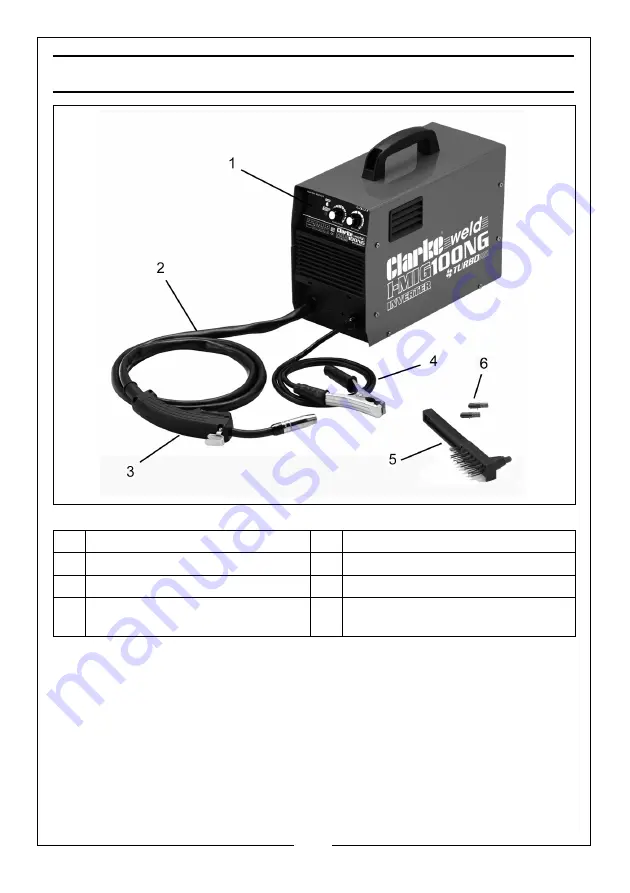
12
Parts & Service: 020 8988 7400 / E-mail: [email protected] or [email protected]
OVERVIEW
When unpacking, any damage or deficiency should be reported to your
CLARKE dealer immediately.
NO DESCRIPTION
NO DESCRIPTION
1
Control Panel
4
Earth Clamp
2
MIG Gun Hose
5
Combination wire brush/hammer
3
MIG Torch
6
Copper Torch Tips - 2 x 0.9 mm,
loose & 1 x 0.9 mm (fitted)
Summary of Contents for 6015610
Page 28: ......