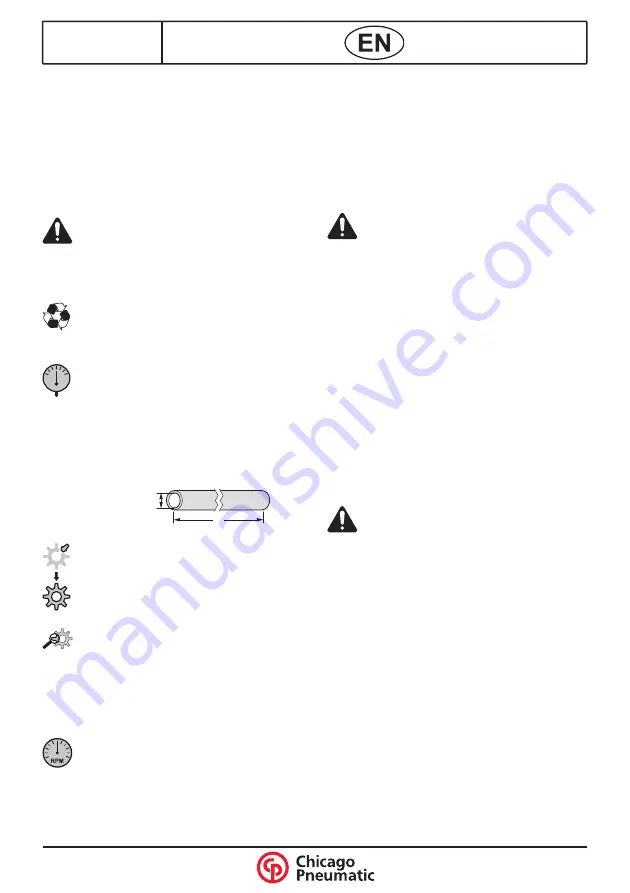
06/2009
8 / 70
6159948630
Issue no: 00
© COPYRIGHT 2009, CP
All rights reserved. Any unauthorized use
or copying of the contents or part thereof
is prohibited. This applies in particular to
trademarks, model denominations, part numbers
and drawings. Use only authorized parts. Any
damage or malfunction caused by the use of
unauthorised parts is not covered by Warranty or
Product Liability.
INSTRUCTIONS
This product is designed for removing
material using abrasives. No other
use permitted. For professional use
only. Before servicing the power tool,
the supply of compressed air must be
disconnected or shut off.
When disposing of components,
lubricants, etc … ensure that the
relevant safety procedures are carried
out.
The tool is designed for a working
pressure of 6.3 bar (90 psig). The
compressed air must be clean. The
installation of a
fi
lter is recommended.
For maximum ef
fi
ciency and
performance, comply with the
speci
fi
cation of the air hose (antistatic
hose).
A: Ømini = 10mm (3/8")
B: 7 m max.
A
B
The use of spare parts other than those
originally supplied by the manufacturer
may result in a drop in performance or
in increased maintenance and level of
vibration and in the full cancellation of
the manufacturer’s liability.
To obtain maximum ef
fi
ciency from the
pneumatic tool, preserve its features
and avoid repeated repairs, a routine
inspection and repair programme are
recommended at least every 1000
hours, the intervals between the various
inspections depending on the amount of
exertion on the power tool.
Check the free speed of the tool
at regular intervals and after each
operation or maintenance task. Remove
the abrasive to check the speed. The
maximum allowed speed shown on
the tool must not be exceeded and the
vibration level must not be excessive.
MOTOR DISASSEMBLY:
1. Press rotor from rear bearing. Press bearing
from rear bearing plate.
2. Remove cylinder and blades.
3. Remove front bearing plate, spacer from
rotor. Bearing is a slip into front bearing plate.
Motor disassembly complete.
MOTOR ASSEMBLY:
Important: Be sure parts are clean and
in good repair before assembling.
1. Install bearing into bearing plate.
2. Place rotor in soft jaw (bronze or aluminium)
vise with threaded spindle pointing upward.
3. Slip spacer onto rotor.
4. Slip front plate onto rotor.
5. Tighten gear onto rotor (torque 17 N.m /
150in.-lbs)
6. Remove rotor of jaw and install well
lubricated blades into rotor slots. (AIROLENE
OIL (P089507) is recommended by CP for
lubri
fi
cation).
7. Install cylinder over rotor. Be careful at the
position and away from the pin on front plate.
8. Press rear bearing into rear plate. Press
bearing into rear plate assembly onto rotor.
Be sure that pin and air inlet holes lines up
with slot and air inlet holes in cylinder.
Important: Fit must be snug between
plates and cylinders. A loose
fi
t will
not achieve the proper pre-load of
motor bearings. If too tight, rotor will
not turn freely. Rotor must then be
tightly tapped at press
fi
t end so it will
turn freely while still mainting a snug
fi
t.
9. Motor adjustment must be checked. With
motor housing still mounted in vise, pull end
of rotor and twist (10-15 lbs), rotor should
turn freely without drag. If drag or rub is felt,
then deload and return to item 7.
Motor assembly complete.