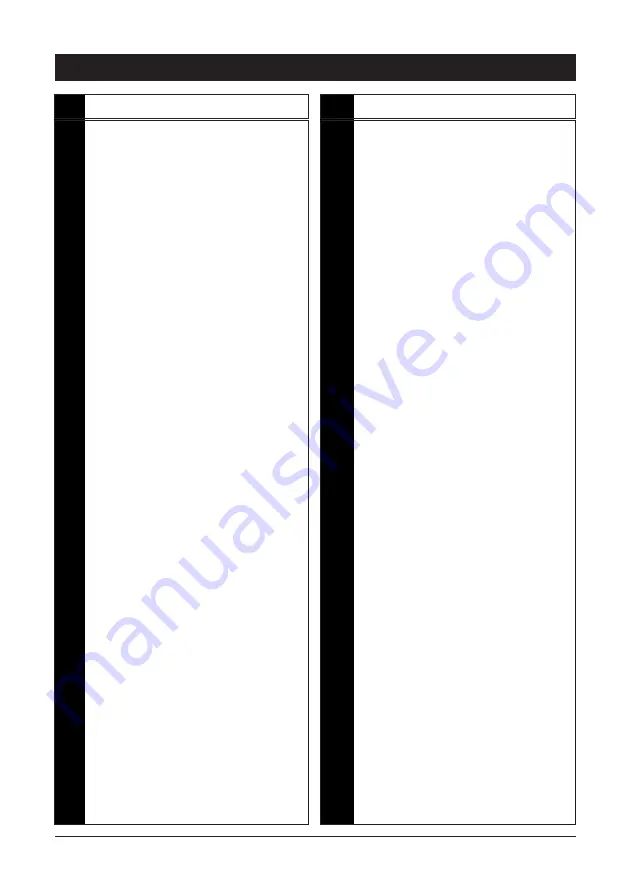
Spare Parts List
cont.
102
103
106
107
108
109
110
111
112
113
114
115
116
117
118
119
120
121
122
123
124
125
126
127
128
129
130
131
132
133
134
135
135A
136
137
138
138A
138B
138C
138D
139
140
141
142
143
144
145
146
147
148
149
150
151
152
153
153A
154
155
156
157
158
159
160
161
162
163
164
165
166
167
168
169
170
171
172
172A
173
174
175
No.
DESCRIPTION
PART NO.
No.
DESCRIPTION
PART NO.
Round Head Screw
M00101102
Bearing Bracket
M00101103
Round Head Screw
M00101106
Hex Screw
M00101107
Supporting Plate
M00101108
Flat Washer
M00101109
Spring Washer
M00101110
Hex Screw
M00101111
Toggle Plate
M00101112
Spring Washer
M00101113
Round Head Screw
M00101114
Frame Assembly
M00101115
Grub Screw
M00101116
Hex Screw
M00101117
Adjuster Post
M00101118
Wheel Shaft
M00101119
O-Ring
M00101120
Wheel
M00101121
Bearing
M00101122
Circlip
M00101123
Flat Washer
M00101124
Spring Washer
M00101125
Hex Screw
M00101126
Steel Wire Brush
M00101127
Hex Screw
M00101128
Flat Washer
M00101129
Tap Screw
M00101130
Mounting Plate
M00101131
Circlip
M00101132
Driving Wheel
M00101133
Conical Head Screw
M00101134
Chip Fence
M00101135
Vert. Cutting Table
M00101135A
Guide Block
M00101136
Guide Block Support
M00101137
Locking Screw
M00101138
Spring Pin
M00101138A
Rubber Plate
M00101138B
Locking Plate
M00101138C
Pan Screw
M00101138D
Locking Clip
M00101139
Tube
M00101140
Hex Screw
M00101141
Flat Washer
M00101142
Adapter
M00101143
Rear Adj. Post
M00101144
Tap assembly
M00101145
Oil Drain Tube
M00101146
Protect Cover
M00101147
Hex Screw
M00101148
Convex Screw
M00101149
Spring Washer
M00101150
Flat Washer
M00101151
Locking Cover
M00101152
Water Tray
M00101153
Plate
M00101153A
Fitting
M00101154
Compressed Frame
M00101155
Round Cap Screw
M00101156
Cove & Base
M00101157
Convex Screw
M00101158
Hex Nut
M00101159
Shaft
M00101160
Wheel
M00101161
Locking Cap
M00101162
Fluid Reservoir
M00101163
Upper Cover
M00101164
Cooling Fluid Pump
M00101165
Lock Cover Pump
M00101166
Round Cap Screw
M00101167
Cover & Base
M00101168
Convex Screw
M00101169
Flat Washer
M00101170
Hex Nut
M00101171
Cord Brush
M00101172
Strain Relief
M00101172A
Cover Plate
M00101173
Flat Washer
M00101174
Pan Head Screw
M00101175
19