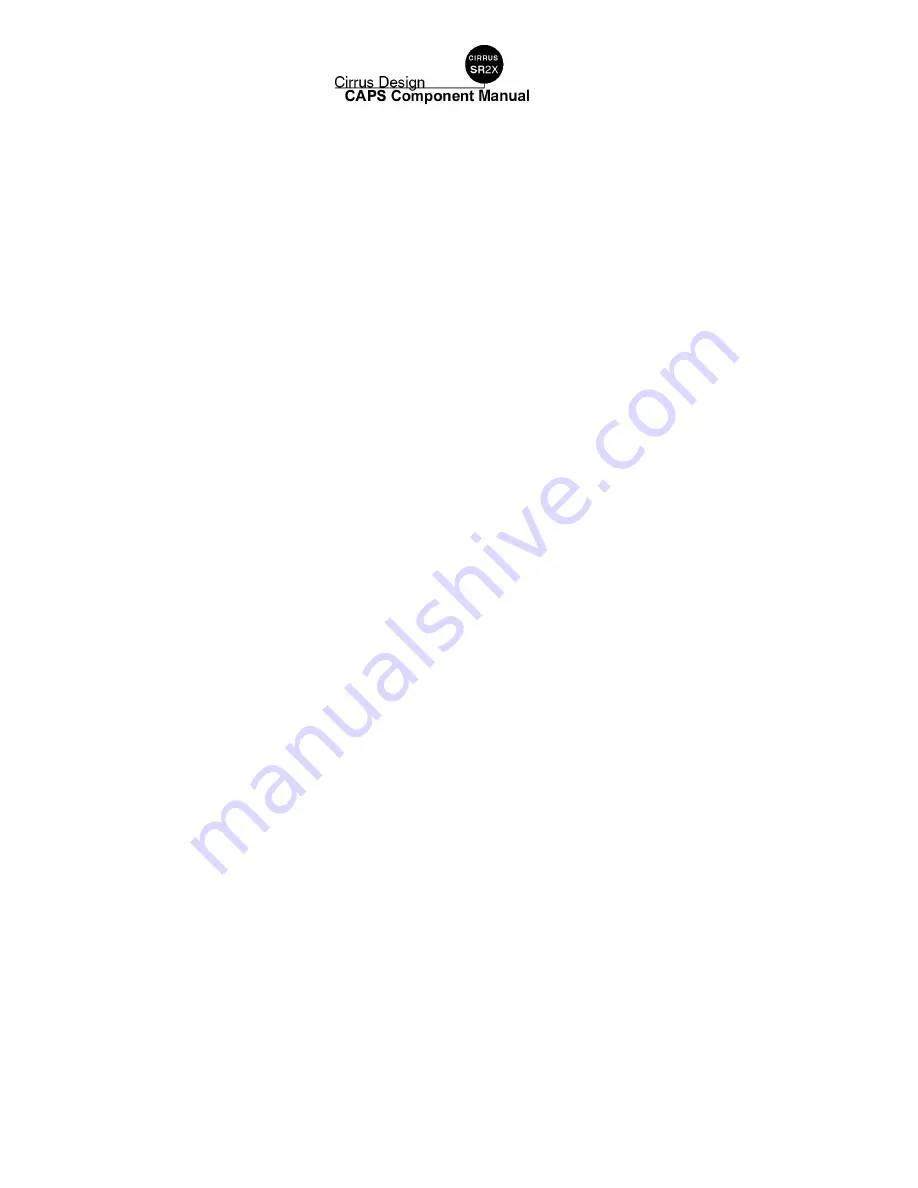
12128-001
95-01
Page 2
15 Sept 2002
3.
GENERAL
The airplane is equipped with a Cirrus Airplane Parachute System (CAPS) designed to bring the aircraft
and its occupants to the ground in the event of a life-threatening emergency.
CAPS consists of a parachute, a solid-propellant rocket to deploy the parachute, a rocket activation sys-
tem, and a harness imbedded within the fuselage structure.
A composite enclosure containing the parachute and solid-propellant rocket is mounted to the airplane
structure immediately aft of the baggage compartment bulkhead. The enclosure is covered and protected
from the elements by a thin composite cover.
