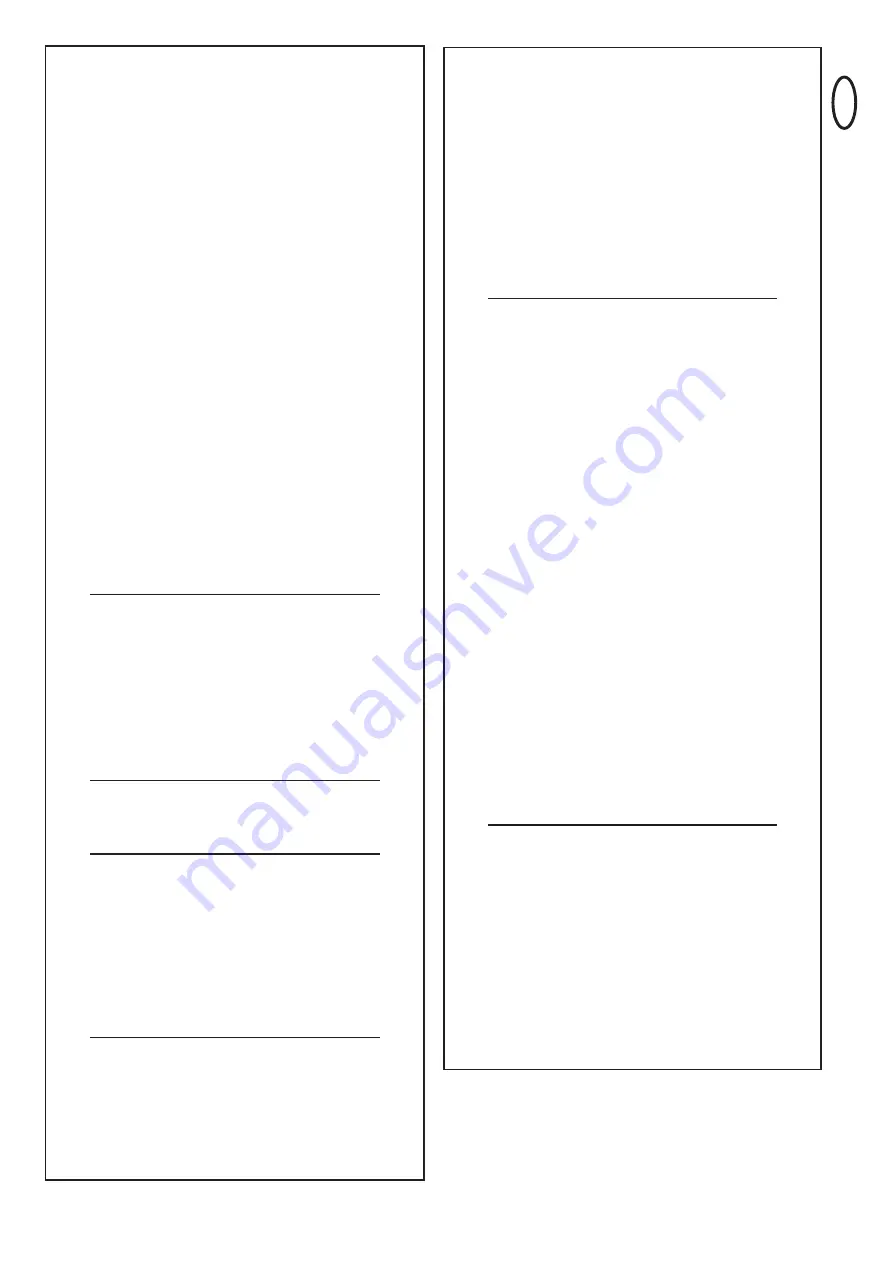
3-GB
GATE FITTING
The gate fitting must be installed so that it is horizontal
relative to the post bracket. The distance between the gate
bracket and post bracket is referred to as the "arm span".
When the gate is closed, the drive mechanism is 95%
extended. When the gate is opened, the drive mechanism is
5% extended. Fully retracting or extending the
plunger/spindle in operation (with gate) damages the drive
mechanism and voids the warranty. It is absolutely imperative
to comply with the required arm span under all
circumstances!
For steel gates, fixings should be welded on or through
bolted. When through bolting the gate, use large washers or
a plate on the other side. The drive mechanism exerts an
extremely high force on this joint.
Fixings must be through bolted for wooden gates. Wood
deflects under load and the bolt will become loose. Due to
movement caused by repeated loading, the wood deflects
more and more until the gate no longer closes correctly and
has to be repaired.
Fit a reinforcing plate from the outside and one on the inside
so that the wood cannot deflect and the joint cannot become
loose.
