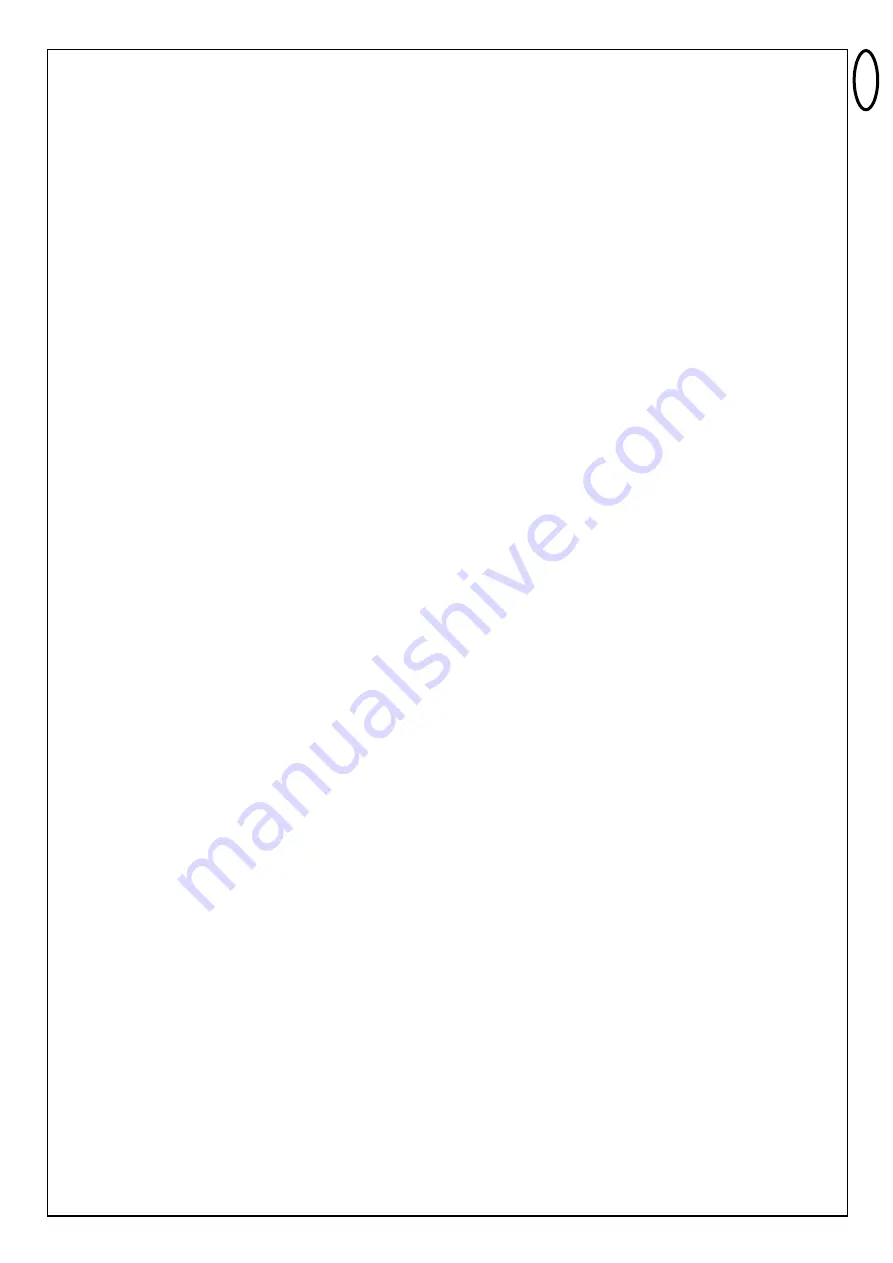
en-1
3
INITIAL OPERATION
BASIC SETTING
Proceed step by step. If you are not sure, start again at the beginning. Take sufficient time to make these settings.
1. Are all components required for operation connected? Motors, photocells, safety contact strip, stop switch.
2. Make sure that nobody is present in the range of the gates.
3. Close the gate/s and attach motor/s. Secure motors with the “R” clip and turn the release lever towards the gate pillar. The
motor/s are now locked.
NOTE:
If attaching the motor/s is not possible, check if spindle travel is sufficient. If not, check tensioning distance. Fittings may
have to be aligned again.
Now connect the mains supply (230V) to the control board.
BASIC SETTING:
1.
Press buttons P1, P2 and P3 simultaneously for approx. 2-3 seconds until yellow LED flashes.
2.
Monitor the gate. Press and hold P1 for 1-2 seconds. The wing with motor 1 opens.
(Do not open gate completely, only short
distances.)
If motor 1 closes, it is wired incorrectly and
the red and blue wires of the motor cable must be inverted. (Caution:
Disconnect Power!)
Repeat steps 1 and 2. Leave gate/s in partially open position.
NOTE:
General operation – if you release the button, the gate will immediately stop. By pressing the button again the gate will
move in the opposite direction until you release the button, and so on.
3. Press and hold P2 for 1-2 seconds. The wing with motor 2 must open. (Do not open gate completely, only short distances.)
If motor 2 closes, it is wired incorrectly and the red and blue wires of the motor cable must be inverted.
(Caution: Disconnect Power!)
Repeat steps 1 and 2. Leave gate/s in partially open position.
NOTE:
The control board is active for this manual setting mode for approx. 20 seconds. If necessary, start again by pressing P1,
P2 and P3 simultaneously.
Now check the following:
1. During opening the front housing must not touch the gate. Stop opening several times and check. If housing touches the gate
dimensions A/B must be checked and if necessary, underlay the gate pillar with flat washers in order to enlarge clearance.
2. Both wings must open completely. Do not open the wings too far! If there are no stops, choose and mark a position for
maximum opening.
3. Both wings must close completely. (Ideally the trolley stops approx. 1 cm before the end of the spindle.) If not, correct
tensioning distance(s).
Wait until learn-LED goes out (20 seconds after a button was pressed).
PROGRAMMING TRAVEL DISTANCES “SIMPLE I”
NOTE:
only with stops in OPEN and CLOSE position
1.
Wings must be closed
2.
Press P1 until wing / motor 1 starts opening (learn-LED flashes)
Automatic programming starts (slow travel)
Wing 1 moves to the stop in OPEN position
Wing 2 moves to the stop in OPEN position
Then wing 2 moves to the stop in CLOSE position.
Then wing 1 moves to the stop in CLOSE position.
When the learn-LED goes out the programming has finished.
PROGRAMMING TRAVEL DISTANCES “SIMPLE II”
NOTE:
If there are no stops at the OPEN position, the wing should be stopped at opening angle of 90 degrees.
1.
Both wings must be closed.
2.
Press P1 until wing / motor 1 starts opening
3.
Press P1 hard when wing / motor 1 reaches OPEN position. Wing 2 starts.
4.
Press P1 hard when wing / motor 2 reaches OPEN position. After that wing 2 closes automatically. The wing 1
closes automatically.
5.
The motors “learn” the CLOSE position automatically.
If required, individual CLOSE positions can be programmed as well. Press P1 hard at the desired CLOSE position for
each wing. When the learn-LED goes out the programming has finished.
Important: Before connecting the control board to the mains the jumper "RADIO" must be off. After connecting the
control board to the mains, the diagnosis LED will flash 7 or 8 times. Nevertheless the control board can be operated.
Note:
If the wings are closing instead of opening, the operators are are connected the wrong way. Invert red and blue cable.