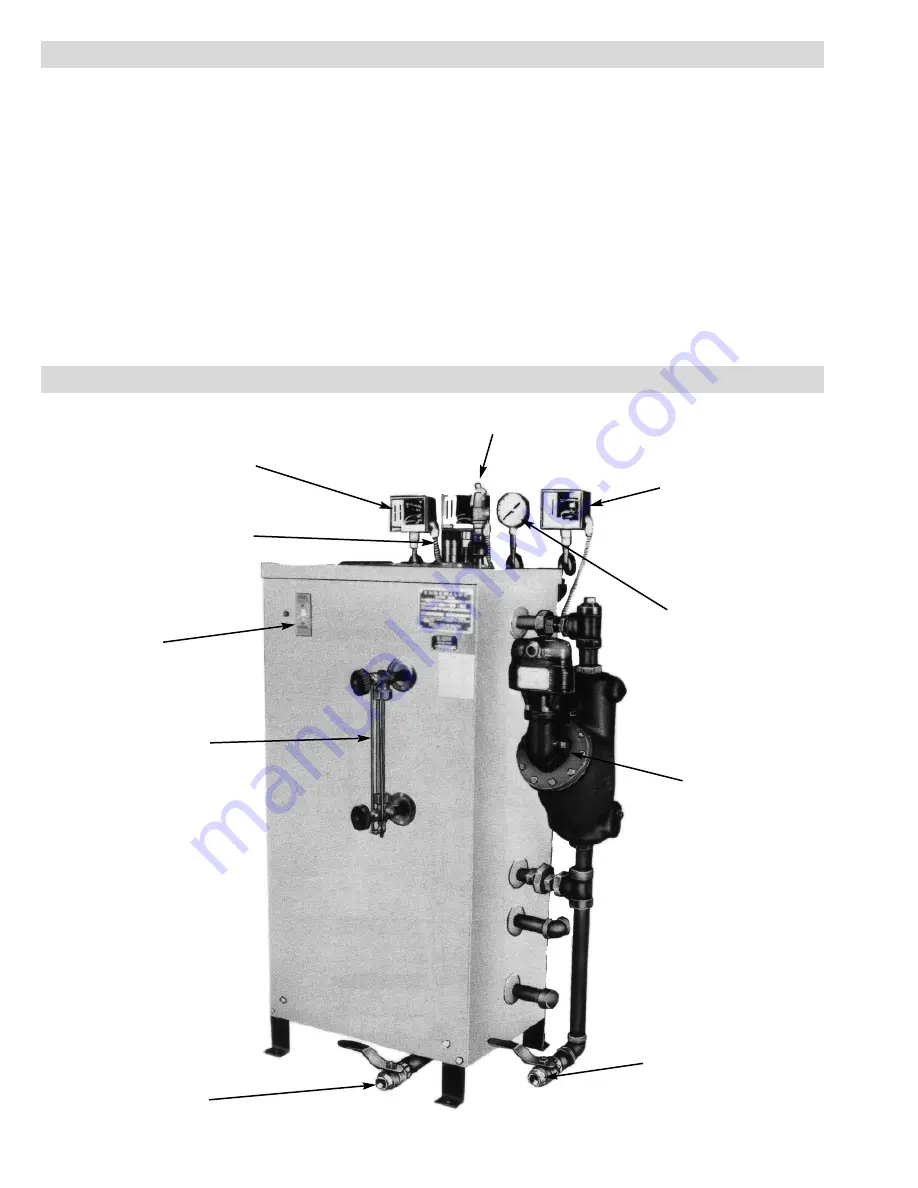
18
MAINTENANCE
RENEWAL PARTS IDENTIFICATION
Drain Blowdown Valve
Drain Blowdown Valve
Water Level Sight Glass
On/Off Switch and
Pilot Light
Steam Outlet
Operating Pressure Control
Range 10-300 Psi
Safety Valve
Manual Reset High
Limit Control
Pressure Gauge, 0-600 Psi
McDonnell & Miller #194
Low Water Cutoff/Pump
Check Valve/Water Inlet
(not shown)
READ COMPLETELY BEFORE STARTING WORK
1.
Disconnect boiler from electric power supply at
main safety
switch or fuse panel.
Then, turn boiler switch to “off” position.
2.
On automatic feed units, close valve on incoming water line. Drain
boiler completely of water.
3.
Open boiler door to expose heating element.
4.
Disconnect wire (electric) leads connecting element to main power
system of boiler. Again note wire connections to facilitate
reassembly. Proceed to remove (6) 5/16-18 bolts from flange.
5.
Thoroughly clean boiler flange of all foreign material. Be certain
no part of old gasket remains on boiler flange.
6.
Apply “Slic-Tite” Gasket Compound or equal to both surfaces of
new gasket with supplied replacement element. Proceed to install
element flange assembly with gasket between boiler flange and
element flange. In doing this, be careful to align flange holes so
wire connection terminals on element assembly are in line with
previously disconnected wire leads to facilitate easy connections.
7.
When all (6) flange bolts are tight, connect all wires to terminals.
Make certain wires are clean and bright to assure good electrical
contact and nuts on screws are firmly secured.
WARNING:
Avoid use of chemical cleaning com-
pounds. Follow maintenance instructions.
8.
Open water valve so water supply can reach boiler feed mecha-
nism.
9.
Put main safety switch to “on” position.
10.
Turn boiler to “on” position.
11.
As boiler automatically refills, observe the new flange assemble
for possible leaks. If water is noticed, to bolts must be retightened.
Before doing this, turn the boiler off at the main fuse safety switch.
12.
As boiler is heated to working pressure, check flange assembly
again for leaks.
WARNING:
Avoid the use of chemical cleaning com-
pounds. Follow maintenance instructions