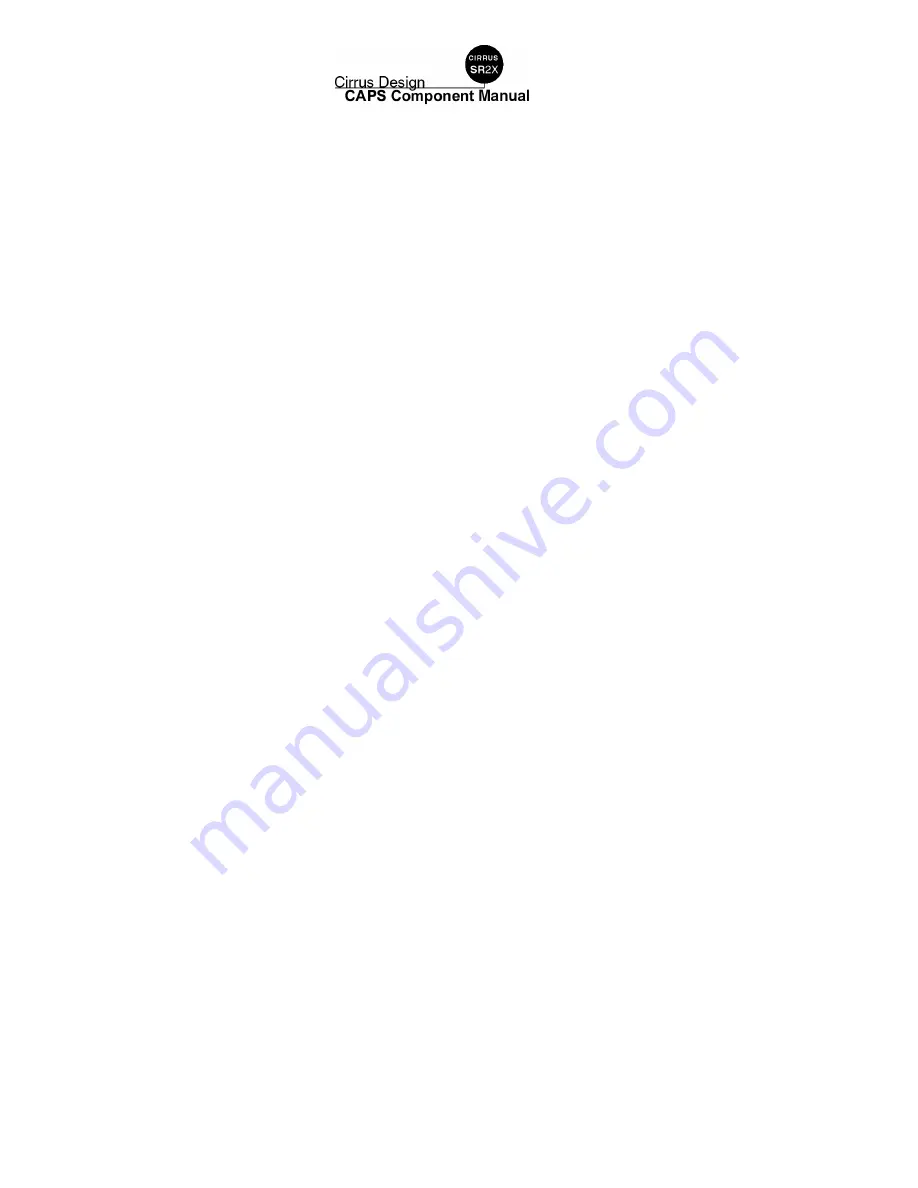
12128-001
95-01
Page 8
15 Sept 2002
(2)
Slider
To limit inflation loads, CAPS uses a slider to aerodynamically reef the parachute. The slider is a
flat annular shaped fabric panel with metal grommets attached to its perimeter. The parachute
suspension lines are routed through the grommets so that the slider is free to move along the
suspension lines. The slider, which has a significantly smaller diameter than the fully inflated
parachute, is positioned at the top of the suspension lines, next to the canopy skirt, when the
parachute is packed. It therefore limits the initial inflated diameter of the parachute and hence
the inflation loads. During inflation, the slider remains next to the skirt for a period of time that is
dependent on the dynamic pressure acting on the system. This allows the payload to decelerate
to a speed at which the parachute can fully inflate without generating excessive loads.
E. Airplane Attachment Harness (See Figure 95-014)
An aircraft harness system connects the parachute risers to the airplane primary structure. The CAPS
aircraft harness consists of two forward harness straps attached to the firewall and a rear harness
attached to the FS 222 bulkhead located directly in front of the parachute enclosure. The CAPS har-
ness system is designed to control the pitch dynamics of the airplane during the deployment cycle by
limiting the aft aircraft attachment harness length until the deployment cycle is complete.
The rear harness assembly has two sections of different length. The shorter section has a mechanical
release mechanism that is activated by two pyrotechnic reefing line cutters. The fuses on these line
cutters are initiated when the line cutter release pin is pulled when the harness is pulled taut during the
extraction. After 8 seconds, the line cutters fire, the longer section of the rear harness takes over and
the airplane assumes its touchdown attitude, approximately ten degrees nose down, to optimize occu-
pant protection.
The release mechanism design is based on a 3-ring release mechanism. This system uses a series of
metal rings routed through each other in a manner that provides a significant mechanical advantage.
For the mechanism to be released, each link must rotate through its adjacent ring or link. The force
necessary to hold the small link in its stowed position is considerably smaller than the force that is
being applied as a result of the overall load on the mechanism. On the CAPS system the last link is
held in place by a short length of nylon cord which is severed by the pyrotechnic reefing line cutters.
Summary of Contents for CAPS
Page 2: ......
Page 4: ......
Page 11: ...12128 001 95 01 Page 3 Figure 95 011 CAPS System and Deployment 15 Sept 2002 ...
Page 13: ...12128 001 95 01 Page 5 Figure 95 012 CAPS Handle and Ignition System 15 Sept 2002 ...
Page 15: ...12128 001 95 01 Page 7 Figure 95 013 Incremental Bridle and Deployment Bag 15 Sept 2002 ...
Page 17: ...12128 001 95 01 Page 9 Figure 95 014 Parachute Assembly and Line Cutters 15 Sept 2002 ...
Page 18: ...THIS PAGE INTENTIONALLY LEFT BLANK ...
Page 27: ...12128 001 95 01 Page 19 Figure 95 016 CAPS Cover Installation 15 Sept 2002 ...
Page 30: ...12128 001 95 01 Page 22 Figure 95 017 CAPS Rocket Assembly Sheet 1 of 2 15 Sept 2002 ...
Page 31: ...12128 001 95 01 Page 23 Figure 95 017 CAPS Rocket Assembly Sheet 2 of 2 15 Sept 2002 ...
Page 37: ...12128 001 95 01 Page 29 Figure 95 018 CAPS Activation System 15 Sept 2002 ...
Page 38: ...12128 001 95 01 Page 30 Figure 95 019 Sheet 1 of 2 CAPS Test Fixture 15 Sept 2002 ...
Page 39: ...12128 001 95 01 Page 31 Figure 95 019 Sheet 2 of 2 CAPS Test Fixture 15 Sept 2002 ...