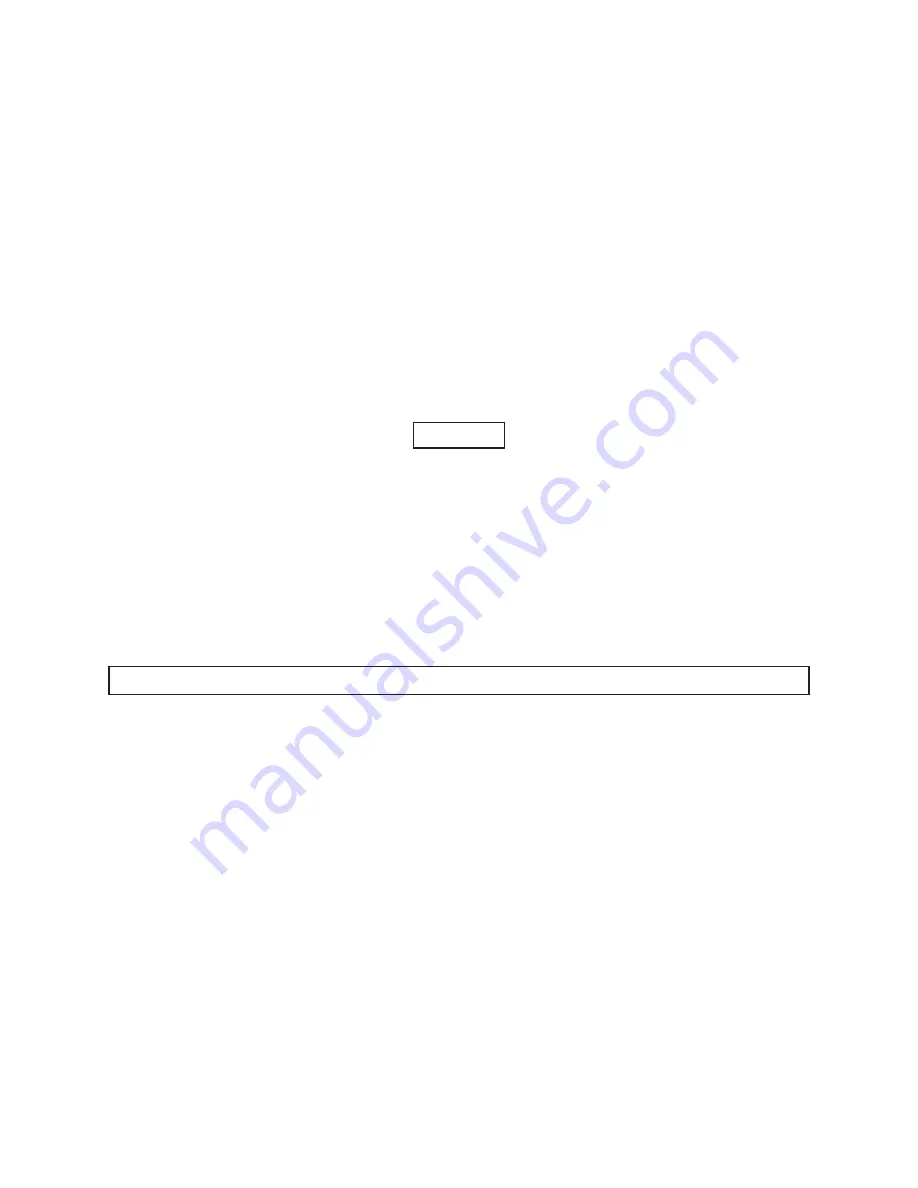
SKU 55594
For technical questions, please call 1-800-444-3353.
Page 5
21.
Maintain welding equipment with care. Keep equipment clean and dry.
Properly maintained equipment is less likely to malfunction and is easier to
control. Do not use damaged welding equipment. Tag damaged equipment “Do
not use” until repaired.
22.
Check for misalignment or binding of moving parts, breakage of parts, and
any other condition that may affect the equipment’s operation. If damaged,
have the equipment serviced before using.
Many accidents are caused by
poorly maintained equipment.
23.
Use only accessories that are recommended by the manufacturer for your
model.
Accessories that may be suitable for one type of welding equipment may
become hazardous when used on another type of equipment
SERVICE
24.
Equipment service must be performed only by qualified repair personnel.
Service or maintenance performed by unqualified personnel could result in a risk
of injury.
25.
When servicing welding equipment, use only identical replacement parts.
Follow instructions in the
“Inspection, Maintenance, And Cleaning” section
of this manual.
Use of unauthorized parts or failure to follow maintenance
instructions may create a risk of electric shock, burns, or other injury.
SPECIFIC SAFETY RULES
1.
Maintain a safe working environment.
Keep the work area well lit. Make sure
there is adequate surrounding workspace. Always keep the work area free of
obstructions, grease, oil, trash, and other debris. Do not use the Welder in areas
near flammable chemicals, dusts, and vapors.
2.
Maintain labels and nameplates on the Welder.
These carry important
information. If unreadable or missing, contact Harbor Freight Tools for a
replacement.
3.
Prevent eye injury and burns.
Wearing and using personal safety clothing and
safety devices reduce the risk of injury. Wear ANSI approved safety impact
eyeglasses with a welding helmet featuring at least a number
10
shade lens
rating. Leather leggings, rubber soled, fire resistant shoes or boots should be
worn when using this Welder. Do not wear pants with cuffs, shirts with open
pockets, or any clothing that can catch and hold molten metal or sparks. Keep
clothing free of grease, oil, solvents, or any other flammable substances. Wear
dry, insulating gloves and protective clothing. Wear an approved head covering