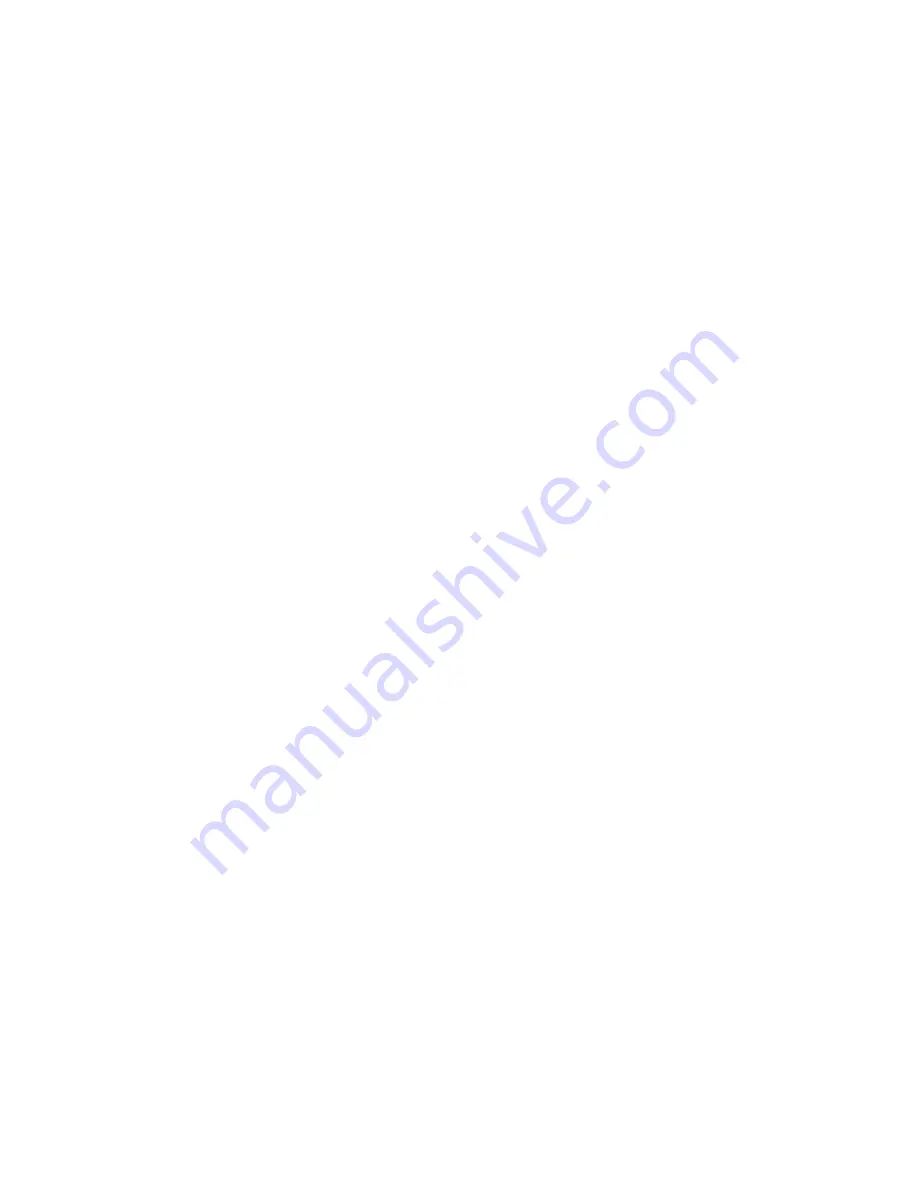
5
INSTRUCTIONS
Anti-Roll Bar Welded Assembly
Anti-roll bar splined tube adapters must be correctly indexed to one another when welded.
1. To determine correct tube length, measure the inside width of the axle brackets and subtract 6-1/8
(6.125) inches.
2. Drill a 5/16” hole through both walls of the anti-roll bar tube 1/2” from each end. These holes will
be used to rosette weld the splined adapters to the center tube.
3. Insert one of the splined adapters into the center tube. Weld the holes, fi lling the hole from the
adapter to outer surface of the tube. This is a rosette weld. You can now weld the circumference of
the joint. This needs to be a good quality weld.
4. After the weld is completely cooled, slide the fi rst billet arm onto the adapter. Position the arm with
the pinch-bolt head up. Secure arm with a socket head cap screw and high collar lock washer.
5. Slide the second arm onto the loose adapter with pinch-bolt head up, then tighten the bolt.
6. Insert the second splined adapter with arm attached, into the anti-roll bar tube. Set the assembly
on a fl at surface with both arms forward. This will index the splines and keep the billet arms fl at to
each other.
7. Rosette weld the second splined adapter to the center tube through both holes. Once the rosette
welds are complete, remove both billet arms and weld the circumference on the second joint. This
needs to be a good quality weld.
Summary of Contents for 5806-U10
Page 2: ...2 ...
Page 3: ...3 ...
Page 13: ...13 ...
Page 14: ...14 NOTES ...
Page 15: ...15 NOTES ...