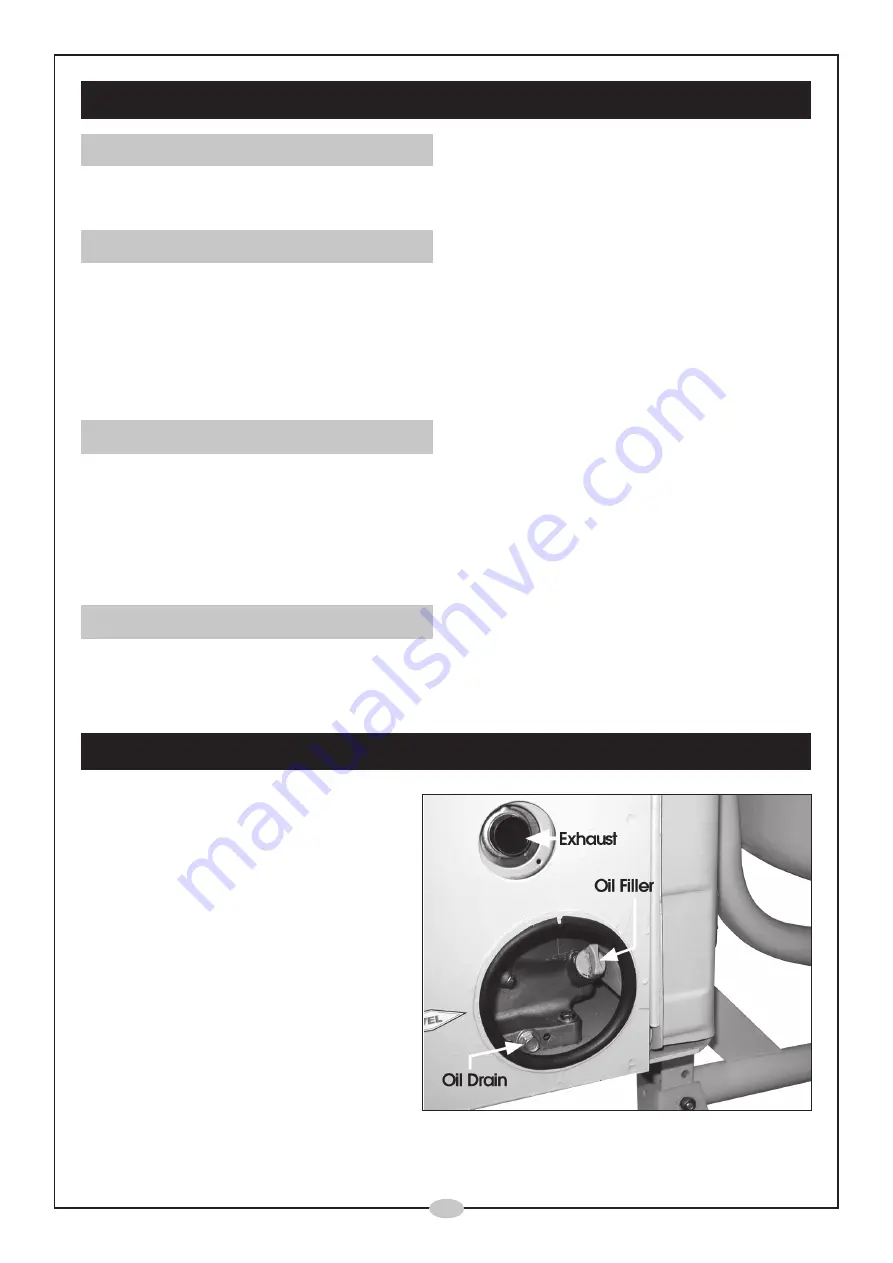
o
MAINTENANCE - General
Before each use
Inspect the machine to ensure it is not damaged and will perform its normal functions correctly.
If any damage is apparent, have it fixed before putting into service.
Periodically
Inject a few drops of light oil into the oil points, located on top of the Bearing Blocks and
rotate the drum to ensure distribution of oil within the bearing surface.
Inspect the paintwork and remove any rust that may be apparent before touching up where
necessary, with a rust resistant paint.
It is recommended that the Collar be removed, at least annually, and grease smeared on the
serrated underside of the lower rim. Ensure the collar is replaced correctly.
After each use.
It is strongly recommended that the machine is hosed down thoroughly with clean water, taking care
to prevent water from entering the engines electrical components by wrapping a polythene sheet or
bag over the engine during the cleaning process.
Turn the drum so that it is face down to allow all water to drain off. Protect it from the elements
by covering with a tarpaulin. This is particularly important if the machine is to be stored for a
period of time.
Storage
It is possible to fold the leg and axle assembly beneath the frame by removing their upper
mounting bolts, and slackening off the lower mounting bolts so that the leg, or axle assy.
pivots beneath the frame.
MAINTENANCE - Engine
12
It is important to maintain the engine
according to the manufacturers
handbook, which accompanies this
manual.
The location of the Oil Filler, and Oil
Drain, is indicated in Fig.13.
Checking oil level, topping up and
changing the oil can all be done with
the engine cover in place, as can the
air filter replacement and spark plug
maintenance. For all other work it will
be necessary to remove the cover.
Summary of Contents for 3400820
Page 14: ...o PARTS DIAGRAM 14 14...
Page 16: ...o...