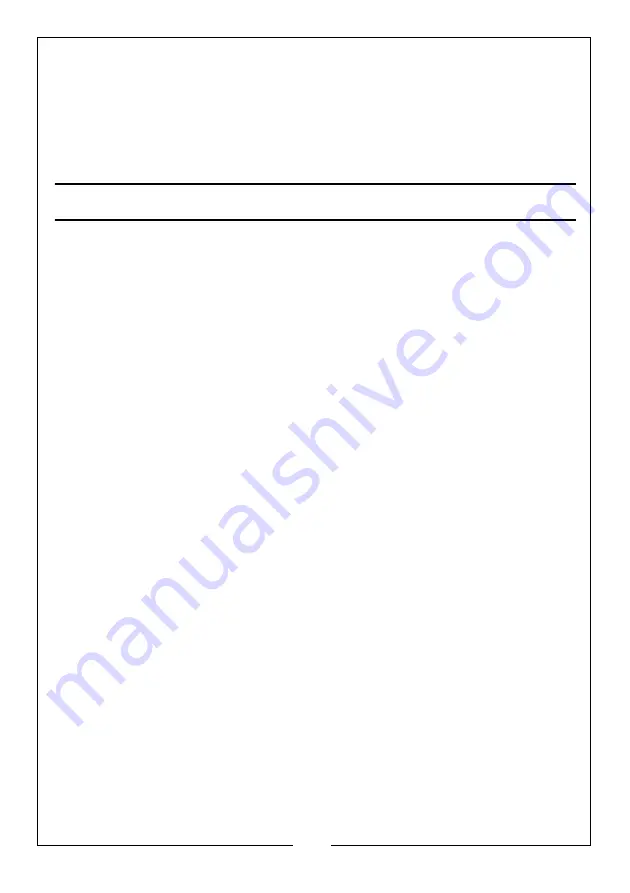
5
Parts & Service: 020 8988 7400 / E-mail: [email protected] or [email protected]
A container with unknown contents should be cleaned (see paragraph
above). Do NOT depend on sense of smell or sight to determine if it is safe to
weld or cut. Hollow castings or containers must be vented before welding or
cutting as they can explode.
In explosive atmospheres, never weld or cut where the air may contain
flammable dust, gas, or liquid vapours.
ELECTRIC ARC (MIG, TIG) WELDING
Comply with precautions in above, and this section. Arc welding, properly
done, is a safe process but a careless operator invites trouble. The equipment
carries high currents at significant voltages. The arc is very bright and hot.
Sparks fly, fumes rise, ultraviolet and infrared energy radiates and work pieces
are hot. The wise operator avoids unnecessary risks and protects himself and
others from accidents.
A) BURN PROTECTION
The welding arc is intense and visibly bright. It’s radiation can damage eyes,
penetrate lightweight clothing, reflect from light coloured surfaces and burn
the skin and eyes. Skin burns resemble acute sunburn, those from gas -
shielded arcs are more severe and painful.
DON’T GET BURNED! FOLLOW ALL SAFETY PRECAUTIONS!
PROTECTIVE CLOTHING
Wear long sleeved clothing (particularly for gas shielded arc) in addition to
gloves, apron and strong shoes. As necessary, use additional protective
clothing such as leather jacket or sleeves, flameproof apron, and fire-resistant
leggings. Avoid outer garments of untreated cotton. Bare skin protection:
Wear dark substantial clothing, Button collars closed to protect the chest and
neck and button any pockets to prevent entry of sparks.
EYE AND HEAD PROTECTION
Protect eyes from exposure to arc. NEVER look at an electric arc without
protection. Welding helmet or shield containing an appropriate filter plate
(Please refer to the section ‘Welding Shield). Place over face before striking
arc. Protect filter plate with a clear cover plate. Cracked or broken helmet or
shield should NOT be worn; radiation can pass through to cause burns.
Cracked, broken, or loose filter plates must be replaced IMMEDIATELY.Replace
clear cover plate when broken, pitted, or spattered. WE SUGGEST you wear
flash goggles with side shields under the helmet, to give some protection to
the eyes should the helmet not be lowered over the face before an arc is
struck. Looking at an arc momentarily with unprotected eyes (particularly high
Summary of Contents for 6014505
Page 32: ......