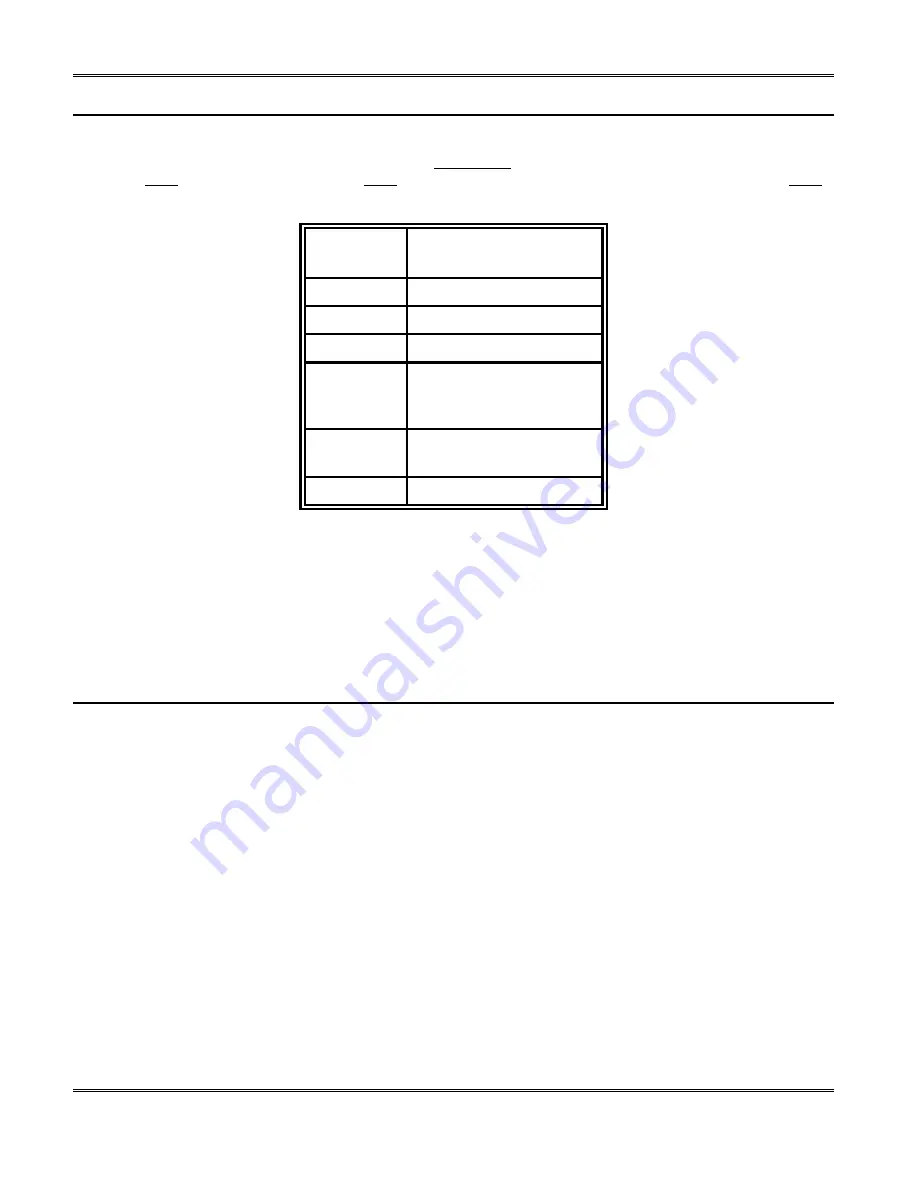
2 . G e n e r a l D e s c r i p t i o n
CHRISTIE INC. - 35/70 Service/PM Manual
July, 1997
System Status
The system status identifies the show being played and the current action of the projector. This value is displayed in the
rightmost two positions of the frame counter LED. The current show is the rightmost character of the two-character value,
and the status is the leftmost character. The status identifies the type of operation the projector is executing. Valid status
values and their meanings are shown in Table 2.4.
System
Status
Meaning
8
Searching for Cue
A
Parked at Cue Point
0
Stopped
1
Moving Forward at or
approaching Cine Speed,
Douser Closed
3
Moving Forward at Cine
Speed, Douser Open
B
Not Ready
Table 2.4: System Status Values
Thus, a value of
A2
indicates that the projector is parked at the cue point for Show #2.
The system status is output over the RS-232 interface in response to an
OUTPUT STATUS
command (see Section 0).
Normally, the show controller receives the system status. When the system is operating in DEBUG mode, the system
status is displayed on the service terminal.
The
35/70
Command Set
Projector commands are encoded in a hexadecimal character format. They are sent to the projector by the show
controller, by a service terminal, or from the keypad. Some common commands have been assigned to specific keys on
the command area of the keypad. When operating the 35/70 projector in a MASTER/SLAVE configuration, the serial
communications port on the SLAVE projector connected to the MASTER will lock out certain commands from the
MASTER projector. When in the SLAVE mode, the SLAVE projector will not echo any commands or provide prompts.
In order to accomplish full duplex communications for a MASTER/SLAVE configuration to a show controller, the show
controller will require two separate serial ports.
There are two types of command:
operational
and
diagnostic
. Operational codes are those commands used by the show
controller or an operator during normal projector use. Diagnostic commands are used for debugging or service
adjustment, for setup, and for other special operations. Some diagnostic commands may be used to enable features not
currently implemented on the 35/70 Projector. Appendix A summarizes the entire system command set.
The following information is provided for each command:
•
command name
•
command type (operational:
OP
or diagnostic:
DX
)
•
lock out condition for SLAVE projector commands (
L
)