONSIDERABLY LESSEN THE RISK OF PERSONAL INJURY.
HOWEVER, IF NORMAL SAFETY PRECAUTIONS ARE OVERLOOKED, OR
IGNORED, PERSONAL INJURY TO THE OPERATOR, OR DAMAGE TO
PROPERTY MAY RESULT.
Summary of Contents for 6505512
Page 24: ......