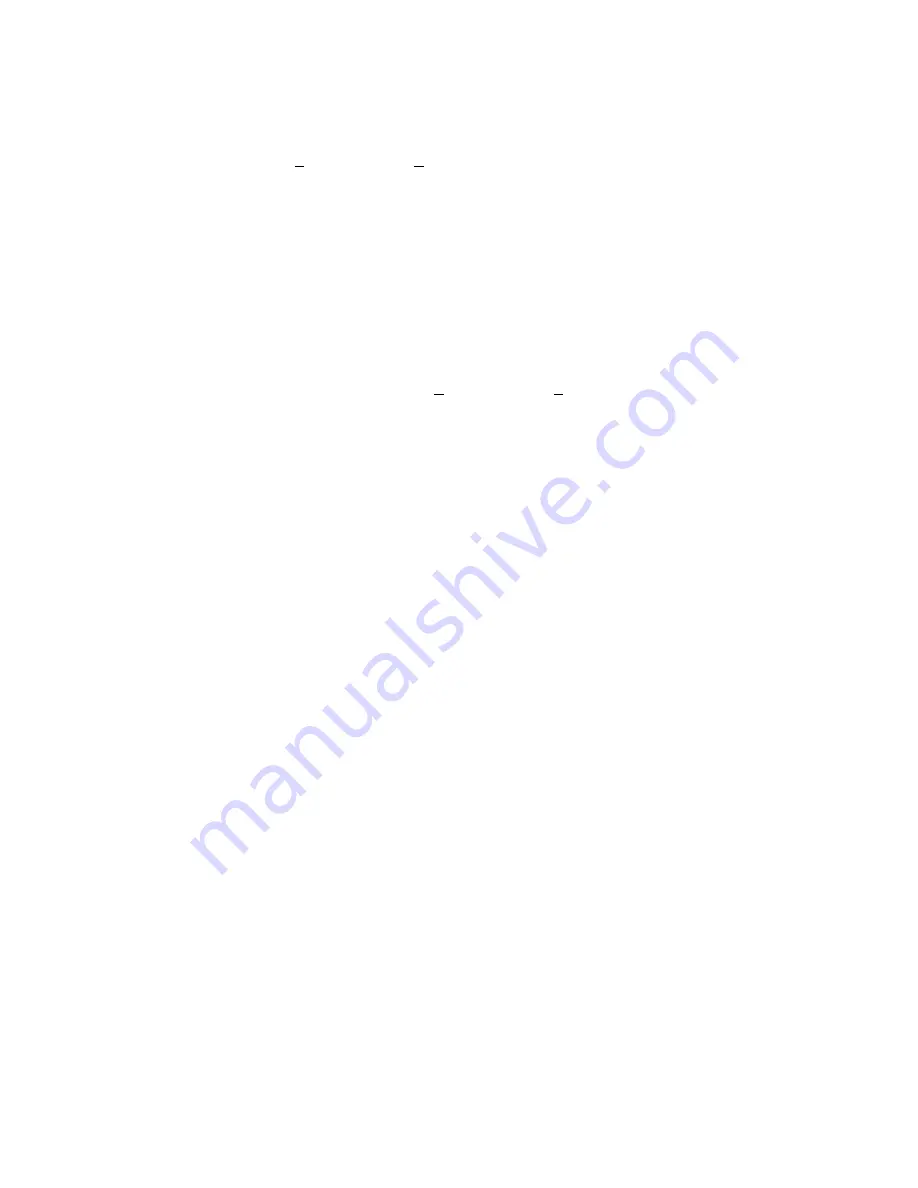
12
Step 5. Installation of Rotors and Setting Power Rotor End Clearance
Install woodruff key (26) in power rotor (13) key slot and install thrust collar (16) on key and
power rotor shaft. Seat squarely against shoulder. Slide power rotor (13), into outboard end
of pump. Install outboard end cover (17) and gasket (4) to case using bolts (2). Torque
bolts (2) to 85 + 10 ft-lbs. (115 + 19 Nm). Mount a dial indicator to inboard end cover (17)
and place indicator needle on power rotor coupling end face. Push power rotor axially into
pump until contact is made with outboard end cover. Zero bezel on dial indicator, then pull
power rotor axially out of pump until thrust collar contacts busing insert. Read and record
total axial movement of power rotor. Measure the thickness of laminated shim pack (36).
Reduce shim pack thickness by peeling away laminations until thickness is .015 to .020
inches (.38 to .51 mm) less than total power rotor axial movement. Remove outboard end
cover (15) and power rotor from pump. Remove thrust collar (16) and woodruff key (26)
from power rotor. Slide adjusted shim pack (36) onto power rotor shaft then install woodruff
key (26) and thrust collar (16). Make sure shims and thrust collar are seated squarely
against power rotor shoulder. Mesh threads of idler rotors onto power rotor and slide rotor
set into pump from outboard end. Re-install outboard end cover (17) and gasket (4) using
bolts (2). Torque bolts (2) to 155 + 10 ft-lbs. (189 + 13 Nm). Verify .015 to .020 inches (.38
to .51 mm) power rotor total axial movement using the dial indicator. Repeat above if
correct axial movement is not achieved.
Step 6.
Install Chesterton 180 cartridge mechanical seal (27) per instruction in Mechanical Seal
Section of this manual. See Section I.1.2.
K. INSTALLATION, ALIGNMENT, AND TROUBLESHOOTING
For instructions regarding Installation, Alignment and Trouble shooting see General Instruction Manual,
SRM00046.
L. FIELD AND FACTORY SERVICE AND PARTS
Imo Pump maintains a staff of trained service personnel that can provide pump installation, pump start-
up, maintenance/overhaul and troubleshooting supervision as well as installation and maintenance
training.
Our factories provide maintenance as well as overhaul and test facilities in the event user prefers to
return pumps for inspection or overhaul. Pumps that have been factory-overhauled are normally tested
and warranted “as-new” for a period of one year from date of shipment. For either field service or
factory overhaul assistance, contact your local Imo Sales Office or representative at the
Technical/Customer Service Department in Monroe, NC, USA.
Most pumps have repair kits available. Minor Repair Kits are used to repair leaking seals, bad bearings
and/or for re-assembly after pump tear-down. They include (as applicable) pump shaft seals, packing,
all gaskets/O-rings and bearings. Major Repair Kits are sufficient to rebuild completely worn-out pumps
to “as-new” condition. They include all parts found in Minor Repair Kits plus all major internal parts
subject to wear. Since kits have all necessary parts, it is preferred that they be purchased rather than
selecting individual parts. When parts are individually selected from Parts List, some needed
components are often overlooked. In addition, mixing worn or used parts with new parts risks rapid
wear and shortened service life from new parts.
Summary of Contents for IMO C324AXFX-12005
Page 13: ...13...