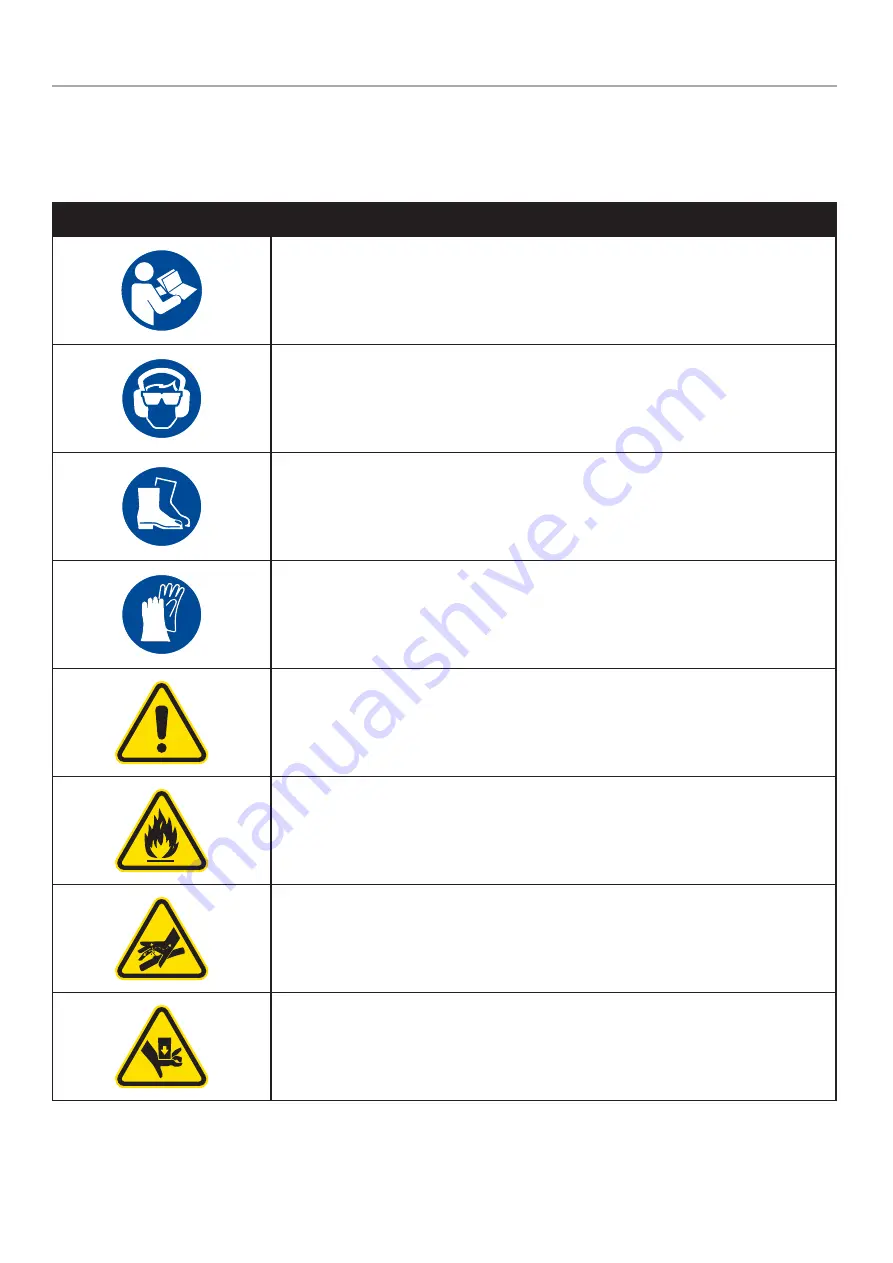
9
100624 - 9 TON FULL BEAM LOg SPLiTTER
iMPORTANT SAFETY iNSTRUCTiONS
Safety Symbols
Some of the following symbols may be used on this product. Please study them and learn their meaning. Proper interpretation of these
symbols will allow you to more safely operate the product.
SYmBOL
mEaNING
Read Operator’s manual.
To reduce the risk of injury, user must read and understand operator’s
manual before using this product.
Eye and Ear Protection
. Always wear safety goggles or safety glasses with side shields, and as
necessary a full face-shield as well as full ear protection when operating this product.
Footwear.
Always wear safety shoes or heavy boots when operating the machine.
Gloves.
Always wear nonslip, heavy-duty protective gloves when operating this product.
Safety alert.
Precautions that involve your safety.
Risk of Fire.
Fuel and its vapors are extremely flammable and explosive. Fire can cause severe
burns or death. Do not add fuel while the product is operating or still hot.
Skin Injection hazard.
High pressure hydraulic oil can inject under your skin.
Make sure all fittings are tightly secure before applying pressure. Relieve system
pressure before servicing.
Always keep hands away from the wedge and the ram. Moving parts can crush or cut.
500887