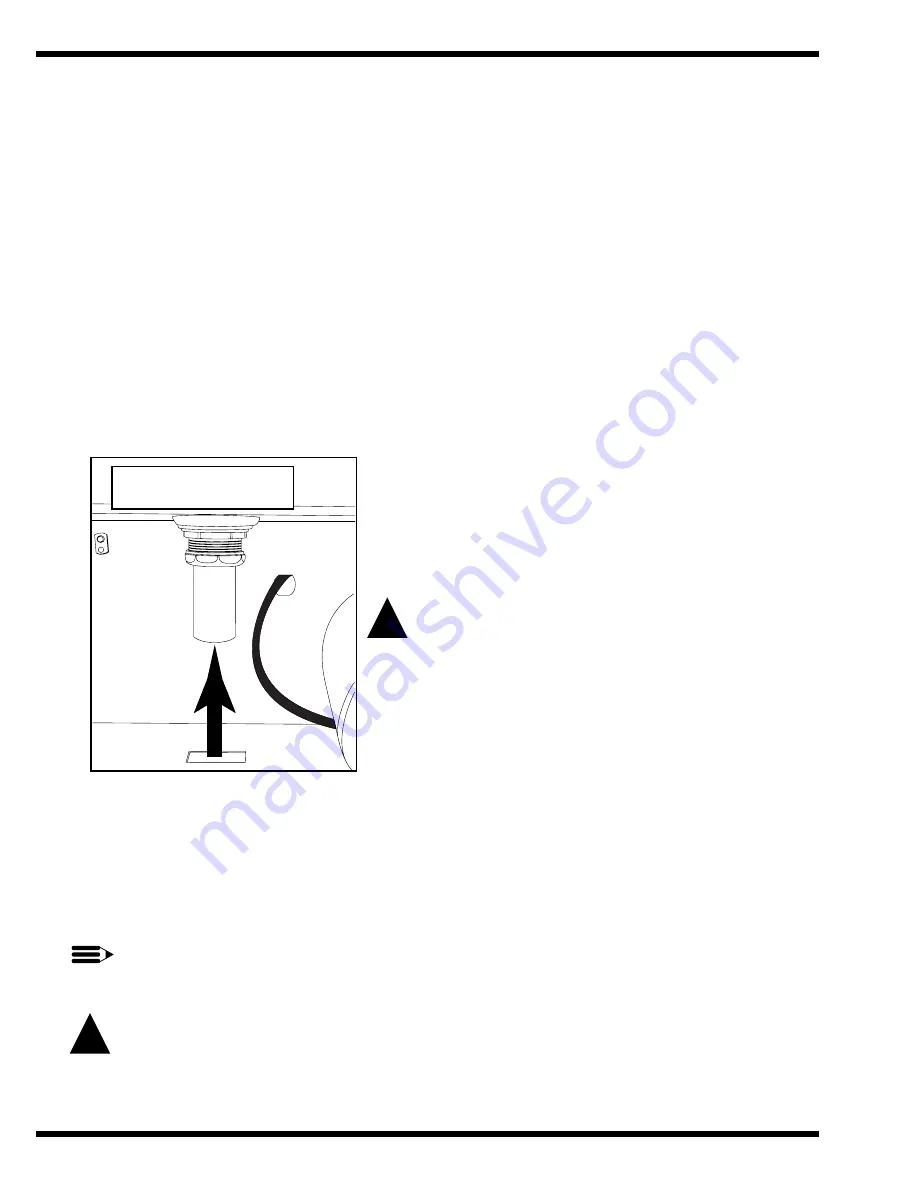
Water Connections (cont’d)
4.
A 3/4" Pressure Regulating Valve (PRV), should be installed on the incoming water supply
line if water flow pressure exceeds 20-22 psi/138 Kpa.
A PRV is standard equipment on Model D-HB.
A PRV is not standard equipment on Models D-H1 and D-LF.
The PRV may be obtained locally or direct from Champion.
Drain Connections
Refer to Fig. 5 for the location of the machine drain.
1.
Models D-HB, D-H1, and D-LF are GRAVITY DRAIN machines equipped
with a 1-1/2" hose connection point.
• Drain height for ALL MODELS must not exceed 11" [280mm] above floor level.
WARNING:
Connection of the machine to a drain line
higher than the machine drain height
will prevent the machine from draining properly.
Ventilation
NOTE:
Ventilation must comply with local sanitary and plumbing codes.
CAUTION:
Exhaust air should not be vented into a wall, ceiling, or concealed space of a building.
Condensation can cause damage.
12
INSTALLATION
!
Figure 5
D-HB, D-H1, D-LF
1-1/2" Drain Connection
Lower Center of Machine
1-1/2" Drain Connection
11” [280mm] above floor level
!
Summary of Contents for D-H1M3
Page 31: ...29 REPLACEMENT PARTS REPLACEMENT PARTS ...
Page 62: ...1 2 3 60 REPLACEMENT PARTS Figure 37 D HB D H1 D LF Dishracks and PRV ...
Page 64: ...62 REPLACEMENT PARTS THIS PAGE INTENTIONALLY LEFT BLANK ...
Page 65: ...63 ELECTRICAL SCHEMATICS ELECTRICAL SCHEMATICS ...
Page 68: ......
Page 69: ......