Thin wooden gates without a metal frame must also be
reinforced in order to withstand continuous stresses
(e.g. type F).
Tip for professionals: The drive mechanism can also be used
for light "rising" gates or light gates with hinge bands offset
up to 8º (gate weighing 100 kg). This subjects all fittings to
extreme stresses and can cause the gate to run erratical.
Special attention must be paid to safety, especially in the
case of rising gates. It is recommended that only experienced
gate installers adopt this method.
RELEASE
The drive mechanism can be released. The gate can then be
opened and operated manually (power failure). With a new
drive mechanism, the release action may sometimes feel
stiff/jerky. This is normal and has no effect on function.
Release:
Insert the key in the cylinder lock and turn it 180
degrees. Then turn the release lever 180 degrees – done!
Engage:
Turn the lever glockwise. As soon as the gate
moves or the drive runs, the gear locks again. Use the lock to
protect the lever against unauthorized release.
INSTALLING THE DRIVE ARMS
Release the drive. Push the released drive onto the fittings
and secure it by using the supplied bolts and rings.
WIRING
The 4-pole connecting cable is approx. 80 cm long and is laid
in a curve to the controller or a watertight distribution box
located above ground. An approved cable is permanently
installed from the distribution box onwards. The capacitor can
be connected inside the distribution box or in the controller.
Connection:
Connect the capacitor across terminals OP and
CL. OP and COM produce rotation direction A. CL and COM
produce reversed direction of rotation.
Always remember to
earth the installation
.
MAINTENANCE WORK
The drive mechanism is maintenance free. Check that the gate
fittings and the drive mechanism are securely fixed at regular
intervals (monthly). Release the drive and check that the gate
functions properly. Unless the gate runs smoothly it will not
operate correctly with the drive mechanism. The drive cannot
eliminate the problems caused by a gate that does not work
satisfactorily.
ELECTRONIC CONTROL
The control board should be the last item to be connected, i.e.
mounting the motors, laying the necessary cable and fitting
light barriers or contact strips. If installation is to be performed
in a permanent location, a means of disconnecting the
equipment from the mains supply with a contact clearance of at
least 3 mm is needed (master switch).
Please note:
in these instructions, relay contacts are
designated NC
(normal closed)
or NO
(normal open)
.
• NC contacts are closed and open
• NO contacts are open and close
Humidity and water will destroy the control board. Always
make sure that water, humidity and condensation cannot
enter the control box. It is vitally important that all openings
and cable glands are sealed so that they are watertight.
ELECTRICAL INSTALLATION
Installing the electronic control board:
the motor control
board is a microprocessor-controlled electronic appliance
featuring state-of-the-art technology. It is equipped with all
the connecting options and functions needed to guarantee
safe operation. An overview of the wiring plan is shown in
fig. 8
. The control box incorporating the motor control board
should be installed with the cable intakes pointing
downwards
fig. 9B
. It should not be continuously exposed to
direct sunlight. The electronic equipment enables the pull
and push forces to be set with great accuracy. If installed
and set correctly, the gate/door can be stopped manually.
When in motion, the gate/door can be stopped at any time by
operating the remote control, the push-button or the key-
operated switch.
The gate/door wing must be fitted with a robust end
stop for the 'OPEN' and 'CLOSED' positions as the
gate/door drive has no limit switches.
Current distribution:
the cable leading from the drive arm
must be laid in a standard watertight distribution box. A
permanently installed cable can be laid from the distribution
box to the control unit. It is often possible to wire the drive,
which is fixed beside the control unit directly to the box.
Never install distribution boxes underground.
Generally speaking, the following minimum cable cross-
sectional areas must be adhered to:
100-230Volt
1.5mm
2
or more
0-24Volt
0.5mm
2
or more
Tips:
Bell wire is often problematic in practical use because
it loses too much voltage if long lengths of wire are used.
Segregate the cables in cable trunking, i.e. motor cable and
light barrier cable, especially in the case of key-operated
switches and ON switches (from the house wiring system) to
prevent interference where long lengths of cable are used.
OVERVIEW OF CONNECTIONS
Motors:
connect the control unit exactly in accordance with
the overview of connections. The gate/door wing, which
opens first, must be motor 1 (M1) and when it first moves it
must OPEN the gate/door. If it closes the gate/door, swap
terminal 6 with terminal 8 or, in the case of motor 2 (M2),
swap terminal 9 with terminal 11.
The capacitor supplied as standard must be installed
between cables 6 and 8 and 9 and 11 (for space reasons,
the capacitor can also be installed in a distribution box).
Make sure that its terminals are properly connected and that
there is a good electrical connection. The capacitor
determines the force which the motor subsequently
develops.