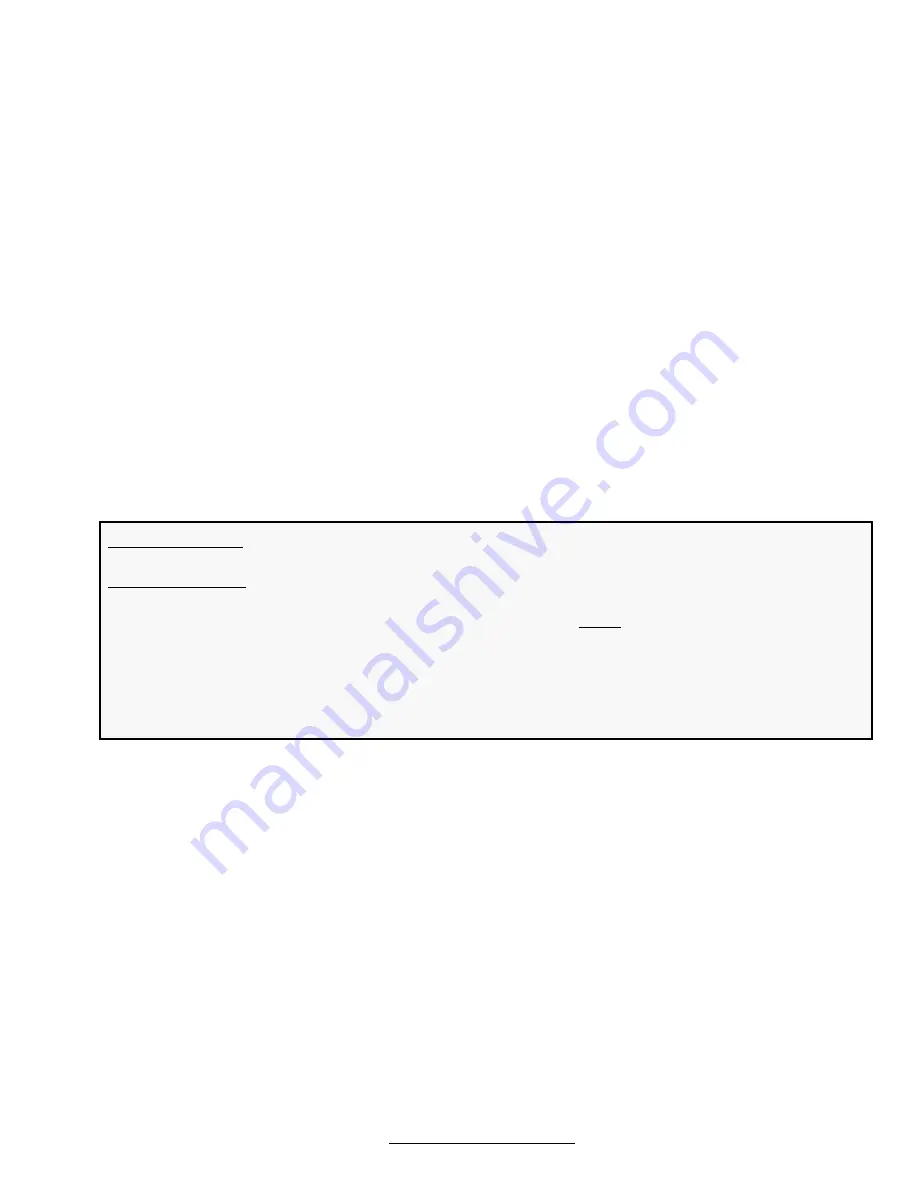
v
Continued on next page.
Champion Industries (herein referred to as the “The Company”), 3765 Champion Blvd., Winston-
Salem, North Carolina 27105, and 2674 N. Service Road, Jordan Station, Ontario, Canada, L0R
1S0, warrants machines, and parts, as set out below.
Warranty of Machines:
The Company warrants all new waste processing machines of its
manufacture bearing the name “Champion”, “Trisys”, or “Champion-Trisys” and installed within
the United States and Canada to be free from defects in material and workmanship for a period of
one (1) year after the date of installation or fifteen (15) months after the date of shipment by the
The Company, whichever occurs first. Warranty registration must be submitted to the The Company
within ten (10) days after installation either online at the Champion Industries website (http://www.
championindustries.com/warranty-registration or by fax to (336) 661-1660 in the USA or (905) 562-
4618 in Canada. The Company will not assume any responsibility for extra costs for installation in
any area where there are jurisdictional problems with local trades or unions.
If a defect in workmanship or material is found to exist within the warranty period, The Company,
at its election, will either repair or replace the defective part or accept return of the machine for
full credit. In the event that The Company elects to repair, the labor and work to be performed in
connection with the warranty shall be done during regular working hours by a Champion authorized
service technician. Defective parts become the property of The Company. Use of replacement parts
not authorized by The Company will relieve The Company of all further liability in connection with
its warranty. In no event will The Company’s warranty obligation exceed The Company’s charge for
the machine.
Approved Waste: Only food, paper napkins, paper towels, and carboard waste are approved
for loading into the machine.
Prohibited Waste: Examples of prohibited waste that must not be loaded into the machine
and not covered by the warranty include, but are not limited to:
a. Flatware, service ware, plastics, large bones, raw bones, (shells: clam, oyster, mussel,
shrimp,crab, lobster, scallop, walnut, peanut, pecan, almond, or any other type of shell not
listed), wood, rags, or nitrile gloves.
b. Loading bulk quantities of waste from tubs, garbage cans, or other large containers directly
into the machine or feed troughs.
c. Metal of any type.
The following are not covered by the warranty:
a. Clogs or damage to any part of the machine due to the loading of prohibited waste.
b. Replacement of fuses or resetting of overload breakers.
c. Opening or closing of utility supply valves or switching of electrical supply current.
d. Cleaning of valves, strainers, screens, nozzles, or spray pipes.
e. Performance of regular maintenance and cleaning.
f. Damages resulting from water conditions, accidents, alterations, improper use, abuse,
tampering, improper installation, or failure to follow maintenance and operation procedures.
Examples of the defects not covered by the warranty include, but are not limited to: (1) Damage
to the exterior or interior finish as a result of the above, (2) Use with utility service other than
that designated on the rating plate, (3) Improper connection to utility service, (4) Inadequate or
excessive water pressure, (5) Corrosion from chemicals dispensed in excess of recommended
concentrations, (6) Failure of electrical components due to connection of chemical dispensing
equipment installed by others,
(7) Leaks or damage resulting from such leaks caused by the installer, including those at machine
trough connections or by connection of chemical dispensing equipment installed by others, (8)
Failure to comply with local building codes, (9) Damage caused by labor dispute.
LIMITED WARRANTY AGREEMENT