The parachute is enclosed within a deployment bag that stages the deployment and inflation sequence.
The deployment bag creates an orderly deployment process by allowing the canopy to inflate only after the
rocket motor has pulled the parachute lines taut.
The parachute itself is a 2400-square-foot round canopy equipped with a slider, an annular-shaped fabric
panel with a diameter significantly less than the open diameter of the canopy. The canopy suspension lines
are routed through grommets so that the slider is free to move along the suspension lines. Since the slider
is positioned at the top of the suspension lines near the canopy, at the beginning of the deployment
sequence, the slider limits the initial diameter of the parachute and the rate at which the parachute inflates.
The canopy inflates as the slider moves down the suspension lines.
A three-point attachment harness connects the airplane to the parachute. The harness consists of two for-
ward straps faired into the fuselage skin and attached to the firewall, and one rear strap attached to FS 222
bulkhead located directly forward of the CAPS enclosure. The harness system is designed to control the
pitch dynamics of the airplane during the deployment cycle by limiting the aft attachment strap’s length until
the cycle is complete. This is accomplished by utilizing a variable length strap section. The shorter section,
which initially supports the load, employes a mechanical release that is activated by two pyrotechnic cut-
ters which fire when the short section is pulled taut during extraction. The harness strap then lengthens
and load is transferred to the longer section.
4.
DESCRIPTION AND OPERATION (SEE FIGURE 95-011)
Two separate and deliberate pilot actions are required to deploy the CAPS parachute. The first action
requires the pilot to remove the access cover from the activation handle enclosure. The second action
requires the pilot to pull the activation handle out, and down several inches.
Upon pulling the activation handle, the activation cable compresses the igniter’s steel spring, cocks the
plunger and the following sequence is initiated: When one half-inch of plunger travel is reached, captured
ball-bearings are released allowing the plunger to strike the firing pins. The firing pins strike two primers
which ignite the primary booster. The primary booster ignites a secondary booster ensuring ignition of the
larger rocket motor. Once ignited, the rocket propellant’s hot gases are exhausted through the nozzle and
the rocket bursts through the CAPS enclosure cover pulling the deployment bag from the enclosure. The
deployment bag then stages the suspension line deployment and inflation of the parachute. As the para-
chute inflates, the forward harness assembly grows taut, pulls free of the fuselage skin, and stops at the
firewall compression tube which supports the forward portion of the airplane. The rear harness’ shorter
section is pulled taut, initiates the pyrotechnic line cutters which sever the shorter lines, and allow the
longer harness section to support the aft load. The airplane then assumes its touchdown attitude; approxi-
mately ten degrees nose down, to optimize occupant protection.
Summary of Contents for CAPS
Page 2: ......
Page 4: ......
Page 11: ...12128 001 95 01 Page 3 Figure 95 011 CAPS System and Deployment 15 Sept 2002 ...
Page 13: ...12128 001 95 01 Page 5 Figure 95 012 CAPS Handle and Ignition System 15 Sept 2002 ...
Page 15: ...12128 001 95 01 Page 7 Figure 95 013 Incremental Bridle and Deployment Bag 15 Sept 2002 ...
Page 17: ...12128 001 95 01 Page 9 Figure 95 014 Parachute Assembly and Line Cutters 15 Sept 2002 ...
Page 18: ...THIS PAGE INTENTIONALLY LEFT BLANK ...
Page 27: ...12128 001 95 01 Page 19 Figure 95 016 CAPS Cover Installation 15 Sept 2002 ...
Page 30: ...12128 001 95 01 Page 22 Figure 95 017 CAPS Rocket Assembly Sheet 1 of 2 15 Sept 2002 ...
Page 31: ...12128 001 95 01 Page 23 Figure 95 017 CAPS Rocket Assembly Sheet 2 of 2 15 Sept 2002 ...
Page 37: ...12128 001 95 01 Page 29 Figure 95 018 CAPS Activation System 15 Sept 2002 ...
Page 38: ...12128 001 95 01 Page 30 Figure 95 019 Sheet 1 of 2 CAPS Test Fixture 15 Sept 2002 ...
Page 39: ...12128 001 95 01 Page 31 Figure 95 019 Sheet 2 of 2 CAPS Test Fixture 15 Sept 2002 ...